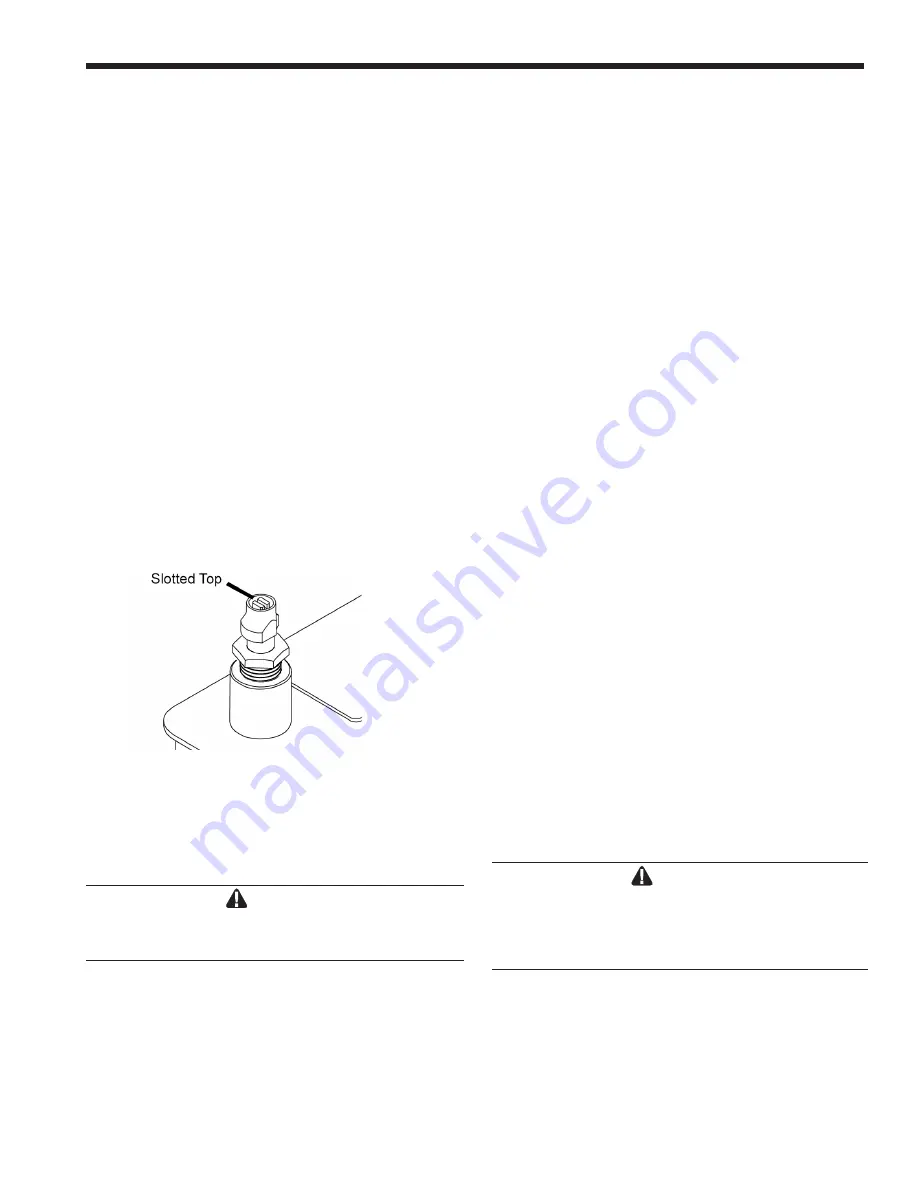
Page 77
Figure 48. Air Vent
9. Shut down the entire system and vent all radiation
units and high points in the system piping, as
described in Step 4.
10. Close the make-up water valve and check
the strainer in the pressure reducing valve for
sediment or debris from the make-up water line.
Reopen the make-up water valve.
11. Check the gauge for correct water pressure and
also check the water level in the system. If the
height indicated above the boiler insures that water
is at the highest point in the circulating loop, then
the system is ready for operation.
12. Prime the condensate trap with water. (This is not
required for Boiler 600, 750, and 850 units.)
13. Refer to local codes and the make-up water valve
manufacturer’s instructions as to whether the
make-up water valve should be left open or closed.
14. After placing the unit in operation, the ignition
system safety shutoff device must be tested.
First, shut off the manual gas valve, and call
the unit for heat. The main gas terminals will be
energized, and attempt to light, for four seconds,
and then will de-energize. The unit will go into
lockout after the required number of trial for ignition
periods.
Next, turn the power Off, and then On again.
Press the manual reset button on the boiler control,
open the manual gas valve, and allow the unit to
light. While the unit is operating, close the manual
gas valve and ensure that power to the main gas
valve has been cut.
15. Within three days of start-up, recheck all air
bleeders and the expansion tank as described in
Step 4.
Important Note:
The installer is responsible for
identifying to the owner/operator the location of all
emergency shutoff devices.
WARNING
Do not use this appliance if any part has been under
water. Manufacturer requires boilers and water
heaters to be replaced, not repaired, if they have
been partially or completely submerged.
SECTION 9 FIRST START UP AND
ADJUSTMENT
9.A Filling the Boiler System
1. Ensure the system is fully connected. Close all
bleeding devices and open the make-up water
valve. Allow the system to fill slowly.
2. If a make-up water pump is employed, adjust the
pressure switch on the pumping system to provide
a minimum of 12 psi (81.8 kPa) at the highest
point in the heating loop.
3. If a water pressure regulator is provided on the
make-up water line, adjust the pressure regulator
to provide at least 12 psi (81.8 kPa) at the highest
point in the heating loop.
4. Open all of the bleeding devices on all radiation
units at the high points in the piping throughout
the system, unless automatic air bleeders are
provided at these points.
Note
- There is an air bleed (air vent with slotted
top) located on the left side of heat exchanger, on
top of the water manifold.
5. To remove all air from the heat exchanger, cycle
the boiler pump on and off 10 times, 10 seconds
on and 10 seconds off, . Then run the system and
appliance pumps for a minimum of 30 minutes with
the gas shut off.
WARNING
Failure to remove all air from the heat exchanger could
lead to property damage, severe injury or death.
6. Open all strainers in the circulating system, check
the operation of the flow switch (if equipped), and
check for debris. If any debris is present, clean it
out to ensure proper circulation.
7. Recheck all air bleeders as described in Step 4.
8. Start up the boiler according to the procedure listed
in this manual. Operate the entire system, including
the pump, boiler, and radiation units for one hour.
N
EO
T
HERM
Commercial Boilers and Water Heaters
Содержание Neotherm NTH
Страница 4: ...LAARS Heating Systems...
Страница 36: ...Page 36 Figure 22 Hydronic Piping Single Boiler Zoning with Circulators LAARS Heating Systems...
Страница 52: ...Page 52 Figure 36 Ladder Diagram 7 H Ladder Diagram LAARS Heating Systems...
Страница 100: ...Page 100 Parts Illustration 4 Internal Components Sizes 750 850 LAARS Heating Systems...
Страница 102: ...Page 102 Parts Illustration 6 Gas Train Components Sizes 600 850 LAARS Heating Systems...
Страница 103: ...Page 103 Parts Illustration 7 Heat Exchanger Components 68A Sizes 285 NEOTHERM Commercial Boilers and Water Heaters...