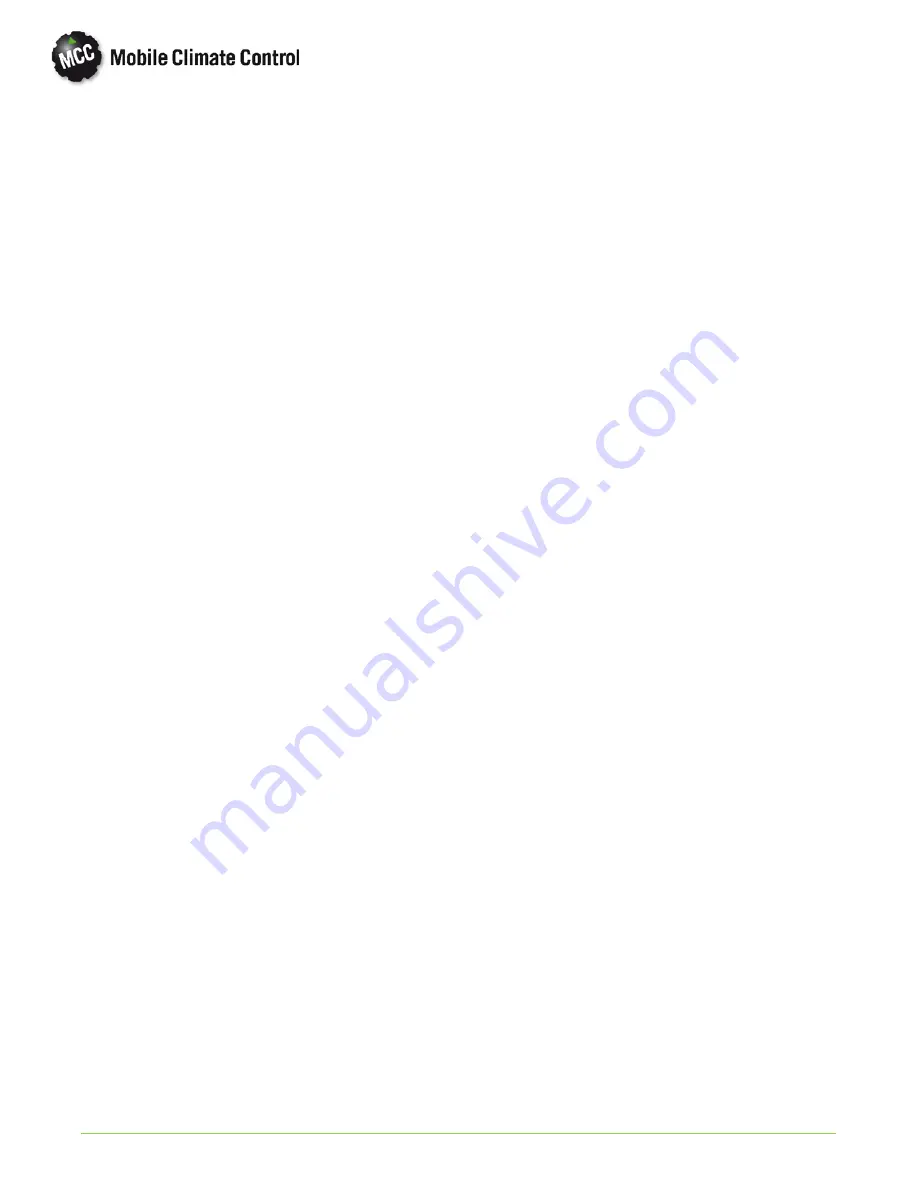
4-8
©
2012 Mobile Climate Control
T-348 Rev. 07/2012
4.7 EVACUATION AND DEHYDRATION
4.7.1 General
The presence of moisture in a refrigeration system
can have many undesirable effects. The most
common are copper plating, acid sludge formation,
“freezing-up” of metering devices by free water, and
formation of acids, resulting in metal corrosion. A
triple evacuation (Refer to paragraph 4.7.4) should
be performed after a major system repair
(compressor,
evaporator,
or
condenser
replacement). A one time evacuation (Refer to
paragraph 4.7.3) should take place after a minor
system repair (replacement of a solenoid valve or a
filter drier).
4.7.2 Preparation
NOTE
Using a compound gauge for determination
of vacuum level is not recommended be
cause of its inherent inaccuracy.
a. Evacuate and dehydrate only after pressure leak
test. Refer to paragraph 4.6.
b. Essential tools to properly evacuate and dehydrate
any system include a good vacuum pump with a
minimum of 6 cfm
(
10.2 m
3
/hr) volume displace
ment, (MCC P/N 07-00176-11), and a good vacu
um indicator (MCC P/N 07-00414-00).
c. Keep the ambient temperature above 60
°
F
(
15.6
°
C) to speed evaporation of moisture. If am
bient temperature is lower than 60
°
F (15.6
°
C), ice
may form before moisture removal is complete.
4.7.3 Procedure for Evacuation and Dehydrating Sys-
tem (One Time Evacuation)
a. Remove refrigerant using a refrigerant recovery
system. Refer to paragraph 4.5.4.
b. The recommended method is connecting lines (re
frigerant hoses designed for vacuum service) as
shown in Figure 4-6.
c. Energize the Liquid Line Solenoid Valve (LSV)
(13) using an external power source (24 VDC).
d. Start vacuum pump. Slowly open valves halfway
and then open vacuum gauge valve (items 22 &
23).
e. Evacuate unit until vacuum gauge indicates 500
microns Hg vacuum.
f. Close off pump valve (23), and stop pump. Wait
five minutes to see if vacuum holds.
g. Remove external 24 VDC from Liquid Line Sole
noid.
h. Charge system. Refer to paragraph 4.8.2.
4.7.4 Procedure for Evacuation and Dehydrating Sys-
tem (Triple Evacuation)
a. Remove refrigerant using a refrigerant recovery
system. Refer to paragraph 4.5.4.
b. The recommended method is connecting lines (re
frigerant hoses designed for vacuum service) as
shown in Figure 4-6.
c. Energize the Liquid Line Solenoid Valve (LSV)
(13) using an external power source (24 VDC).
d. Start vacuum pump. Slowly open valves halfway
and then open vacuum gauge valve.
e. Evacuate unit until vacuum gauge indicates 2000
microns Hg vacuum. Close gauge valve, vacuum
pump valve, and stop vacuum pump.
f. Break the vacuum with nitrogen. Raise system
pressure to approximately 2 psig.
g. Purge the nitrogen from the system.
h. Repeat steps d. thru g. one time.
i. Start vacuum pump and open all valves. Dehy
drate unit to 500 microns Hg vacuum.
j. Close off pump valve (23), and stop pump. Wait
five minutes to see if vacuum holds.
k. Remove external 24 VDC from Liquid Line Sole
noid.
l. Charge system. Refer to paragraph 4.8.2.
4.8 ADDING REFRIGERANT TO SYSTEM
4.8.1 Checking Refrigerant Charge
The following conditions must be met to accurately
check the refrigerant charge.
a. Coach engine operating at high idle.
b. Unit operating fully loaded (six cylinder) in cool
mode for 15 minutes.
c. Compressor discharge (head) pressure to 150
PSIG (R-134a). It may be necessary to block con
denser air flow to raise discharge pressure.
d. Under the above conditions, the system is proper
ly charged when the white balls are floating and a
liquid level is detected in the receiver sight glasses.
Adjust the charge (add or remove) to meet this
condition.