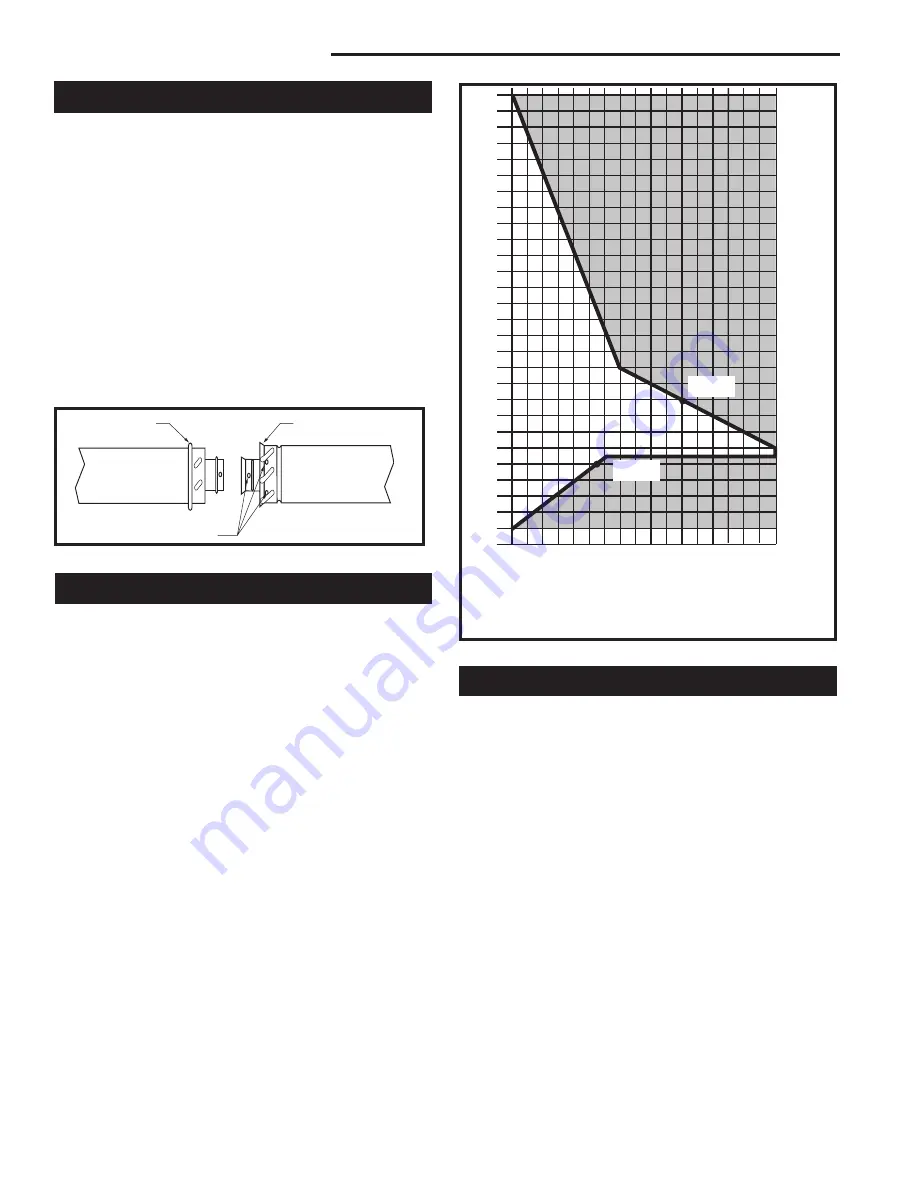
14
LDVR Series Direct Vent Gas Fireplace
10007317
The vent chart should be read in conjunction with the
following vent installation instructions to determine the
relationship of the vertical and horizontal dimensions of
the vent system.
1. Determine the height of the center of the horizontal vent
pipe exiting through the outer wall. Using this dimension
on the Sidewall Vent Graph (Fig. 15) locate the point
intersecting with slanted graph line.
. From the point of this intersection, draw a vertical line
to the bottom of the graph.
3. Select the indicated dimension, and position the fireplace
in accordance with same.
Example A:
If the vertical dimension from the floor of the
fireplace is 11’ (3.4 m) the horizontal run to the face
of the outer wall must not exceed 14’ (4.3 m).
Example B:
If the vertical dimension from the floor of the unit is
7’ (.14 m), the horizontal run to the face of the outer
wall must not exceed 8
¹⁄₂
’ (.6 m).
How to Use the Vent Graph
Rear Wall Venting Applications
When installed as a rear vent unit this appliance may be
vented directly to a termination located on the rear wall
behind the appliance.
•
Only Vermont Castings Group venting components
Vermont Castings Group venting components
venting components
are approved to be used in these applications. (Refer
to “Venting Components” listed for different installation
requirements)
•
The maximum horizontal distance between the rear of
the appliance (or end of the transition elbow in a corner
application) and the outside face of the rear wall is 0”
(508mm). (Fig. 16)
•
Only one 45° elbow is allowed in these installations.
•
Minimum clearances between vent pipe and combus-
tible materials are as follows:
Top - ” (51 mm)
Sides - 1” (5 mm)
Bottom - 1” (5 mm)
Horizontal dimension from the outside face of the
wall to the center of the fireplace vent flange
Sidewall vent graph showing the relationship between vertical and
horizontal dimensions for a Direct Vent flue system.
Vertical dimension from the floor of the unit
to the center of the horizontal vent pipe
3
4
5
6
7
8
9
10
11
12
13
14
15
16
17
18
19
20
21
22
23
24
25
26
27
28
29
30
3 4 5 6 7 8 9 10 11 12 13 14 15 16 17 18 19 20
eg: A
eg: B
CFM102
DV Graphic
9/28/00 sta
Fig. 15
Sidewall venting graph. (Dimensions in feet)
TWL100
Twist Lock Pipe
3/12/99 djt
Male End
Female End
Screw Holes
TWL100
Fig. 14
Twist-lock pipe joints.
Twist Lock Pipes
When using Vermont Castings Group twist-lock pipe it is
Vermont Castings Group twist-lock pipe it is
twist-lock pipe it is
not necessary to use sealant on the joints. The only areas
of the venting system that need to be sealed with high
temperature silicone sealant are the sliding joints of any
telescopic vent section used in the system.
To join the twist lock pipes together, simply align the beads
of the male end with the grooves of the female end, then
while bringing the pipe together, twist the pipe until the
flange on the female end contacts the external flange
on the male end. It is recommended that you secure the
joints with three (3) sheet metal screws, however this is
not mandatory with twist lock pipe.
To make it easier to assemble the joints we suggest putting
a lubricant (Vaseline or similar) on the male end of the twist
lock pipe prior to assembly.