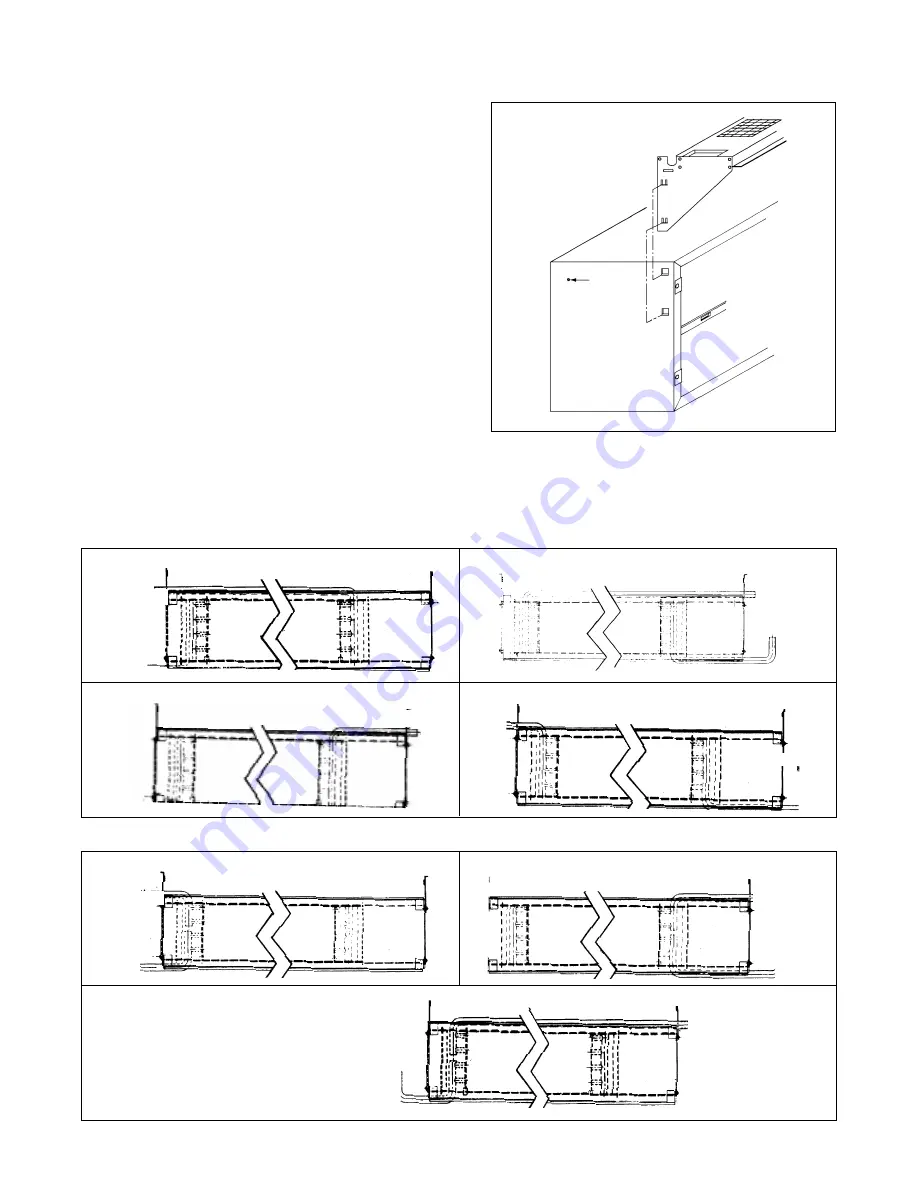
IM 422-4 / Page 7 (Rev. 5/99)
Heat Section Installation
The heat section is designed to be “snapped” into the top of the
wall sleeve (see Figure 6). There are four square holes provided
in the wall sleeve, two on each side, for coil attachment. Assem-
bly the heat section to the wall sleeve as follows:
1. Unpack the heat section and inspect for any shipping
damage. Report any damage found to the carrier.
2. Check the heat section against the plans to make certain the
coil supplied has the connections match the specifications.
3. Firmly attach the heat section to the wall sleeve by lining up
the heat section hooks with the square holes supplied in the
wall sleeve. Snap the heat section in place by exerting pres-
sure downward.
4. The valve is always connected to the supply side of the coil.
There are seven possible coil arrangements available. Each
is shown below. Select the illustration below that matches the
coil supplied and pipe it according to the illustration. Install
valve and other accessories including air vents, steam traps,
stop balance valves, etc., as specified by the design engIneer.
5. For valve installed on right side of the unit, make electrical
connection to matching cap extending from the control box.
For left side valve, make electrical connection to cap mounted
to left side of chassis.
Note: When the heating medium is steam, the supply connec-
tion should be attached to the uppermost tube and the return to
the lower tube. The coil is pitched in the casing to allow drainage
of condensate.
When the heating medium is hot water, the supply connec-
tion should be made to the lowermost tube and the return to the
uppermost tube. Hot water coils should be “flooded” to minimize
air entrapment.
Factory
Supplied
Holes (2)
Wall Sleeve
Hydronic
Heat
Section
Hot Water Coils
Hot Water Coils
Hot Water Coils
Hot Water Coils
Hot Water Coils
Steam Coils
Steam Coils
Steam Coils
Steam Coils
Steam Coils
SUPPLY
RETURN
RETURN
SUPPLY
RETURN
SUPPLY
SUPPLY
RETURN
RETURN
SUPPLY
SUPPLY
RETURN
RETURN OR SUPPLY
RETURN OR SUPPLY