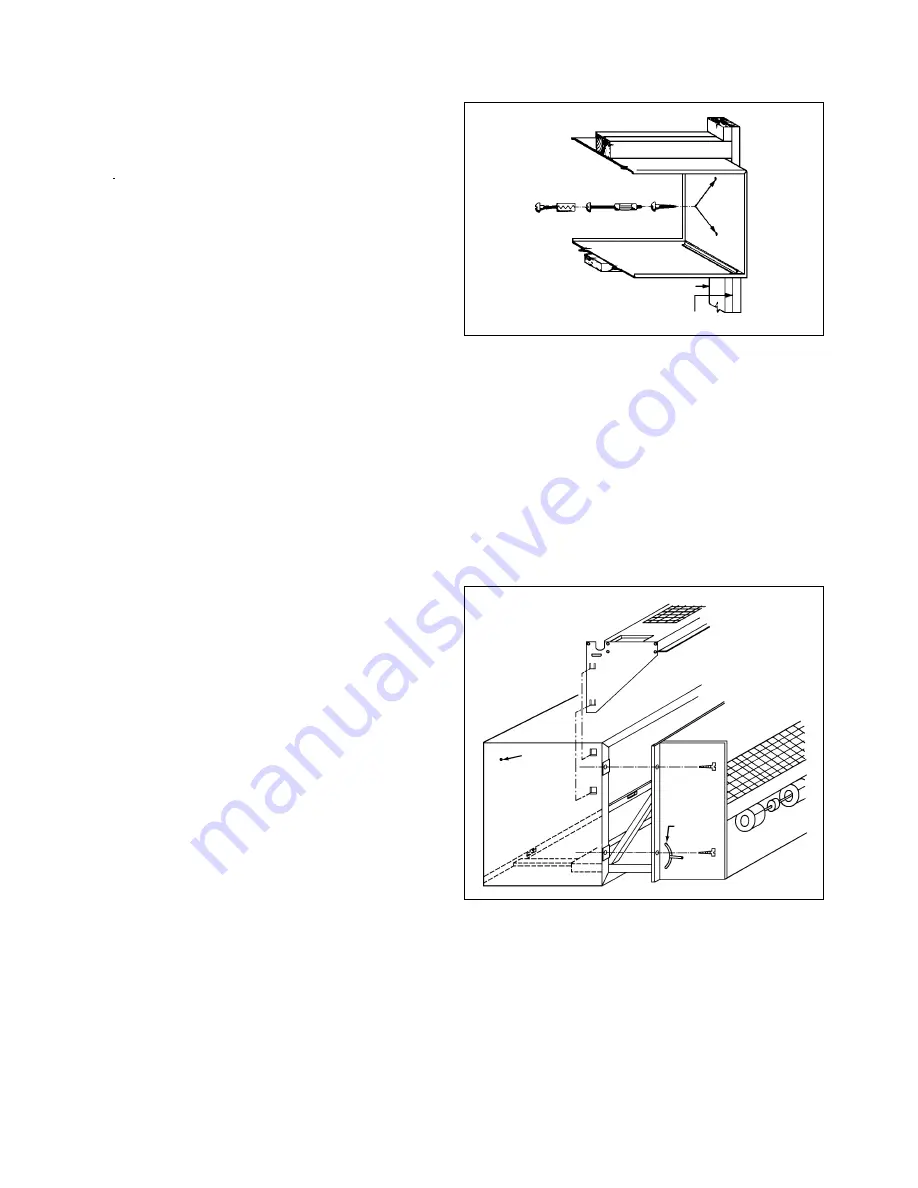
IM 422-4 / Page 8 (Rev 5/99)
Anchoring
Anchoring the wall sleeve in the opening is accomplished as
shown in Figure 14. It is recommended that rubber isolation
washers be used with the fasteners to minimize sound
transmission from the equipment to the wall, at the point of
contact.
A
5
⁄
16
" (8mm) hole is provided on each side, 2" (51mm)
down from the top and 2" (51mm) in from the rear of the wall
sleeve. It may be necessary to drill additional holes in the wall
sleeve to firmly secure it. Caution: Do not drill holes in the
base of the wall sleeve. Use shims between the wall and the
wall sleeve to prevent sleeve distortion during anchoring.
Installation of Cooling Chassis
Correct installation of the cooling chassis is extremely impor-
tant to insure the proper operation of the unit. Install the
chassis as follows:
1. Remove outer carton and inspect for any shipping dam-
age. Report any found to the carrier.
2. Check nameplate data on chassis to insure that the
correct job site distribution has been made with respect
to cooling capacities. Generally, corner rooms require
larger capacities.
3. Remove chassis from carton by pulling evenly on sub-
stantial portion of unit. Caution: Do not pull on evaporator
fan housing, control box or compressor.
4. If wall sleeve has been previously installed, remove
temporary weather panel.
5. Check all fasteners to make certain they have not come
loose during shipment. Do not loosen nuts holding down
compressor; they are set at the factory.
6. Do not lubricate motors before start-up. Motors are
factory lubricated. Consult “Scheduled Maintenance”
section on page 12 for lubrication instructions.
7. Place Tinnerman clips from bag onto wall sleeve. Clips
and mounting screws are enclosed in a bag attached to
the top of the condenser coil cover.
8. If louver has not been previously installed, connect to
wall sleeve as described above.
9. If louver is supplied by others, as illustrated in Figure 4,
page 5, be sure to install foam type gaskets on all sides
of the condenser coil to prevent recirculation or bypass of
condenser air.
10. Slide chassis into wall sleeve until firmly seated against
weather seals of wall sleeve. Caution: Do not push on
Installation of Louvers
1. Remove louver from its shipping carton which also con-
tains a hardware package for mounting the louver.
2. Remove outside weather plug and weather panel from wall
sleeve.
3. Make a temporary handle by looping a piece of flexible
wire or heavy cord through the louver. This enables the
installer to keep a firm grasp on the louver when installing
from inside the room.
4. Push the louver through the opening at the rear of the wall
box, then pull the louver back to the wall sleeve flange so
that the louver studs pass through the holes in the flange.
5. Attach washers and nuts and secure louver in place.
6. If the cooling chassis is not to be immediately installed,
replace the weather panel.
coil surface or control box cover. Make sure the com-
pres
sor tubing does not catch when inserting chassis.
11. Secure chassis to wall sleeve with four (4) sheet metal
screws packaged with the Tinnerman clips.
12. Plug electrical cord into receptacle. Excess cord should
be coiled up neatly and stored in the conditioner.
13. Set the manual damper operator in open or closed
position as desired. On units equipped with the optional
electric fresh air damper, set the “Auto-Off” switch in the
desired position. In “Auto,” the damper is open whenever
the indoor fan motor is running. The “Auto-Off” switch is
located on the bottom front face of the control box.
Expansion
Anchor
Bolt
Molly or
Toggle Bolt
Cripple Stud
Main Stud
Wood
Screw
Factory
Supplied
Holes (2)
Chassis
Damper
Actuator
Hydronic
Heat
Sect.
Wall Sleeve