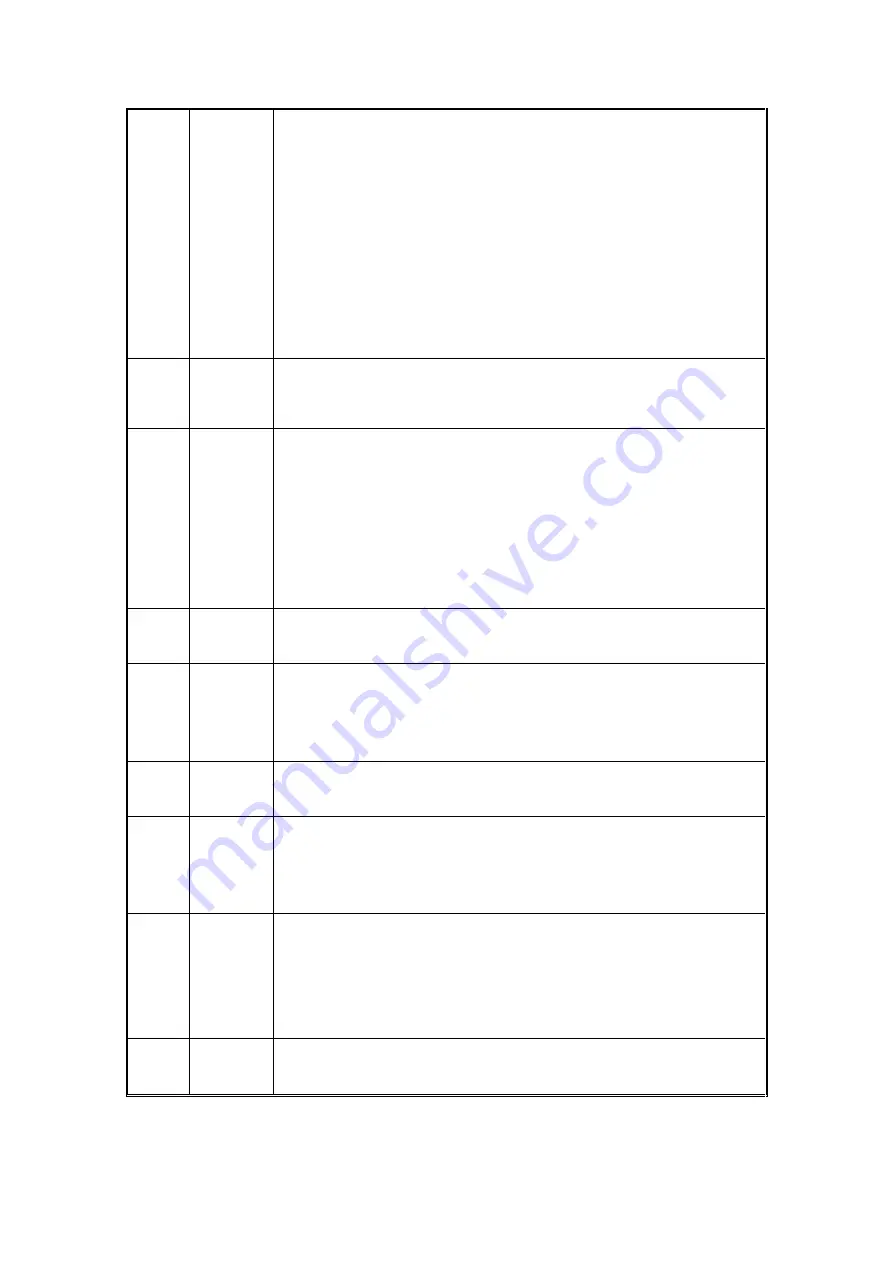
42
13-14
Room
Thermostat or
Open-Therm
Bus Controller
When no time or temperature control is required, these terminals should be linked. In this situation, the boiler
flow temperature is set via the control interface; if an outside temperature sensor is connected, the boiler is
controlled through the heating curve.
When an On/Off room thermostat (with or without timer) or a BMS enable contact is connected, the boiler will
operate when the controller contact is closed. The flow temperature is controlled set via the control interface
(with or without outside temperature compensation). To prevent interference in the control circuit, cabling to
any control switch should be kept away from sources of electromagnetic interference or suitable screened
cable should be used.
When configured (see
Section 13.1 SETTING THE PARAMETERS WITH THE DISPLAY MENU
for further
information), terminals ‘7’ and ‘8’ can be used to switch the unit between normal and setback operation mode.
