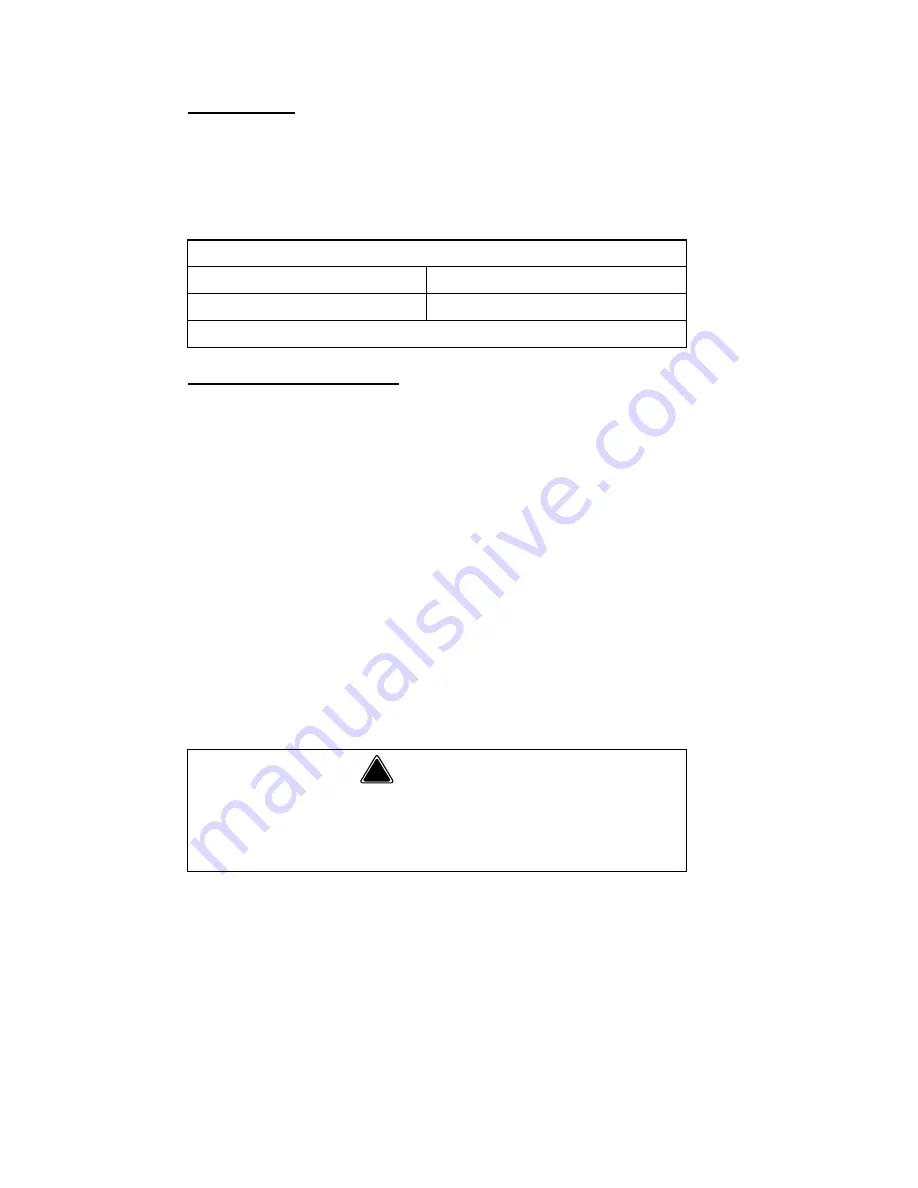
216
Part Number 80-1505-3 6/11
HIGH PRESSURE CUTOUT (HPCO) CONTROL
FUNCTION
Stops the ice machine if subjected to excessive high-
side pressure.
The HPCO control is normally closed, and opens on a
rise in discharge pressure.
CHECK PROCEDURE
1. Set ICE/OFF/CLEAN switch to OFF.
2. Disconnect power to condensing unit.
3. Connect manifold gauges on condensing unit
access valves.
4. Hook voltmeter in parallel across the HPCO,
leaving wires attached.
5. Reconnect condensing unit.
6. Set ICE/OFF/CLEAN switch to ICE, block
condensing unit with cardboard or similar object.
7. No air flowing through the condenser will cause
the HPCO control to open because of excessive
pressure. Watch the pressure gauge and record
the cut-out pressure.
Replace the HPCO control if it:
1. Will not reset (below 300 psig).
2. Does not open at the specified cut-out point.
Specifications
Cut-Out
Cut-In
450 psig ±10
Automatic Reset
(Must be below 300 psig to reset)
!
Warning
If discharge pressure exceeds 460 psig and the
HPCO control does not cut out, set ICE/OFF/CLEAN
switch to OFF to stop ice machine operation.
Содержание SD0672C
Страница 2: ......
Страница 65: ...Part Number 80 1505 3 6 11 65 This Page Intentionally Left Blank ...
Страница 66: ...66 Part Number 80 1505 3 6 11 This Page Intentionally Left Blank ...
Страница 79: ...Part Number 80 1505 3 6 11 79 A B C D ...
Страница 81: ...Part Number 80 1505 3 6 11 81 A B C D E I ...
Страница 90: ...90 Part Number 80 1505 3 6 11 A B C D E F G ...
Страница 94: ...94 Part Number 80 1505 3 6 11 A B C E F D G H ...
Страница 97: ...Part Number 80 1505 3 6 11 97 A B C D F G E ...
Страница 100: ...100 Part Number 80 1505 3 6 11 A B C D E F G H ...
Страница 174: ...174 Part Number 80 1505 3 6 11 This Page Intentionally Left Blank ...
Страница 198: ...198 Part Number 80 1505 3 6 11 This Page Intentionally Left Blank ...
Страница 229: ...Part Number 80 1505 3 6 11 229 SV1406 USING PINCH OFF TOOL ...
Страница 232: ...232 Part Number 80 1505 3 6 11 ...
Страница 238: ...238 Part Number 80 1505 3 6 11 This Page Intentionally Left Blank ...
Страница 276: ...276 Part Number 80 1505 3 6 11 S3070C 230V 50HZ 1PH ...
Страница 283: ...Part Number 80 1505 3 6 11 283 CVD3085 380V 50HZ 3PH ...
Страница 296: ...296 Part Number 80 1505 3 6 11 This Page Intentionally Left Blank ...
Страница 297: ......