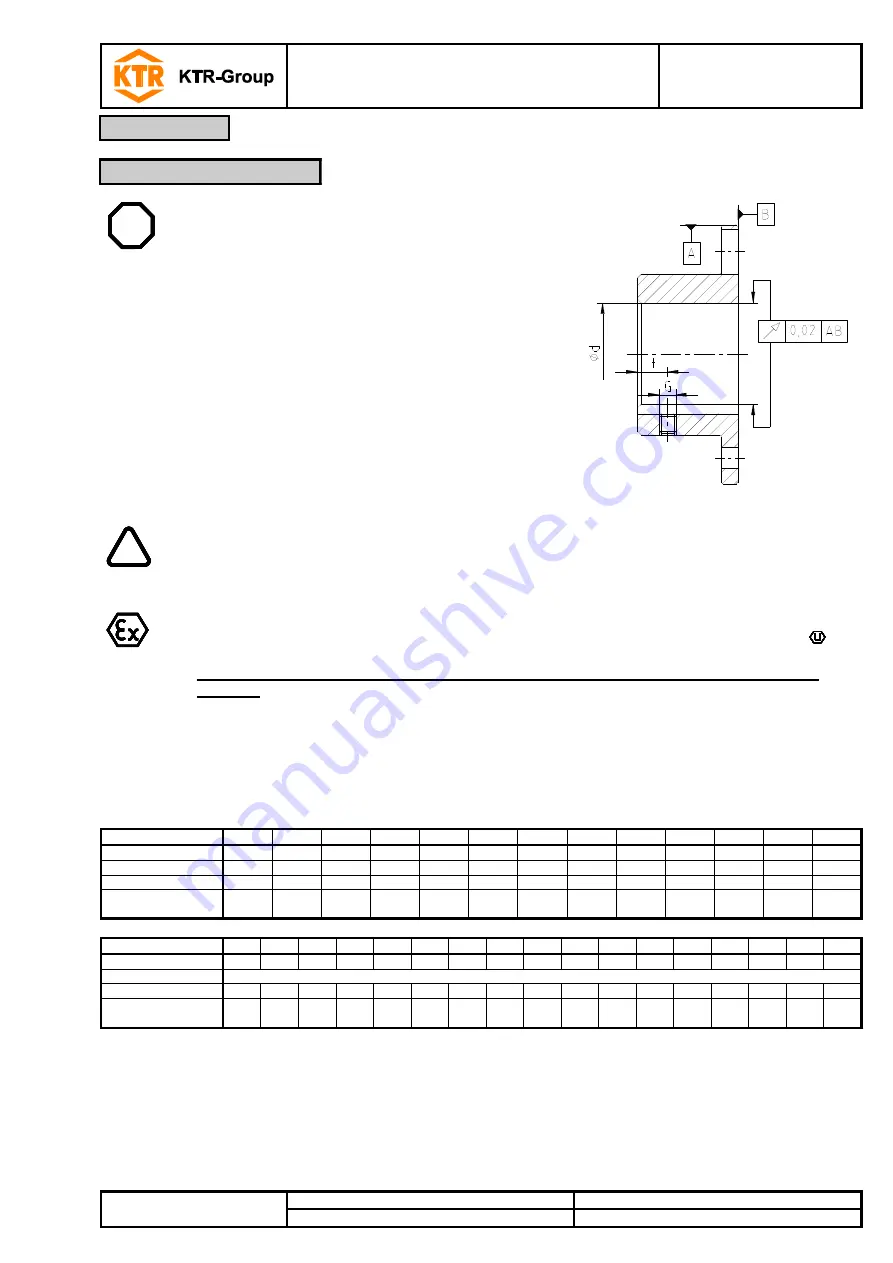
RADEX
®
-N
Operating/Assembly instructions
KTR-N
Sheet:
Edition:
47110 EN
13 of 31
24
Please observe protection
note ISO 16016.
Drawn:
2019-07-23 Pz/Wb
Replacing:
KTR-N dated 2018-07-17
Verified:
2019-07-26 Pz
Replaced by:
STOP
The maximum permissible bore diameters d (see
chapter 1 - technical data) must not be exceeded.
If these figures are disregarded, the coupling may
tear. Rotating particles may cause danger to life.
Illustration 16: Concentricity and axial run-out
•
Bores of flange hubs machined by the customer have to observe
concentricity or axial runout, respectively (see illustration 16).
•
Please make absolutely sure to observe the figures for Ø d
max
.
•
Carefully align the flange hubs when the finish bores are drilled.
•
Please provide for a setscrew according to DIN EN ISO 4029 with
a cup point or an end plate to fasten the flange hubs axially.
!
The customer bears the sole responsibility for all machining processes performed
subsequently on unbored or pilot bored as well as finish machined coupling components
and spare parts. KTR does not assume any warranty claims resulting from insufficient
remachining.
KTR supplies unbored or pilot bored coupling components and spare parts only upon
explicit request of the customer. These parts are additionally marked with the symbol
.
Reference to unbored resp. pilot bored coupling components with explosion protection
marking:
Basically the company KTR supplies couplings resp. coupling hubs with explosion protection
marking as an unbored or pilot bored type only on explicit request of the customer. The prerequisite
is a declaration of exemption submitted by the customer assuming any responsibility and liability for
remachining performed properly.
Table 7: Setscrew DIN EN ISO 4029
Size
20
25
35
38
42
50
60
70
80
85
90
105
115
G
M5
M5
M6
M6
M8
M8
M8
M10
M10
M10
M12
M12
M12
t
6
8
15
15
20
20
20
20
20
25
25
30
30
Number z
1
1
1
1
1
1
1
1
1
1
1
1
1
Tightening torque T
A
[Nm]
2
2
4.8
4.8
10
10
10
17
17
17
40
40
40
Size
135
136
156
166
186
206
246
286
336
138
158
168
188
208
248
288
338
G
M20 M12 M12 M16 M16 M16 M20 M20 M24 M12 M12 M16 M16 M16 M20 M20 M24
t
As specified by the customer
Number z
1
2
2
2
2
2
2
2
2
2
2
2
2
2
2
2
2
Tightening torque T
A
[Nm]
140
40
40
80
80
80
140
140
240
40
40
80
80
80
140
140
240
4
Assembly
4.2 Advice for finish bore