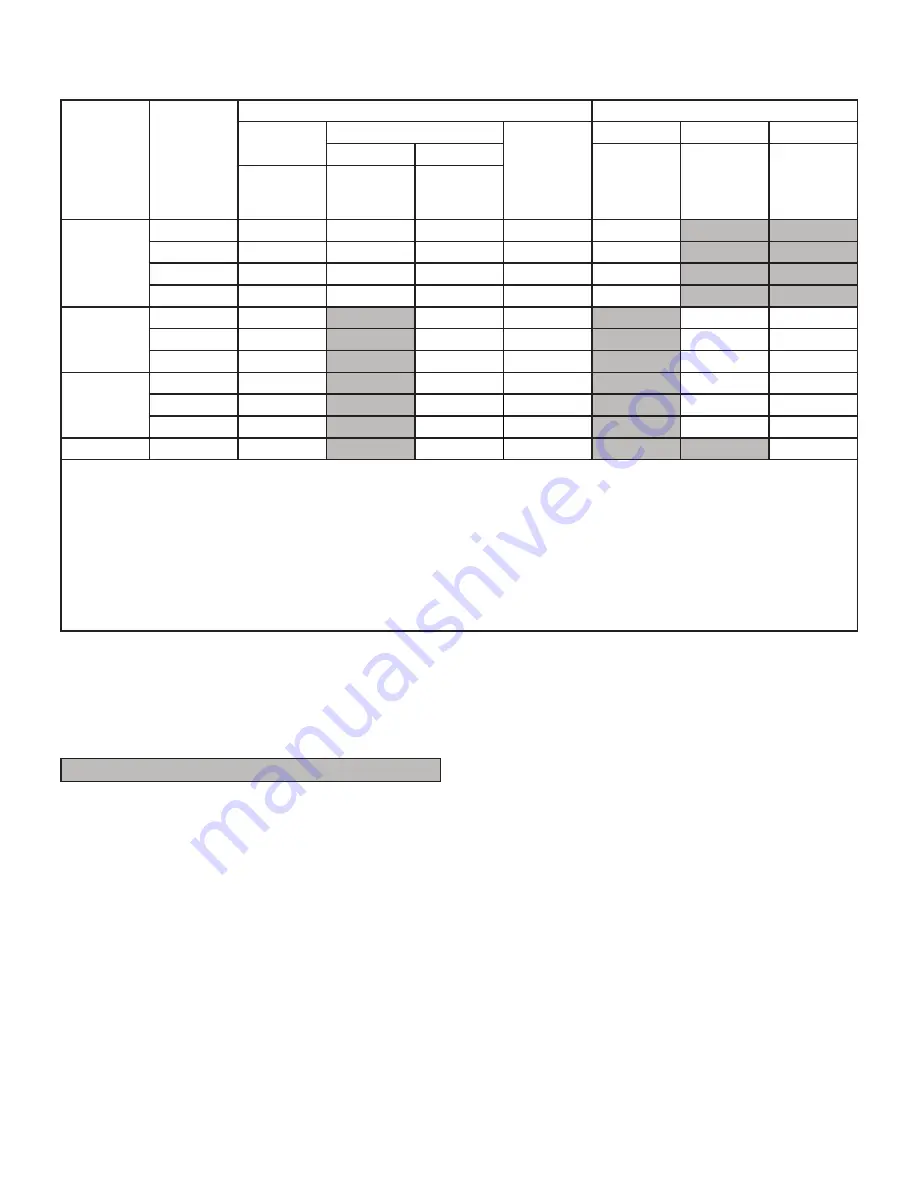
Page 47
TABLE 22
OUTDOOR TERMINATION USAGE*
Input Size
Vent Pipe
Dia. in.
