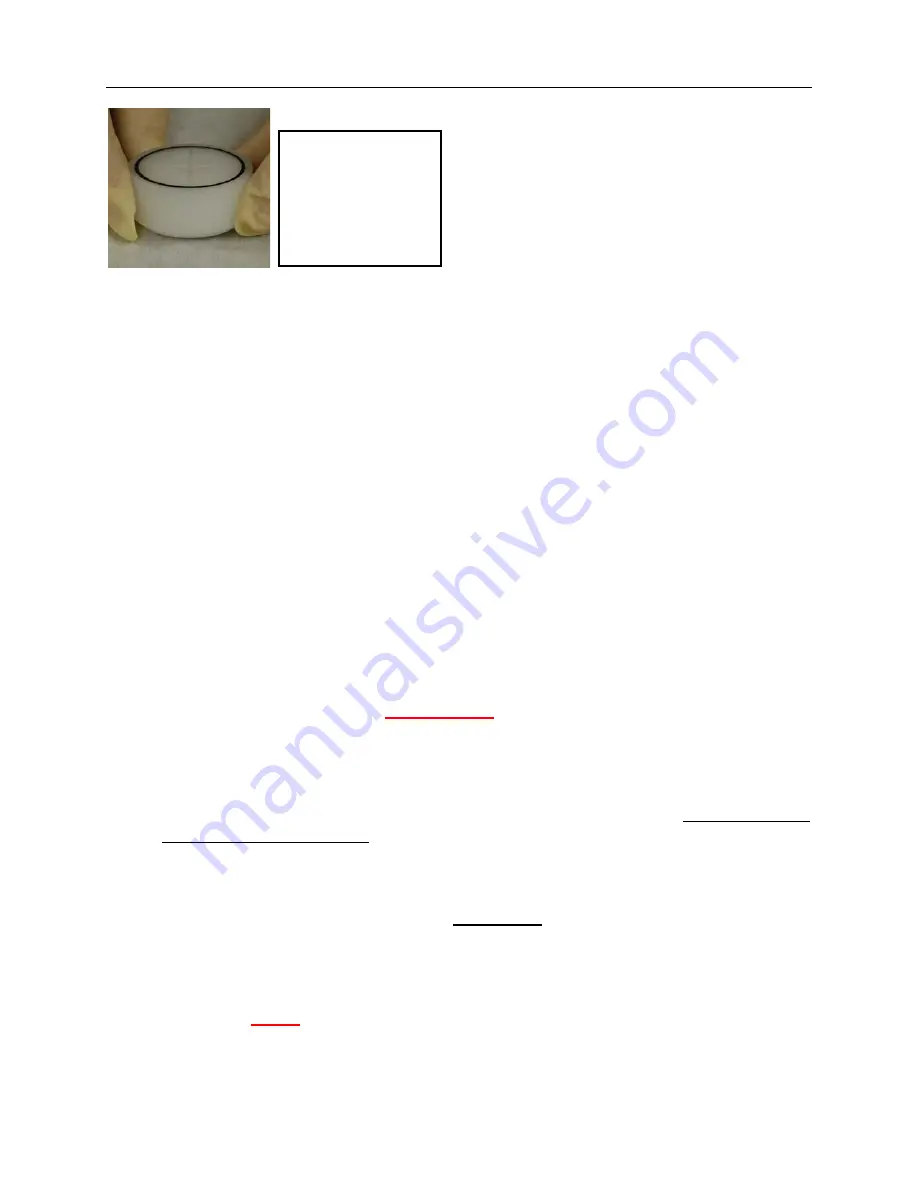
Laurell Technologies
Operations Manual WS-650 Lite Series
Revision Date: 7/26/2011
All information contained in this manual is the property of Laurell Technologies Corporation® and is NOT to be edited, reproduced or
distributed without express written permission from a corporate officer.
74
4.1.4.1 O-RING COMPOSITION, USES & RECOGNITION
We have determined that O-rings are the best way to insure a liquid-tight seal
between the chuck face and a non-porous substrate. The O-ring provides a
gripping as well as a sealing interface to our vacuum chuck and is normally
provided in two standard materials, Viton and EPDM.
The type O-ring which is installed on your chuck has been determined by the
chemicals which were specified when the spin processor was quoted. EPDM O-
rings are most commonly used for solvents while Viton is the choice where acids
or Toluene are present. You should determine before using the equipment what
chemical you will be using as well as the type O-ring which is installed. A supply
of both type rings are usually shipped with each system in properly labeled clear
re-closable bags.
If O-rings become intermixed, an EPDM O-ring can usually be identified by the
dull finish as opposed to the relatively smooth texture of the Viton material (some
Viton O-rings are brown in color).
The vacuum chuck’s O-ring seal should NEVER deflect (> 0.002” / 50 microns). If
you experience substrate deflection or breakage this is not a design issue but
this is not normal so you
MUST STOP
immediately and contact our support
department for application assistance. If you have thin or fragile material we
have developed successful approaches to eliminate or minimize deflection and
breakage.
When using the fragment adapter it is recommended that only one size O-ring
should be used at a time. The simultaneous use of O-rings can add more grip
and support to the substrate but if not absolutely identical thickness can cause a
vacuum leak or even cause the material to break. When both O-rings are used
an improper seal may develop allowing chemical to enter the vacuum path (a
leading cause of machine failure).
Important:
The substrate must always fully
cover the face of the O-ring being used.
Note: If you notice a black residue on the O-ring or marking of the holding
surface either the O-ring is dirty or the material is being damaged by the process
chemistry.
STOP
immediately especially if fluid passes the sealing surface after
being under vacuum.
5 - Make a final
check to be sure
that the o-ring is
entirely seated.
Perform a chuck wet
test to ensure o-ring
sealing integrity.