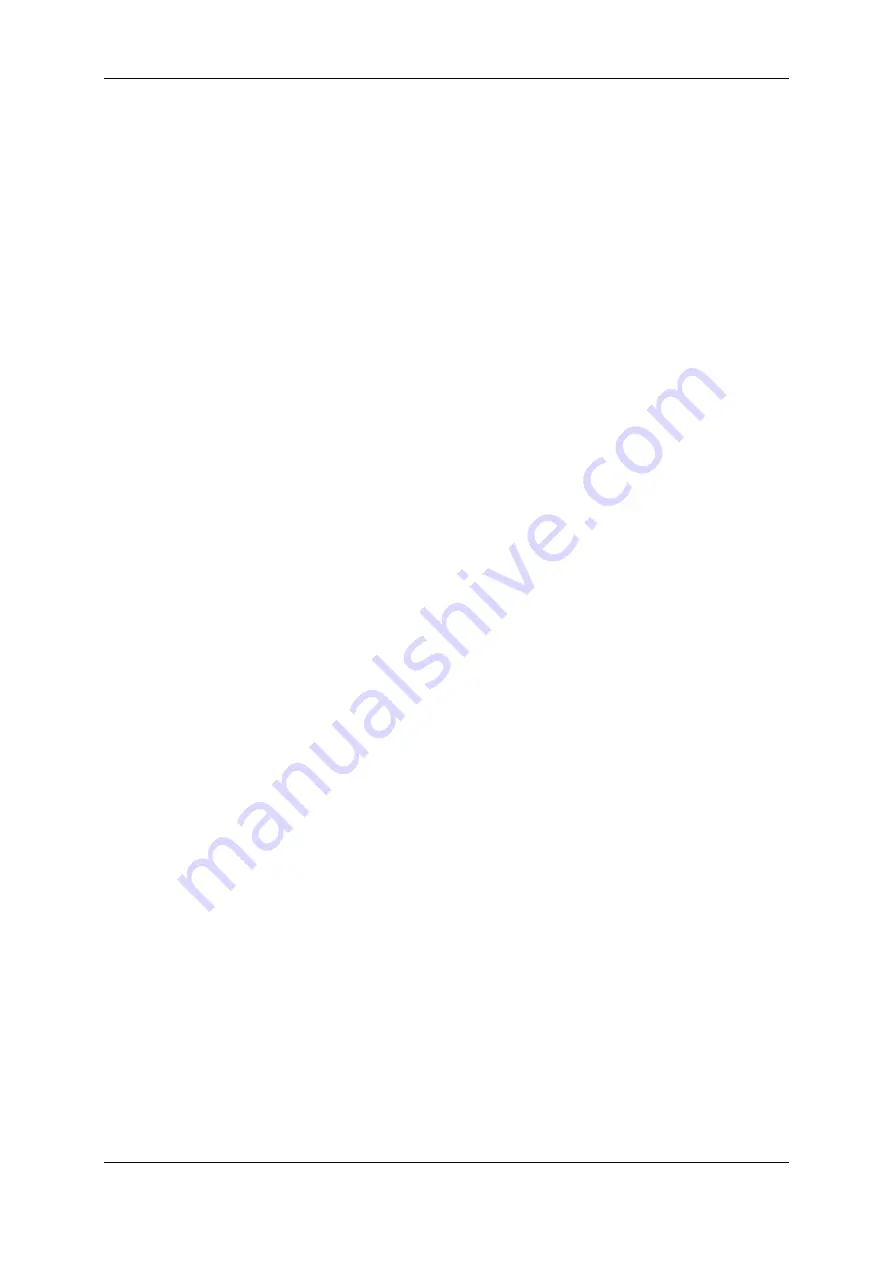
Page 22
PROFIBUS-DP and PROFIdrive
PROFIBUS-Manual Servo positioning controller DIS-2 48/10 FB
Version 2.0
Due to the extensive diagnosis functions of DP, errors can be localized very quickly. Diagnosis
messages are transmitted on the bus and collected at the master.
DP master class 1 (DPM1) is a central control system which exchanges information cyclically with
decentralized stations (slaves) in a defined message cycle. Typical DPM1 devices are programmable
logic controls (PLCs) or PCs, for example.
DP master class 2 (DPM2) devices are engineering, project or operating devices. They are used for
start-up, maintenance and diagnosis, to configure the connected devices, to evaluate measured values
and parameters and to check the device status. A DPM2 device does not have to be permanently
connected to the bus system.
A slave is peripheral device (I/O device, drive, etc.) which reads in process information and/or uses
output information to intervene in the process. In terms of communication, slaves are passive devices
as they reply only to direct requests from a DPM1 or DPM2 device.
4.2
Basic functions of DP-V0
The central control system (master) cyclically reads the input information from the slaves and cyclically
writes the output information to the slaves. The bus cycle time should be shorter than the program
cycle time of the central automation system which is in the range of about 10 ms for many applications.
A high data throughput alone is not enough for successful use of a bus system. Other factors, such as
ease of operation, good diagnosis facilities and a fail-safe transmission method are more important.
These characteristics have been combined successfully in DP-V0.
DP needs only about 1 ms to transmit 512 bits of input data and 512 bits of output data distributed to
32 connected devices. DP transmits input and output data in a message cycle. Useful data are
transmitted using the SRD service (Send and Receive Data Service) of ISO/OSI layer 2.
To transmit data using the DP-V0 service, the amount and the meaning of the data to be transmitted
have to be defined both for the master and for the slave. When a PROFIBUS connection is configured,
the user has to make this definition before the field bus connection can be parameterized at both ends.
4.3
PROFIdrive overview
The “PROFIBUS profile for drive technology” or short PROFIdrive is a manufacturer standard for
implementing PROFIBUS interfaces for drives. It has been defined by the association of PROFIBUS
users. Just like CANopen, its aim is to offer the user a defined interface for programming servo
controllers. This interface should be as manufacturer-independent as possible.
PROFIdrive specifies the configuration, diagnosis, data exchange and state machines with a
PROFIBUS master. Furthermore, so-called application classes are defined. There are different