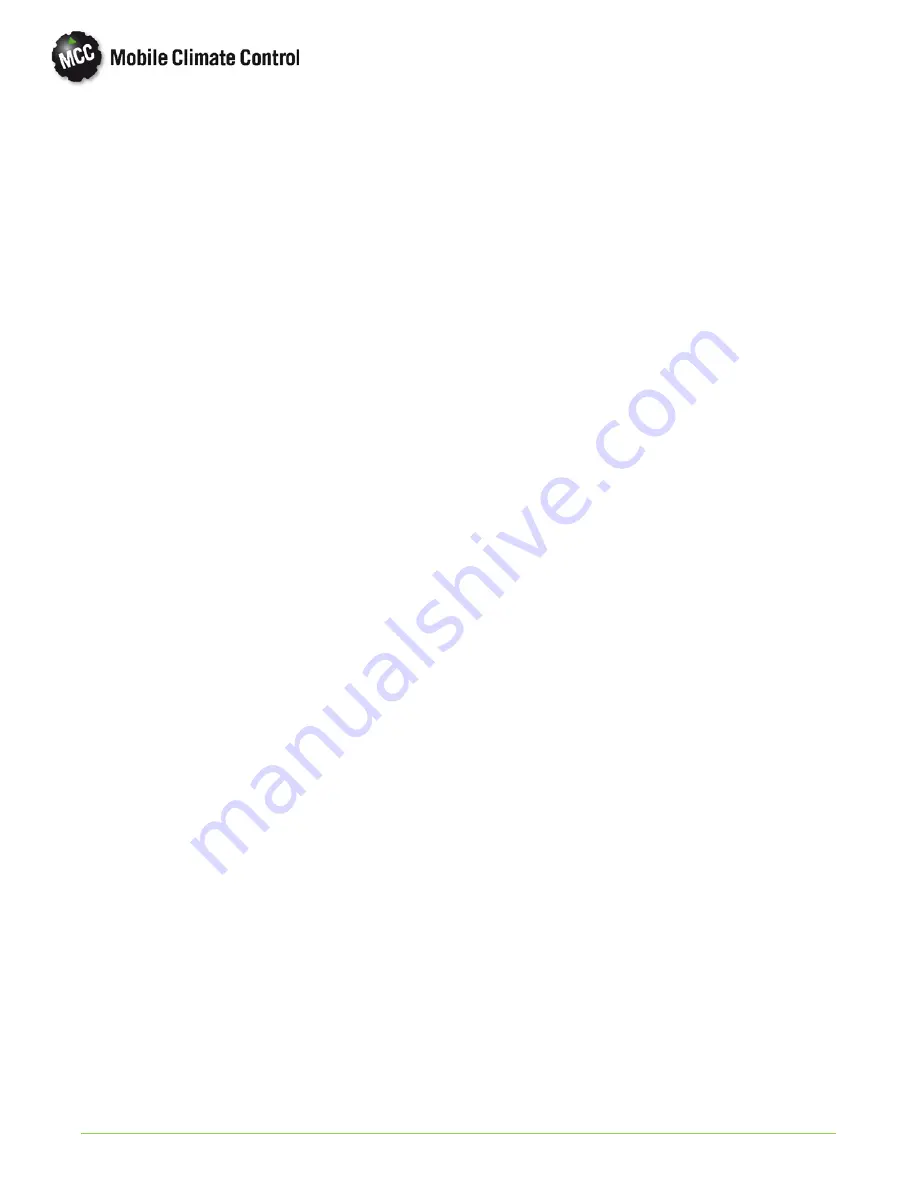
4-7
©
2012 Mobile Climate Control
T-348 Rev. 07/2012
4.5.3 Pump Down An Operable Compressor For Repair
To service an operable compressor, pump the
refrigerant into the condenser coil and receiver as
follows:
a. Install manifold gauge set. Refer to Figure 4-6.
b. Frontseat the compressor suction service valve (6)
by turning clockwise.
c. Install a jumper on the compressor mounted low
pressure switch. Start the unit and run in cooling
until 10 ”/hg (25.4 cm/hg) of vacuum is reached.
Shut the system down and tag out system power
source.
d. Frontseat the compressor discharge service valve
(1) and wait 5 minutes to verify that vacuum is
maintained. If the pressure rises above vacuum,
open the compressor discharge service valve and
repeat steps c and d until a vacuum is maintained.
e. Service or replace components as required and
leak check the compressor.
NOTE
To avoid the entrance of air, never evacuate
an open drive compressor below 500 mi
crons.
f. Using refrigerant hoses designed for vacuum ser
vice, connect a vacuum pump to the center con
nection of the manifold gauge set. Evacuate com
pressor to 500 microns. Close off pump valve (23),
isolate vacuum gauge valve (22) and stop pump.
Wait 5 minutes to verify that vacuum holds.
g. Once vacuum is maintained, re-connect low pres
sure switch. Backseat compressor service valves
and disconnect manifold gauge set.
h. Check refrigerant level. Refer to paragraph 4.8.1. It
may be necessary to clear any alarms that have
been generated.
4.5.4. Removing Entire System Charge
To remove the entire refrigerant charge, do the
following:
a. Connect a manifold gauge set to the system as
shown in Figure 4-6.
b. Connect a reclaimer to the center manifold gauge
set connection.
c. Energize the Liquid Line Solenoid Valve (LSV)
(13) using an external power source (24 VDC).
d. Recover refrigerant in accordance with reclaimer
manufacturers instructions.
4.6 REFRIGERANT LEAK CHECK
A refrigerant leak check should always be performed
after the system has been opened to replace or repair
a component. To check for leaks in the refrigeration
system, perform the following procedure:
NOTE
It is emphasized that only the correct refrig
erant should be used to pressurize the sys
tem. Use of any other refrigerant will con
taminate the system, and require additional
evacuation.
a. Ensure the service valves are open and power the
liquid line solenoid valve from an external source.
b. If system is without refrigerant, charge system
with refrigerant vapor to build up pressure to
approximately 30 PSIG (R-134a).
c. Add sufficient nitrogen to raise system pressure to
150 to 200 psig (10.21 to 13.61 bar).
d. Check for leaks. The recommended procedure for
finding leaks in a system is with an electronic leak
detector. Testing joints with soap suds is satisfac
tory and may be necessary under conditions when
an electronic leak detector will not function cor
rectly.
e. Remove test gas and replace filter-drier.
f. Evacuate and dehydrate the system. Refer to para
graph 4.7.
g. Charge the unit. Refer to paragraph 4.8.
h. Ensure that a Logic Board self-test has been per
formed and that there are no errors or alarms indi
cated. (Refer to paragraph 2.1.3.)