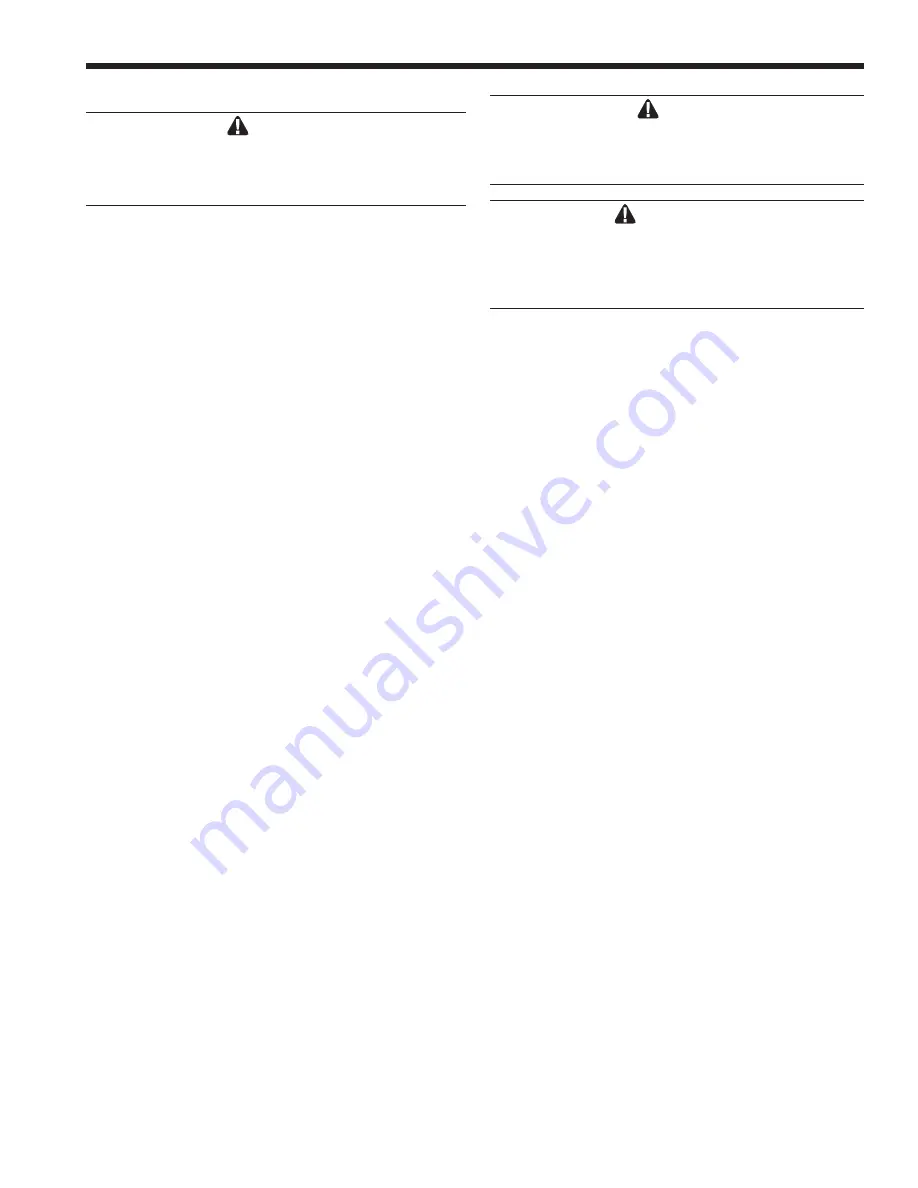
Page 79
SECTION 10 MAINTENANCE
WARNING
Disconnect all power to the appliance before
attempting any service. Contact with electricity can
result in severe injury or death.
10.A System Maintenance
Do the following once every 6 months.
1. On Outdoor models only as needed per air quality,
remove and inspect the air filter. Clean with soapy water
if needed. Be sure that filter is dry before re-inserting
back into air filter box. Replace air filter if damaged. .
Do the following once every year:
1. Lubricate all the pumps in the system, per the
instructions on the pump.