When an “Open-Therm” room thermostat is connected, it should be connected to terminals ‘7’ and ‘8’
using
screened cable
. The boiler is ready for use with a multifunctional room controller (such as the Lochinvar RC
Controller). For further information, please see the controller specific manual.
No change in control parameters will be required when this connection is used.
15-16
0 – 10V DC
The boiler setpoint can or firing rate can be adjusted by an external control, through a 0V to 10V analogue
signal. For Further information on 0-10 VDC control, please refer to
Section 13.1: SETTING THE
PARAMETERS WITH THE DISPLAY MENU
.
The “+” has to be connected to terminal ‘15’, while the “-“ has to be connected to the terminal ‘16’.
17-18
Cascade
Connection
The Lochinvar CP-M+ has a built in cascade management system. When two or more boilers are connected
in a cascade, each boiler of the cascade has to be connected to the next boiler using terminals ‘17’ and ‘18’.
This connection is polarity sensitive (all terminal 17s to be linked and all terminal 18s to be linked) and should
be made using screened cable.
One boiler has to be appointed as a Master, while the other boiler(s) are the Slaves. All external controls
such as calorifier sensor, outside temperature sensor, system pumps etc. are to be connected to the Master
boiler.
For a cascade to work correctly, it is essential that a flow temperature sensor is used.
Each connected boiler needs to be programmed with a different address through the control interface, see
Section 13.1: SETTING THE PARAMETERS WITH THE DISPLAY MENU
for further details.
19-20
Lock-Out
Signal
Terminals ‘19’, and ‘20’ are normally open volt free terminals that can be used to give status signals to a BMS
panel in the event of a ‘Lock-Out ’condition.
No change in control parameters will be required when these connections are used.
21-22
Burner Burning
Signal
Terminals ‘21’, and ‘22’ are normally open volt free terminals that can be used to give status signals to a BMS
panel when the burner is operational.
The contacts can also be configured to close when a specific firing rate is reached to enable a non-cascaded
boiler.
A change in control parameters is required to activate this function.
23-24
Burner
Demand
Signal
Terminals ‘23’ and ‘24’ are normally open volt free terminals that can be used to give status signals to a BMS
panel when a demand for heat is present.
A change in control parameters is required to activate this function.
25-26-
27
Central
Heating
System Pump
If required, a central heating system pump can be connected to terminals ’25 – 27’.
When a calorifier is connected to the boiler (or to the Master, when a cascade system is installed), the system
pump is switched off when there is a DHW demand.
If the pump has an electrical loading in excess of 250 watts, a relay should be used to energise the
pump.
28-29-
30-31
Calorifier
Diverter Valve
or Calorifier
Pump
Where a diverter valve is used to separate the CH circuit from the DHW circuit, this can be controlled by the
boiler using terminals ’28 – 31’. Where the DHW circuit is operated by an additional pump, this can be
enabled using terminals ’29 – 31’
See
Section 13.1: SETTING THE PARAMETERS WITH THE DISPLAY MENU
for details on configuring this
output.
If the pump has an electrical loading in excess of 250 watts, a relay should be used to energise the
pump.
32-33-34
230 V ~ 1 Ph
50 Hz Supply
The 230 VAC 1PH 50Hz power supply should be connected to terminals ’24 – 26’.
Terminal ‘32’ should be Live
Terminal ‘33’ should be Earth
Terminal ‘34’ should be Neutral.
TABLE 11.2
CONNECTION TERMINAL DETAILS
Содержание CP-M Series
Страница 5: ...5 2 0 PRINCIPAL PARTS FIGURE 2 1 REMOVABLE COMPONENTS CP M 60...
Страница 6: ...6 FIGURE 2 2 REMOVABLE COMPONENTS CP M 60 CONTINUED...
Страница 8: ...8 FIGURE 2 3 REMOVABLE COMPONENTS CP M 80 CP M 100...
Страница 9: ...9 FIGURE 2 4 REMOVABLE COMPONENTS CP M 80 CP M 100 CONTINUED...
Страница 11: ...11 FIGURE 2 5 REMOVABLE COMPONENTS CP M 120...
Страница 12: ...12 FIGURE 2 6 REMOVABLE COMPONENTS CP M 120 CONTINUED...
Страница 14: ...14 FIGURE 2 7 REMOVABLE COMPONENTS CP M 150 CP M 180...
Страница 15: ...15 FIGURE 2 8 REMOVABLE COMPONENTS CP M 150 CP M 180 CONTINUED...
Страница 94: ...94...