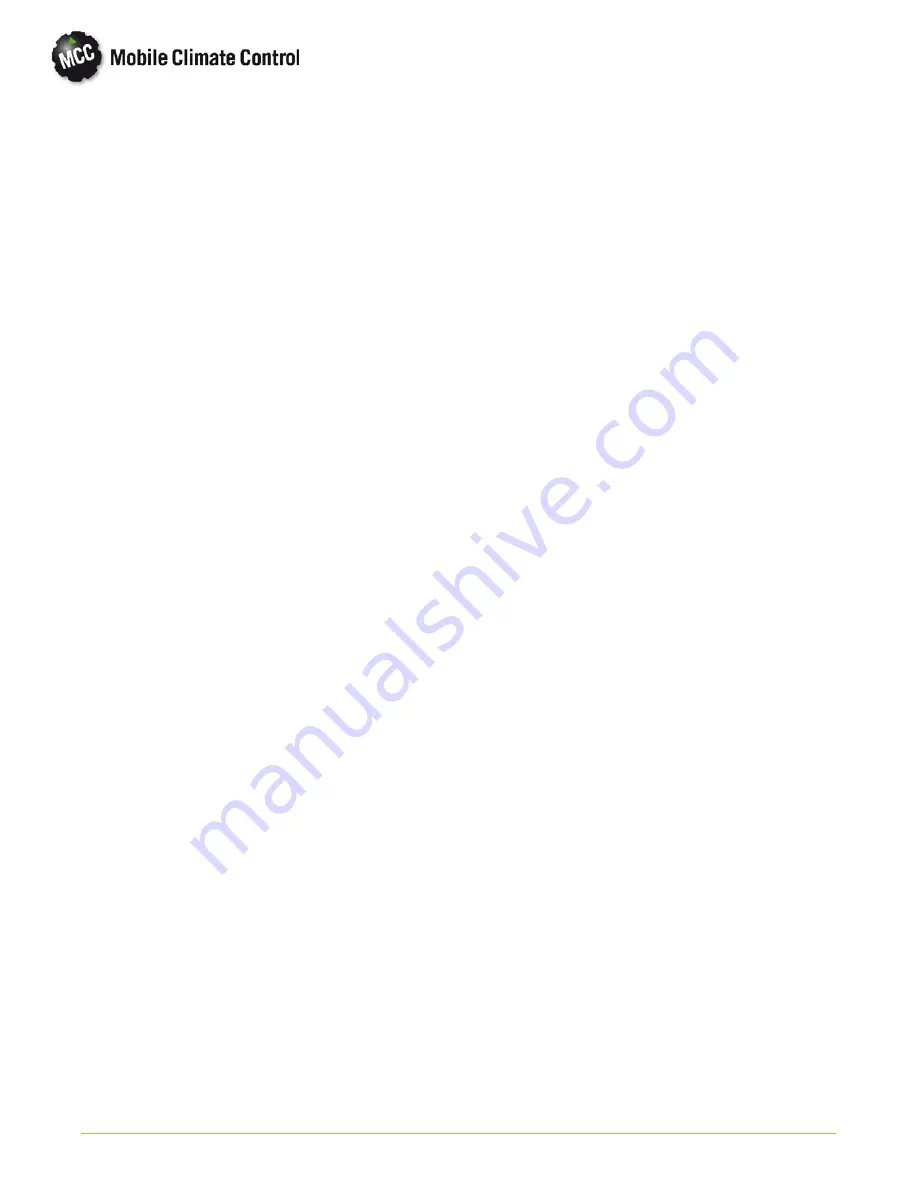
4-13
©
2012 Mobile Climate Control
T-348 Rev. 07/2012
d. Connect an accurate low pressure gauge to the low
pressure port (Figure 1-6).
e. Start bus and run on fast idle until unit has stabi
lized, about 20 to 30 minutes.
NOTE
When conducting this test, the suction pres
sure must be at least 6 psig
(0.41 bar)
below
the expansion valve maximum operating
pressure (MOP). Refer to paragraph 1.5 for
MOP.
f. From the temperature/pressure chart (Table 4-4),
determine the saturation temperature corre
sponding to the evaporator outlet pressure.
g. Note the temperature of the suction gas at the ex
pansion valve bulb. Subtract the saturation tem
perature from this temperature. The difference is
the superheat of the suction gas.
h. The superheat may cycle from a low to high read
ing. Monitor the superheat taking readings every
3-5 minutes for a total of 5-6 readings. Calculate
the superheats, add the readings and divide by the
number of readings taken to determine average su
perheat. Refer to paragraph 1.5 for superheat set
ting.
i. If superheat is not within tolerance, replace the
valve.
4.14 REPLACING EVAPORATOR RETURN AIR FILTERS
The evaporator return air filters are located in the
evaporator section next to the evaporator coils.
Access to the filters is accomplished by removing the
evaporator covers.
The filters should be checked for cleanliness
periodically depending on operating conditions. A
dirty filter will restrict air flow over the evaporator
coil which may cause insufficient cooling or heating
and possible frost buildup on the coil. To remove the
filters, do the following.
a. Place main battery disconnect switch in OFF posi
tion and lock.
b. Open the evaporator top cover. Refer to para
graph 4.2.
c. Grasp and lift the filter elements out using care not
to damage the evaporator coil.
d. Reverse procedure to install new filters and close
the covers.
4.15 COMPRESSOR MAINTENANCE
4.15.1 Removing the Compressor
If compressor is inoperative and the unit still has
refrigerant pressure, isolate the compressor and
remove the refrigerant. Refer to paragraph 4.5.2. If
compressor is operative, perform a pump down.
Refer to paragraph 4.5.3.
a. Place main battery disconnect switch in OFF posi
tion and lock.
b. Tag and disconnect wiring to the high pressure and
low pressure switch, unloaders and clutch.
c. Remove tension on drive belts, remove drive belts.
d. Loosen bolts at suction and discharge service valve
flanges and break seal to be sure pressure is re
leased. Remove bolts.
e. Remove four bolts holding compressor to base
f. Attach sling or other device to the compressor and
remove compressor from the coach through the
rear access door.
NOTES
1 Service replacement compressors are
sold without service valves. Valve pads
are installed in their place. The optional
unloaders are not supplied, as the
cylinder heads are shipped with plugs.
Customer should retain the original
unloader valves for use on the
replacement compressor.
2 The piston plug that is removed from the
replacement compressor head must be
installed in the failed compressor if
returning for warranty or core credit.
3 Do
not
interchange
allen-head
capscrews that mount the piston plug
and
unloader,
they
are
not
interchangeable.
4 Check oil level in service replacement
compressor. Refer to paragraphs 1.5 and
4.15.4.