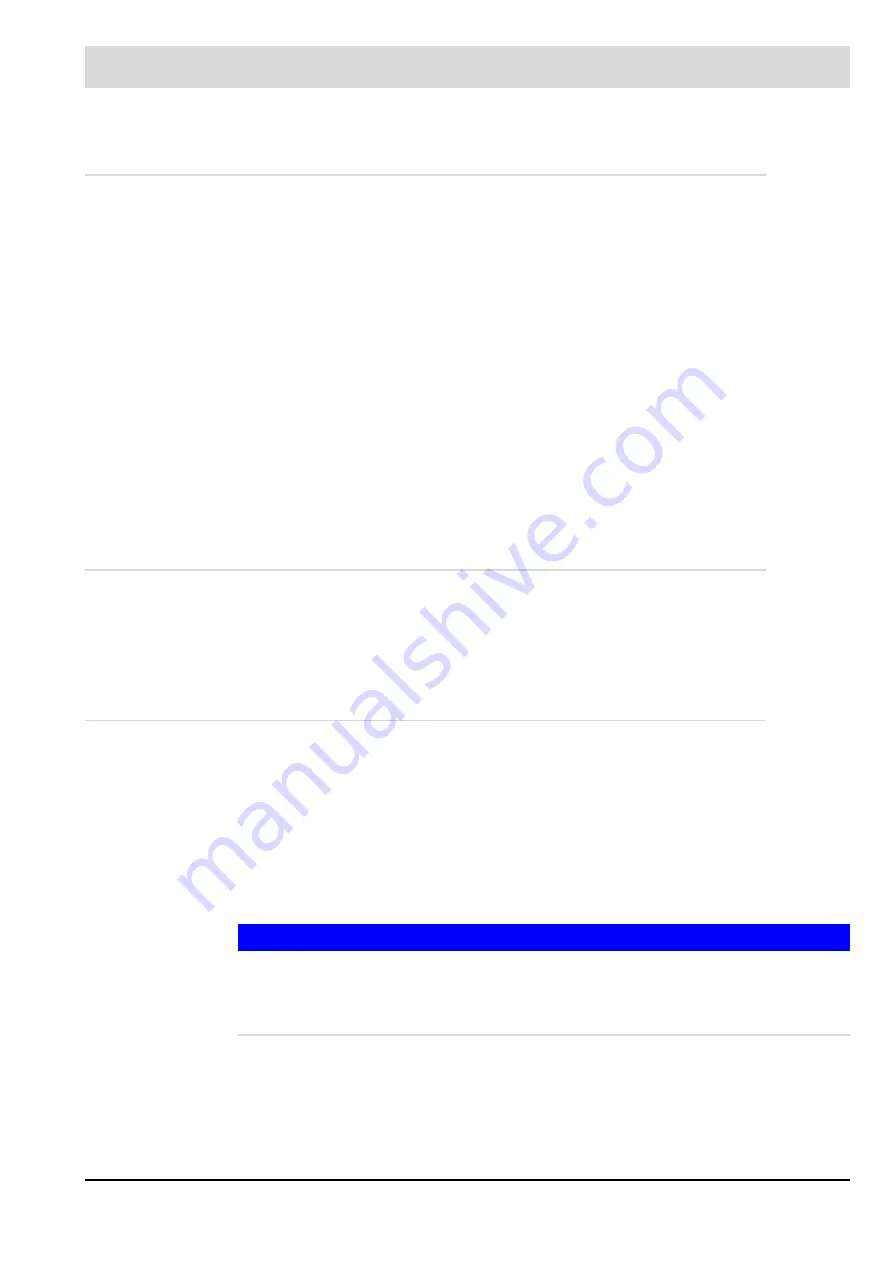
12
2
General Safety Instructions
2.2.1.2 Basic Device
Check the following items prior to commissioning:
•
Valves must be assigned correctly to valve outputs on BT300.
•
Correct setting of time parameters.
•
Functioning of flame sensor
–
in case of flame blow-off during operation
–
parasitic light being present during pre-purge period
–
missing flame formation at the end of the safety-period
•
Whether an approved self-checking flame sensor is used as only these types allow con-
tinuous operation.
•
The function of all existing or required input messages such as:
–
air pressure
–
Gas pressure - min / oil pressure - min
–
Safety chain (e.g. STL)
•
Activated valve leakage control function for gas valves if required for application purposes.
–
If so, check/adjust the correct leakage rate determination.
2.2.2
Tasks fulfilled by "authority on the subject" during Approval Test
By specifying the assigned DIN registration number and product ID number the manufacturer
confirms that model BT300 burner control system is consistent with type-tested system.
The connection between actuators and actuator elements for fuel and combustion air and also
to any additional actuator elements used must be form-fit.
2.2.2.1 Checking for Correct Parameter Setting in System
While installing and commissioning the plant the person in charge of the plant/heating techni-
cian needs to document the following:
•
Parameter set values
•
Setting values (e.g. curve progressions)
•
Values describing fuel/air ratio control.
This data can be printed using LSB Remote Software or alternatively being kept as a hand-
written note.
Retain this documentation and have it checked by the ’authority on the subject’.
NOTICE
For BT300 parameter settings which deviate from application standards can be carried out in
access level 2. For this reason, check whether the parameter settings are consistent with the
corresponding application standards (e.g. EN 676, EN 267, etc.) or the respective plant has
to be approved separately.
Содержание BT300 BurnerTronic
Страница 2: ......
Страница 21: ...20 3 Product Description Fig 3 3 UI300 and Fig 3 4 UI300 and dimensional drawings Fig 3 5 UI300 panel cut out...
Страница 25: ...24 3 Product Description Fig 3 9 Temperature derating BT300 for operation 2000 m NHN...
Страница 49: ...48 4 Design and Functions Fig 4 20 Oil with pilot burner BT300...
Страница 50: ...49 4 Design and Functions Fig 4 21 Oil without pilot burner BT300...
Страница 51: ...50 4 Design and Functions Fig 4 22 Gas with pilot burner and leakage test BT300...
Страница 52: ...51 4 Design and Functions Fig 4 23 Gas without pilot burner and leakage test BT300...
Страница 53: ...52 4 Design and Functions Fig 4 24 Oil without pilot burner BT335...
Страница 54: ...53 4 Design and Functions Fig 4 25 Gas without pilot burner and leakage test BT335...
Страница 59: ...58 4 Design and Functions Fig 4 28 Leakage test process diagram...
Страница 98: ...97 6 Operating Control and Displays...
Страница 99: ...98 6 Operating Control and Displays...
Страница 102: ...101 6 Operating Control and Displays NOTICE If the license agreements are not accepted the installation is aborted...
Страница 103: ...102 6 Operating Control and Displays...
Страница 105: ...104 6 Operating Control and Displays...
Страница 106: ...105 6 Operating Control and Displays...
Страница 107: ...106 6 Operating Control and Displays...
Страница 109: ...108 6 Operating Control and Displays...
Страница 126: ...125 6 Operating Control and Displays 6 3 4 2 Curve Table Fig 6 37 Curve table window...
Страница 246: ...242 10 EU Declaration of Conformity 10 EU Declaration of Conformity...
Страница 247: ...243 10 EU Declaration of Conformity...
Страница 248: ...244 10 EU Declaration of Conformity...