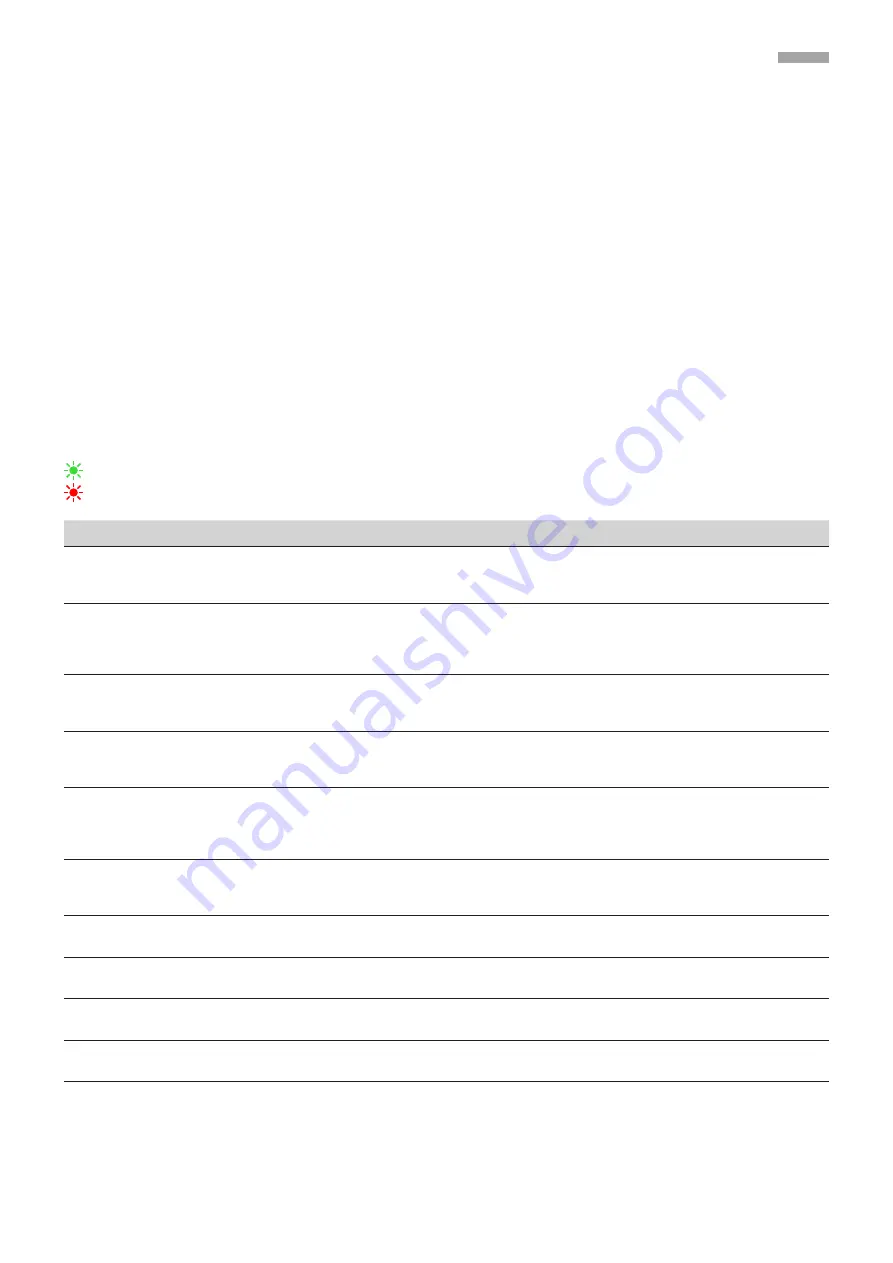
23
SERVICE
Service
F / P Functions enable / disable
With the YM 3N1 FP it is possible to switch the sensing heads F and P function on / off.
After changing, it is necessary to carry out a warm start. Settings: Service / Service Parameters / Other
F and P is only available with the corresponding sensor and the additional PCB (Art. No. 701000.000) on the SE.
Hardware Locks
LOEPFE YM 3N1 has a built-in diagnostic function. Technical problems are indicated by means of hardware locks.
Hardware locks can be cancelled by means of the unlock card, from the SCU or with button on sensing head. Since hardware
failures of this kind can have several influences on yarn quality, they should be corrected and reset by qualified personnel only.
Hardware locks should therefore be assigned to unlock card 3, which should be accessible to qualified personnel only.
A hardware alarm is indicated on the Q-sensor: Both LEDs are flashing. The type of alarm can be viewed on the SCU screen.
Fault
Description
Possible cause
Recommended action
Hardware QB lock 0
Unspecified diagnostic lock af-
ter restart of SE
A lock was present before Power
Down of the SE and is restored by
the SCU
Correct lock situations before Power
Down of SE
Reset lock and check again
Hardware QB lock 1 (*)
The SH detects no Yarn signal
although the rotor is in RUN
state
Yarn not / not correctly in the SH
measuring slit
SH lower ceramic missing
SH defective
Check Yarn position and guiding
Replace SH
Hardware QB lock 2
Measured Yarn signal is too low
Yarn position wrong
SH lower ceramic missing
SH defective
Check Yarn position and guiding
Replace SH
Hardware QB lock 3
Measured Yarn signal is too
high
Measuring slit obstructed by dust
or lint
SH defective
Remove dust or lint
Replace SH
Hardware QB lock 4
Too much Run / Stop transitions
in the measured Yarn signal
Maximum piecing attempts reached
(default 20 per shift)
Yarn position wrong
SH defective
Check piecing robot and spinbox
components
Check and correct
Replace SH
Hardware QB lock 5
No communication with YM
3N1 SH
Cable unplugged or defective
SH defective
SE has a defective input
Connect or replace cable
Replace SH
Replace SE
Hardware QB lock 6
Minimum intensity signal. (F
channel)
SH has no F-function
SH defective
Install correct SH
Replace SH
Hardware QB lock 7
Maximum intensity signal. (F
channel)
Machine is producing blended yarn
SH defective
Disable F-channel of YM 3N1
Replace SH
Hardware QB lock 8
Minimum intensity signal. (P
channel)
SH has no P-function
SH defective
Install correct SH
Replace SH
Hardware QB lock 9
Maximum intensity signal. (P
channel)
Machine is producing synthetic yarn
SH defective
Disable P-channel of YM 3N1
Replace SH
Notes:
(*) = Function not present on stand-alone installations
SH = Sensing Head
SE = Section Electronics
SCU = Sensors Central Unit
YM 3N1 = YarnMaster 3N1
Содержание Savio FRS 3000
Страница 1: ...YARNMASTER 3N1 46359003en Fitting Instruction Savio FRS 3000...
Страница 2: ......
Страница 4: ...4 3N1 INHALTSVERZEICHNIS...
Страница 6: ......