2. Inspect the venting system for obstruction or leakage.
Periodically clean the screens in the vent terminal
and combustion air terminal (when used).
3. Remove and inspect the air filter. Clean with soapy
water if needed. Be sure that filter is dry before re-
inserting back into air filter box. Replace air filter if
damaged.
4. Keep the area around the unit clear and free of
combustible materials, gasoline, or other flammable
vapors or liquids.
5. If the unit is not going to be used for extended
periods in locations where freezing normally occurs,
it should be isolated from the system and completely
drained of all water.
6. Low water cutoffs, if installed, should be checked
every year on commercial units. Residential models
need to be checked every 5 years. Float type low
water cutoffs should be flushed periodically.
7. Inspect and clean the condensate collection, float
switch and disposal system yearly.
8. When a means is provided to neutralize condensate,
ensure that the condensate is being neutralized
properly.
9. Inspect the flue passages, and clean them using
brushes or vacuums, if necessary. Sooting in flue
passages indicates improper combustion. Determine
the cause of the problem and correct it.
10. Inspect the vent system and air intake system, and
ensure that all joints are sealed properly. If any joints
need to be resealed, completely remove the existing
sealing material, and clean with alcohol. Apply new
sealing material, and reassemble.
11. The Pressure Relief Valve should be inspected and
tested every year.
10.B
Appliance Maintenance and
Component Description
Use only genuine replacement parts.
The gas and electric controls in the unit are engineered
for long life and dependable operation, but the safety
of equipment depends on their proper functioning. Only
a qualified service technician should inspect the basic
items listed below every year:
Burner
Check the burner for debris. Remove the blower arm
assembly to access the burner. Remove the four bolts
connecting the blower to the arm. (See Figure 47.)
Remove the five bolts which hold the burner arm in
place. Pull the burner up and out. Clean the burner, if
necessary, by blowing compressed air from the outside
of the burner into the center, and wipe the inside clean
with glass cleaner. A dirty burner may be an indication of
improper combustion or dirty combustion air. Determine
the cause of this, and correct it. If the burner gasket is
damaged, replace it when replacing the burner.
When Re-Installing the Burner Door,
ensure all
gaskets are properly seated and the mating surfaces are
clear and properly aligned. Any leakage of heat and flue
products will cause deformation and deterioration of the
metals which may result in permanent damage to the
heat exchanger assembly.
When mounting the burner door to the heat exchanger
first finger tighten each of the flange nuts using a star
pattern to ensure the door is properly aligning with
mounting surface. Continue to snug nuts using the star
pattern and a standard wrench. Finally using a torque
wrench tighten the nuts down to 44in. lbs. (5Nm).
See Figure 49 on page 80
a. Appliance control
b. Automatic gas valve
c. Air filter
d. Pressure switches
e. Blower
f. Pump
g. Flow switch
h. Low water cutoff
i. Burner
j. Heat exchanger
k. Ignitor
Caution
Label all wires prior to disconnection when servicing
controls. Wiring errors can cause improper and danger-
ous operation. Verify proper operation after servicing.
Avertissement
Tous les fils avant la déconnexion lors de l’entretien
des contrôles. Les erreurs de câblage peut causer le
mauvais et de danger-uo opération. Vérifier le fonc-
tionnement correct après l’entretien.
N
EO
T
HERM
Commercial Boilers and Water Heaters
Содержание Neotherm NTH
Страница 4: ...LAARS Heating Systems...
Страница 36: ...Page 36 Figure 22 Hydronic Piping Single Boiler Zoning with Circulators LAARS Heating Systems...
Страница 52: ...Page 52 Figure 36 Ladder Diagram 7 H Ladder Diagram LAARS Heating Systems...
Страница 100: ...Page 100 Parts Illustration 4 Internal Components Sizes 750 850 LAARS Heating Systems...
Страница 102: ...Page 102 Parts Illustration 6 Gas Train Components Sizes 600 850 LAARS Heating Systems...
Страница 103: ...Page 103 Parts Illustration 7 Heat Exchanger Components 68A Sizes 285 NEOTHERM Commercial Boilers and Water Heaters...