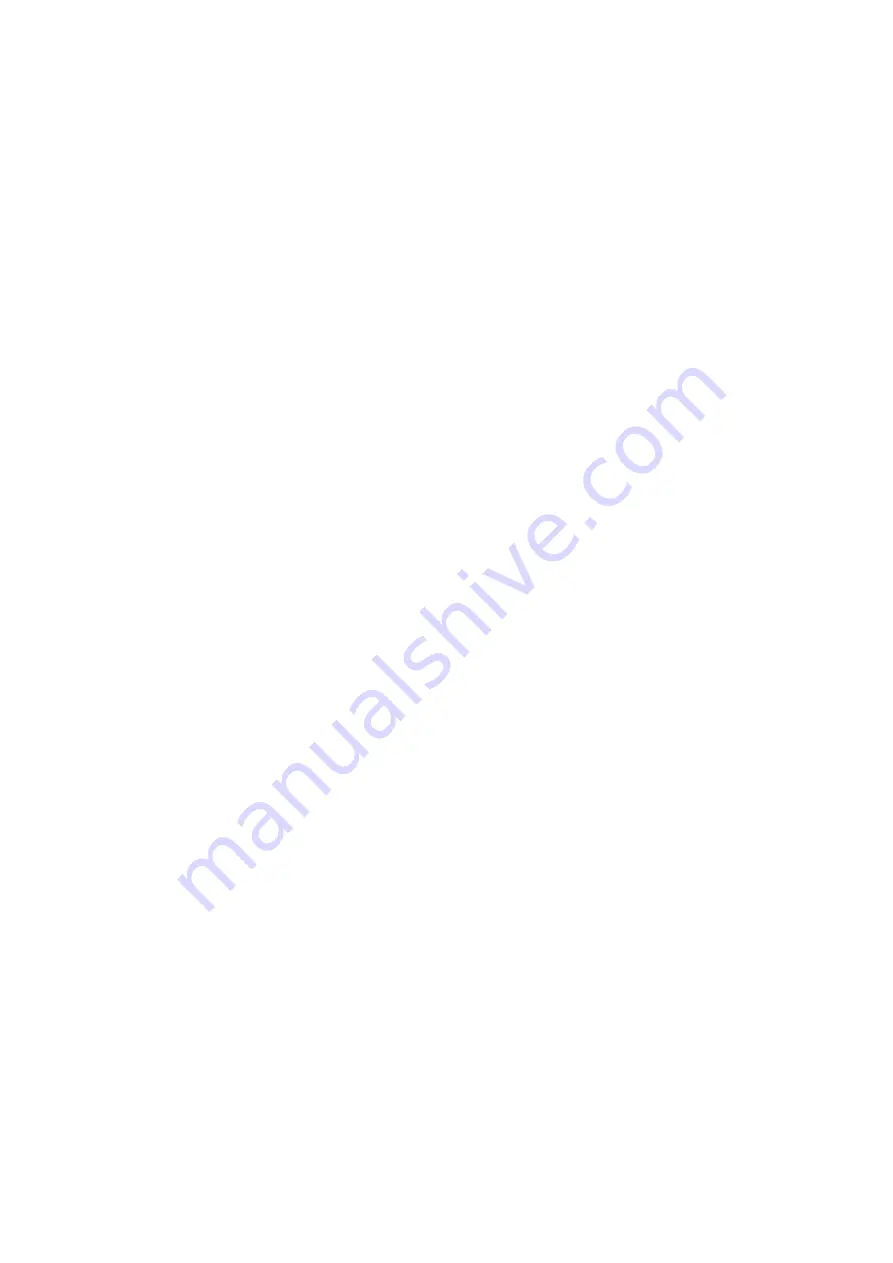
72
14.0
COMMISSIONING AND TESTING
14.1
ELECTRICAL INSTALLATION
Notes on the requirements for electrical installation are provided in
Section 11:
ELECTRICAL SUPPLY
. A
schematic drawing of the control circuit is shown in
Figure 11.2
14.2
GAS INSTALLATION
For design see
Section 7: GAS SUPPLY.
See
Figure 3.1
or
Figure 3.2
for details on the position of the gas
connection.
14.3
WATER CONNECTIONS
For design see
Section 10: WATER CONNECTIONS
The system should be thoroughly flushed in accordance with CIBSE Commissioning Codes B & W and
BSRIA AG1/2001.1: Pre-commission cleaning of pipework systems.
Check the system for leaks and repair as necessary. If the system is configured in a sealed arrangement, check
the expansion vessel cushion pressure and pressurisation unit settings.
14.4
COMMISSIONING THE EQUIPMENT
14.4.1
GENERAL CHECKS PRIOR TO LIGHTING
A person deemed competent MUST be responsible for the commissioning of this equipment. Before
attempting to commission any equipment, ensure that personnel involved are aware of what action is
about to be taken and begin by making the following checks:
1.
Flueway passages are clear.
2.
Adequate ventilation exists in the plant room (if necessary)
3.
The system is fully charged with water, ready to receive heat. All necessary valves are open and all
allied pumps are circulating water.
4.
The gas supply pipework is clear of any loose matter, tested for soundness and purged.
5.
The condensate drain is installed correctly and the condensate trap is filled with water. (see
Section 6.6:
FILLING THE CONDENSATE TRAP
)
NOTE: If the condensate trap is not filled with water before use, products of combustion may escape
and may cause severe personal injury or death.
14.4.2
EQUIPMENT CHECKS PRIOR TO LIGHTING
This unit has been designed for a nominal gas inlet pressure of 20 mbar when used on natural gas.
Information relating to propane firing can be found in Section 15: LPG FUEL
1.
Gas supply is connected but turned to the “off” position. Any unions or fittings are correctly tightened,
test points are closed and the ignition electrode lead is connected correctly. Ensure the ceramic sheath
around the ignition electrode is not cracked or broken.
2.
Ensure electricity supply is connected.
3.
Check that the heat exchanger is fully bled by opening the bleed automatic air vent screw cap.
Содержание CP-M Series
Страница 5: ...5 2 0 PRINCIPAL PARTS FIGURE 2 1 REMOVABLE COMPONENTS CP M 60...
Страница 6: ...6 FIGURE 2 2 REMOVABLE COMPONENTS CP M 60 CONTINUED...
Страница 8: ...8 FIGURE 2 3 REMOVABLE COMPONENTS CP M 80 CP M 100...
Страница 9: ...9 FIGURE 2 4 REMOVABLE COMPONENTS CP M 80 CP M 100 CONTINUED...
Страница 11: ...11 FIGURE 2 5 REMOVABLE COMPONENTS CP M 120...
Страница 12: ...12 FIGURE 2 6 REMOVABLE COMPONENTS CP M 120 CONTINUED...
Страница 14: ...14 FIGURE 2 7 REMOVABLE COMPONENTS CP M 150 CP M 180...
Страница 15: ...15 FIGURE 2 8 REMOVABLE COMPONENTS CP M 150 CP M 180 CONTINUED...
Страница 94: ...94...