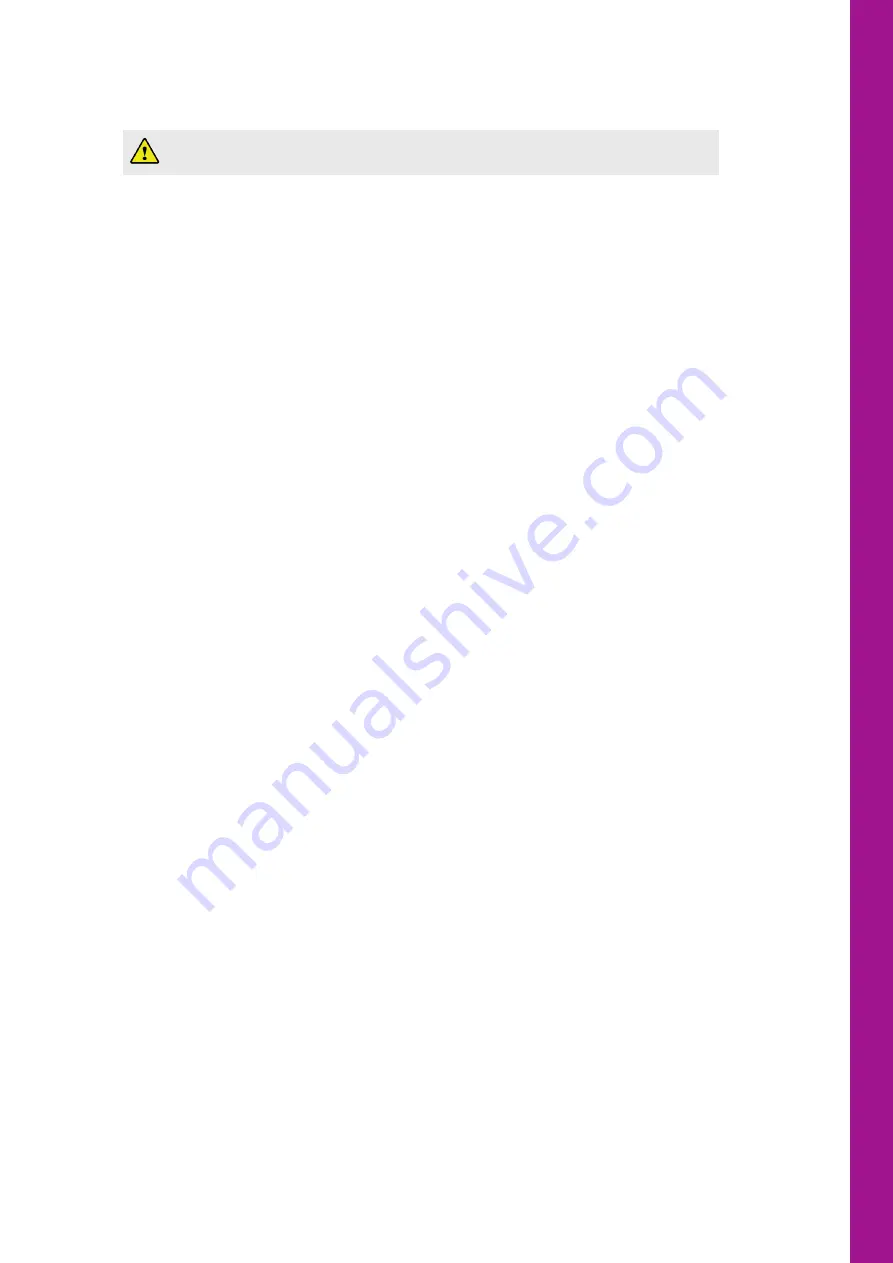
18
6 Function description
Caution!
The mechanical arrest system is not an emergency brake!
6.1 Operating process
The LEANTECHNIK AG mechanical arrest system (short name: ASS) is a mechanism designed
to prevent the uncontrolled descent of systems, system components or heavy weights and also to
prevent the unwanted application of forces and is attached to / installed in gear racks in combi-
nation with a lifgo
®
, lifgo
®
linear or lean SL
®
.
It is used to protect systems / machines / equipment etc. against falling or sudden collapse dur-
ing inspections or in the event of repair work.
When used in combination with a lifgo
®
or lean SL
®
gearbox, the ASS can also be used as a
positioning unit for a given value. Please consult us for further information!
The secured force is 5 times greater than the nominal force of the associated lifgo
®
or lean SL
®
gearbox. It is not permitted to exceed these forces at any time.
The force is secured in only one direction of movement (see drawing on the next page) which is
opposite to the load or lifting direction and only provided that an electronic drive containing a
service brake is used.
This protective device has a simple, robust method of operation. In normal operation, an air cylin-
der keeps the ASS open against a mechanical spring pressure. This is the “free-moving position”.
When it is necessary to apply the protective device, the system / machine / equipment is first
stopped.
The air is drained from the ASS air cylinder and the spring pressure forces the toothed bar to-
wards the gear rack. The inductive switch at the air cylinder indicates that the mechanism has left
its “free-moving” position. The system is now descended at low speed until the spring pressure
fully engages the toothed bar in the gear rack. When this “locked position” has been reached,
a second inductive switch indicates this to the control unit. The downward movement is stopped
immediately. The system / machine / equipment is now mechanically held in place by the inter-
locking components.
If the system has to be unlocked again then the air cylinder must be pressurized again. The system
/ machine / equipment is then lifted at low speed. The toothed bar is released and pressed back
by the pressure from the cylinder. The inductive switch first indicates that the locked position has
been exited and then that the free-moving position has been reached. The system / machine /
equipment can resume normal operation again.
In case there is a power supply failure, the system’s service brake must first be engaged. Shortly
afterwards, the air cylinder is depressurized. The toothed bar moves towards the gear rack to just
in front of the closest tooth. If the system / machine / equipment does not descend any further,
nothing else happens! If, for whatever reason, the system / machine / equipment continues to
descend, the spring pressure forces the toothed bar into the next possible tooth space and the
mechanical interlock halts the system / machine / equipment.
In accordance with VDE and EU guidelines, all the functions must be wired in a suitable control
unit as per DIN 60204.
6 Function description