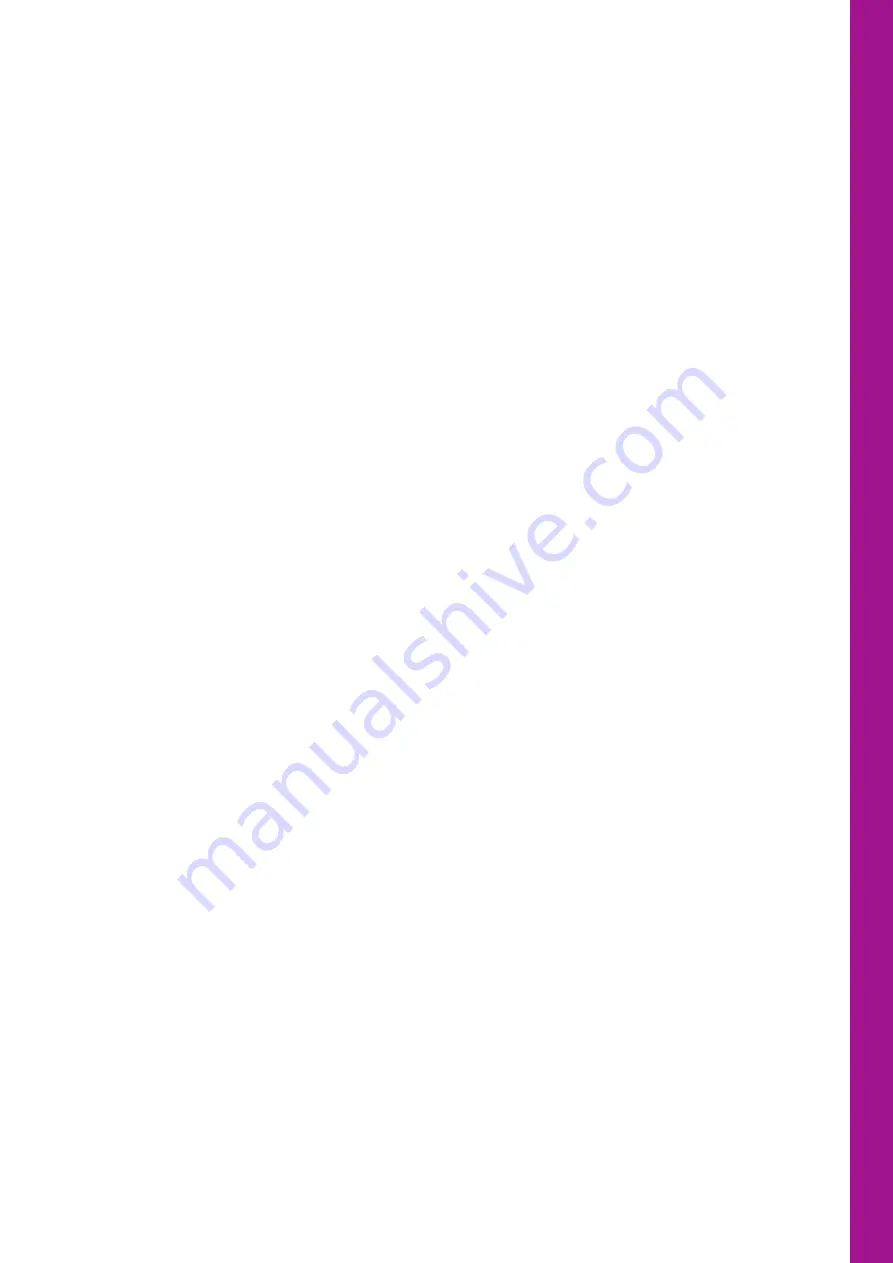
20
6.3 Gearbox
=> see the documentation for lifgo
®
, lifgo
®
linear and lean SL
®
The dimensions at the contact points with the gearbox can be found in the assembly drawings.
6.4 Unlocking
The attached air cylinder disengages a release bar from the gear rack and is held in this position
as long as pressure is still present in the cylinder. The mechanical arrest system is now unlocked.
6.5 Locking
When the air pressure is removed, a spring pushes the release bar forwards until it engages be-
tween the teeth of the gear rack. The mechanical arrest system is now locked. To increase locking
reliability, the air cylinder can also be moved in the direction of the spring. However, this is not
necessary for operation and is not provided for as standard.
6.6 Required procedure
Before a system is locked, it must be moved to the required height. The locking mechanism is then
activated by depressurizing the mechanical arrest system’s lifting cylinder. Complete locking is
only ensured once the system has slowly descended by a maximum of 8 mm after activation so
that the teeth in the gear rack and release bar engage with one another.
The angle of entry of the release bar into the gear rack guarantees that the mechanical arrest
system cannot become unlocked by itself.
In order to unlock the mechanical arrest system, the system must be raised approximately 5 mm.
6.7 Proximity switches
Two Festo proximity switches (type SME-8F-DS-24V-K0, 3-M8 LZ) are affixed to each air cylinder
in order to check the strokes. These query the position or state (locked or unlocked) of the mechani-
cal arrest system. The locking or unlocking operation is not completed until all 4 cylinders are
inserted or retracted and have emitted a signal.
Air is supplied via quick-fit connectors for 6 mm hoses.
6 Function description
20