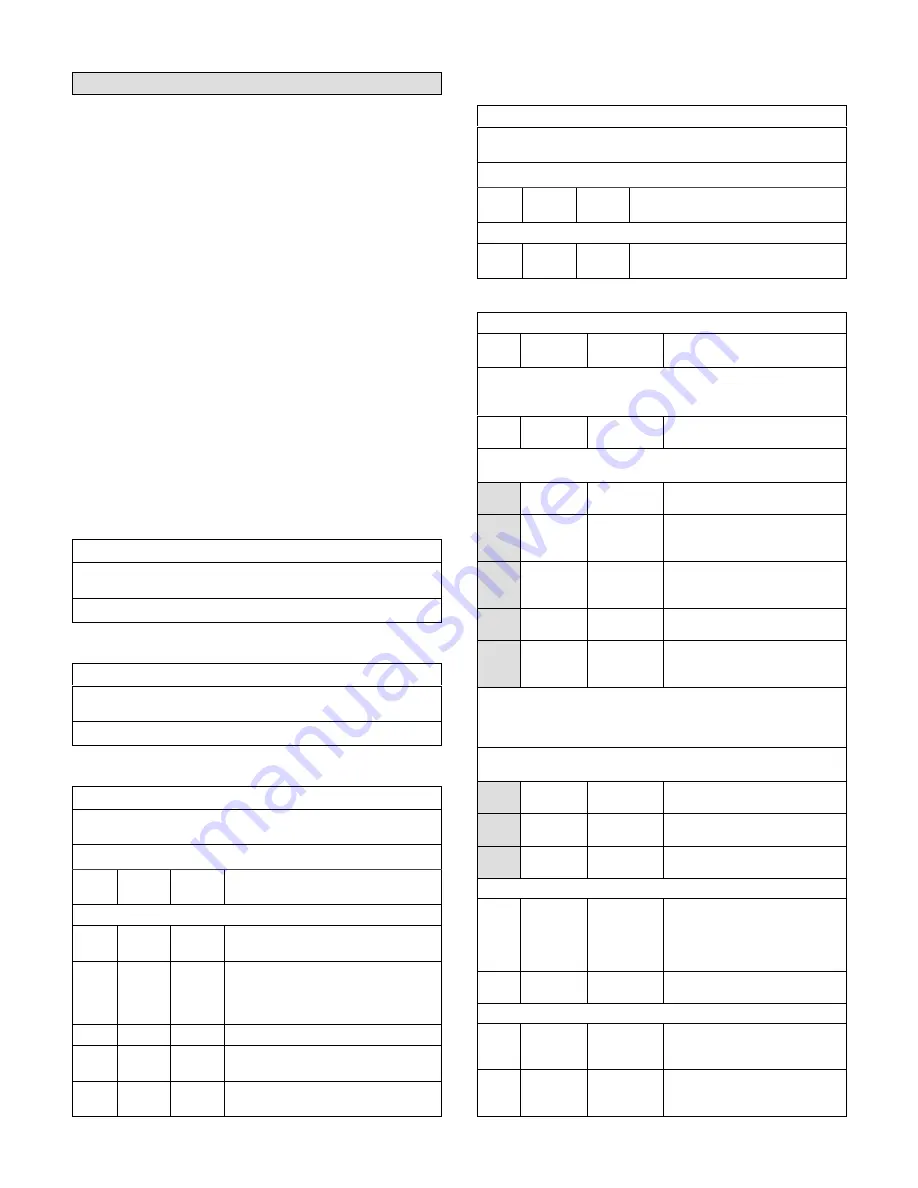
Page 45
Factory Unit Controller Settings
Use the Unit Controller to adjust parameters; menu paths
are shown in each table. Refer to the Unit Controller
manual provided with each unit.
Tables 30 through 40 show factory settings (in degrees, %
of fan CFM, etc.). Record adjusted settings on the label
located inside the compressor access panel.