STANDARD
CONCENTRIC
Flush Mount
Kit
Wall Kit
Field
Fabricated
1-1.2 inch
2 inch
3 inch
2 inch
3 inch
71M80 (US)
4
44W92
(CA)
69M29 (US)
4
44W92
(CA)
60L46 (US)
4
44W93
(CA)
51W11 (US)
51W12
(CA)
22G44 (US)
4
30G28 (CA)
44J40 (US)
4
81J20 (CA)
070
6
1-1/2
3
YES
YES
1
YES
5
YES
2
YES
2
3
YES
YES
1
YES
5
YES
2
YES
2-1/2
3
YES
YES
1
YES
5
YES
2
YES
3
3
YES
YES
1
YES
5
YES
2
YES
090
2
3
YES
YES
5
YES
YES
YES
2-1/2
3
YES
YES
5
YES
YES
YES
3
3
YES
YES
5
YES
YES
YES
110
2
YES
YES
5
YES
YES
YES
2-1/2
YES
YES
5
YES
YES
YES
3
YES
YES
5
YES
YES
YES
135
3
YES
YES
5
YES
YES
NOTE - Standard Terminations do not include any vent pipe or elbows external to the structure. Any vent pipe or elbows external to the structure must be included in total
vent length calculations. See vent length tables.
* Kits must be properly installed according to kit instructions.
1Requires field-provided outdoor 1-1/2” exhaust accelerator.
2Concentric kits 71M80 and 44W92 include 1-1/2 in. outdoor accelerator, when used with 070 input models. When 1-1/2 in. pipe is used it must transition to 2 in. pipe with
the concentric kit.
3 Flush mount kits 51W11 and 51W12 includes 1-1/2 in. outdoor exhaust accelerator, required when used with 070 and 090 input models. When 1-1/2 in. pipe is used it
must transition to 2 in. pipe with the flush mount kit.
4 Termination kits 30G28, 44W92, 4493 and 81J20 are certified to ULC S636 for use in Canada only.
5 See table 26 for vent accelerator requirements.
6 2 in. to 1-1/2 in.
field provided
reducer required.
Canadian Applications Only -
Pipe, fittings, primer and
solvent cement used to vent (exhaust) this appliance must
be certified to ULC S636 and supplied by a single manu
-
facturer as part of an approved vent (exhaust) system. In
addition, the first three feet of vent pipe from the furnace
flue collar must be accessible for inspection. TABLE 22
lists the available exhaust termination kits.
Joint Cementing Procedure
All cementing of joints should be done according to the
specifications outlined in ASTM D 2855.
NOTE -
A sheet metal screw may be used to secure the
intake pipe to the connector, if desired. Use a drill or self
tapping screw to make a pilot hole.
1 - Measure and cut vent pipe to desired length.
2 - Debur and chamfer end of pipe, removing any
ridges or rough edges. If end is not chamfered,
edge of pipe may remove cement from fitting socket
and result in a leaking joint.
NOTE -
Check the inside of vent pipe thoroughly for
any obstruction that may alter furnace operation.
3 - Clean and dry surfaces to be joined.
4 -
Test fit joint and mark depth of fitting on outside of
pipe.
5 - Uniformly apply a liberal coat of PVC primer for
PVC or use a clean dry cloth for ABS to clean inside
socket surface of fitting and male end of pipe to
depth of fitting socket.
6 - Promptly apply solvent cement to end of pipe and
inside socket surface of fitting. Cement should be
applied lightly but uniformly to inside of socket. Take
care to keep excess cement out of socket. Apply
second coat to end of pipe.
NOTE -
Time is critical at this stage. Do not allow
primer to dry before applying cement.
7 - Immediately after applying last coat of cement to
pipe, and while both inside socket surface and end
of pipe are wet with cement, forcefully insert end of
pipe into socket until it bottoms out. Turn PVC pipe
1/4 turn during assembly (but not after pipe is fully
inserted) to distribute cement evenly. DO NOT turn
ABS or cellular core pipe.
NOTE -
Assembly should be completed within 20
seconds after last application of cement. Hammer
blows should not be used when inserting pipe.
8 - After assembly, wipe excess cement from pipe at
end of fitting socket. A properly made joint will show
a bead around its entire perimeter. Any gaps may
indicate a defective assembly due to insufficient
solvent.
9 - Handle joints carefully until completely set.