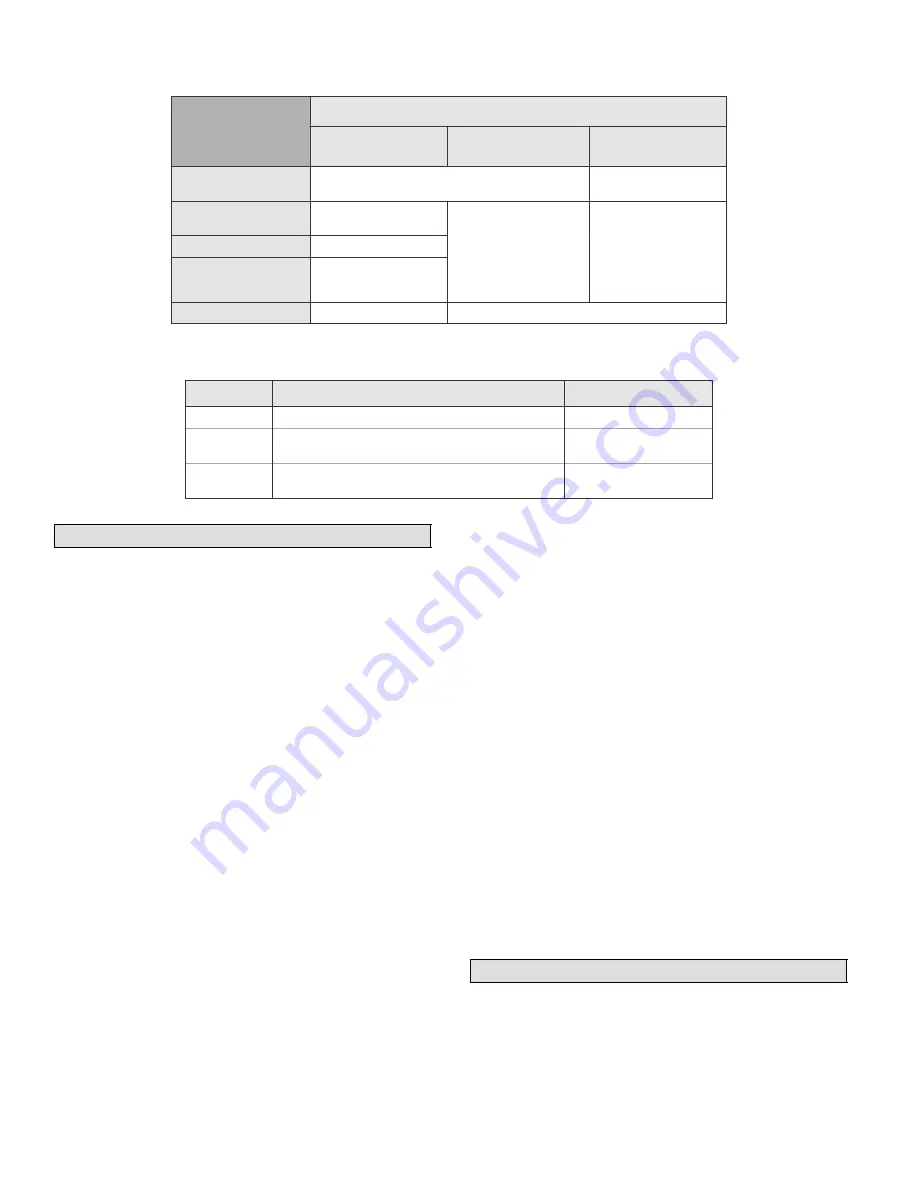
Page 22
If the burner is in the
below state:
Pushing the reset button will:
Button Click
(press < 1 second)
Button Hold
(press > 1 second)
Button Hold
(press 15+ seconds)
t
u
o
k
c
o
L
tf
o
S
m
o
r
f
t
e
s
e
R
t
u
o
k
c
o
L
Reset from Restricted
(Hard) Lockout
Valve−on Delay, Trial for
Ignition, Ignition Carryover
Go to pump prime (see
Priming the Pump" above)
Disable the Burner:
Any time the burner is
running, press and hold
the reset button to disable
the burner. The burner will
remain off as long as the
button is held.
Enables pump priming
After the reset button has
been held for 15 seconds.
The button can then be
clicked during the next
ignition sequence to enter
pump prime mode.
Run (igniter is shut off)
No action
No action
Pump Prime
No action
Exit Pump Prime mode and return to Standby
g
n
i
h
s
a
l
F
y
l
s
u
o
u
n
i
t
n
o
C
n
O
r
o
l
o
C
t
h
g
i
L
t
u
o
k
c
o
L
tf
o
S
t
u
o
k
c
o
L
)
d
r
a
H
(
d
e
t
c
ir
t
s
e
R
d
e
R
Green
Flame Sensed during normal operation (Could be stray
light during standby)
Recycle
Yellow
Control is in pump prime mode
or
N/A
Table 10
Reset Button Operation
Table 11
Status Light Function
Reset button currently held for 15+ seconds.
Heating Sequence − Actions & Responses
1.
Action: Thermostat calls for heat
(W terminal is en-
ergized)
Response:
D
ST9103A control (A15) closes oil primary control
TR−TW contacts.
D
After 15−second prepurge, power is sent to the oil
delay valve, ignition occurs and flame is
established.
D
Igition sequence continues for 10 seconds after
flame is sensed. Oil will continue to flow as long as
cad cell senses flame.
D
Heat fan on ramp timing begins. When timing is
complete, the indoor blower is at heat speed and
warm air is delivered to the controlled space.
2.
Action: Thermostat ends call for heat
(W terminal
is de−energized)
Response:
D
After the thermostat is satisfied, the thermostat
circuit opens. The oil delay valve and burner are
de−energized.
D
Burner is de−energized.
D
Heat fan off ramp timing begins. When timing is
complete, indoor blower is de−energized.
D
Blower control returns to standby mode (oil prima-
ry control and indoor blower are off).
3.
Action: Burner fails to light
Response:
D
Oil primary control enters soft lockout after ignition
failure (15 seconds without flame being sensed).
Push reset button on primary control for one sec-
ond to reset soft lockout.
D
After soft lockout reset, oil primary control allows
second ignition attempt. Primary control enters
hard lockout after second ignition failure (15 sec-
onds without flame being sensed). Push reset but-
ton on primary control for 15 seconds until light on
control turns yellow to reset hard lockout.
D
Burner motor is de−energized.
4.
Action: Established flame fails
Response:
D
Burner motor is de−energized and oil primary con-
trol goes into recycle mode.
D
If the fan off delay is longer than the recycle timing,
the indoor blower continues to run on heating
speed through the next trial for ignition.
5.
Action: Limit Switch Opens
Response:
D
Oil primary control de−energizes burner.
D
Indoor blower is energized immediately at cool
speed.
D
A15 control opens oil primary control TR−TW con-
tacts.
D
Indoor blower runs as long as limit stays open.
6.
Action: Limit Switch Closes
Response: If there is a heating demand, A15 control
energizes oil primary control and ignition sequence
begins.
Troubleshooting
Burner failure or improper operation can result from a num-
ber of different causes. Often the cause can be pinpointed
by observing the different types of failure or by the process
of elimination. The following troubleshooting charts list
some failures, causes and a sequence of steps to isolate
the point of failure. Check the simplest and most obvious
items before progressing to other items.