When field installing optional kits and accessories, the
Unit Controller must be configured to identify the option
before it will function. Refer to figures 37 and 38 to
determine whether the Unit Controller configuration I.D.
must change. To configure the option, use MAIN MENU >
SETUP > INSTALL menu path. Press SAVE until
CONFIGURATION ID 1 or 2 appears depending on the
option installed. Change the appropriate character in the
configuration I.D. For example, when an economizer is
installed using a single enthalpy sensor, change
configuration I.D. 1, the second character, to “S”.
TABLE 30
580730
Units With BACnet Module Settings
Use menu SETUP > NETWORK INTEGRATION. Set “BACNET” and
network address.
BACNET MAC ADDRESS:
TABLE 31
580732
Units With Room Sensor, CPC/LSE Gateway Settings
Use menu SETUP > NETWORK INTEGRATION. Set “L CONNEC
TION” and network address.
LCONN ADDRESS:
TABLE 32
580735
Units with BACnet Module (Target) Settings
Use menu SETUP > NETWORK INTEGRATION. Set “BACNET”
and network address.
BACNET MAC ADDRESS:
Para
meter
Factory
Setting
Setting
Description
Use SETTINGS > RTU OPTIONS > EDIT PARAMETERS
91
120
Sets the compressor minimum run
time to 2 minutes.
106
99
Set reheat SP from connected sensor
to 99% to basically disable. Reheat
will be controlled over by BAS. Only
applies to units with the reheat option.
111
3
Thermostat with three cooling stages.
117
0
DCV max. open damper. 0=controlled
by network.
153
60
Time delay between heating and cool
ing mode.
TABLE 33
580733
Units With BACnet Module (Kohl's) Settings
Use menu SETUP > NETWORK INTEGRATION. Set “BACNET”
and network address.
BACNET MAC ADDRESS:
Para
meter
Factory
Setting
Setting
Description
Use SETTINGS > RTU OPTIONS > EDIT PARAMETERS
137
65
Sets the backup occupied heating set
point to 65F.
TABLE 34
580685
LGH/LCH 152U4E (2-Compressor) Staged Direct Drive
Para
meter
Factory
Setting
Field
Setting
Description
Note: Any changes to Smoke CFM setting must be adjusted
before the other CFM settings. Use SETTINGS > RTU OPTIONS
> EDIT PARAMETERS
12
5000
CFM
CFM
Blower CFM during smoke
detection.
SETUP > TEST & BALANCE (can also use SETTINGS > RTU
OPTIONS > BLOWER > SPEEDS)
5000
CFM
CFM
Blower CFM during heating.
5000
CFM
CFM
Blower CFM during high speed
cooling (2 compressor)
operation.
3250
CFM
CFM
Blower CFM during low speed
cooling (1 compressor)
operation.
5000
CFM
CFM
Blower CFM during ventilation.
1655
RPM
RPM*
Adjust RPM based on unit static
and blower tables to reach tar
get CFM.
*Once all four blower settings are entered, the target (highest of the
heating and cooling settings) CFM will be displayed. Once the RPM
is saved for the target CFM, all other blower RPM values are set by
the Unit Controller according to the field CFM setting..
SETUP > TEST & BALANCE (can also use SETTINGS > RTU
OPTIONS > DAMPER)
0%
%
Damper min. position during
LOW blower operation.
0%
%
Damper min. position during
HIGH blower operation.
50%
%
Min. damper % for stage 1 pow
er exhaust operation.
SETTINGS > RTU OPTIONS > EDIT PARAMETERS
29
101%
%
Open
Damper minimum position during
G blower operation. (Setting para
meter 29 to “101” disables para
meter 29 and passes control to
parameter 9 or 132)
216
5%
%
Deadband % for stage 1 power
exhaust operation.
SETTINGS > RTU OPTIONS > EDIT PARAMETER
85
40°F
°F
Compressor 1 low temp lockout.
Settings lower than 40°F could
void warranty.
86
40°F
°F
Compressor 2 low temp lockout.
Settings lower than 40°F could
void warranty.