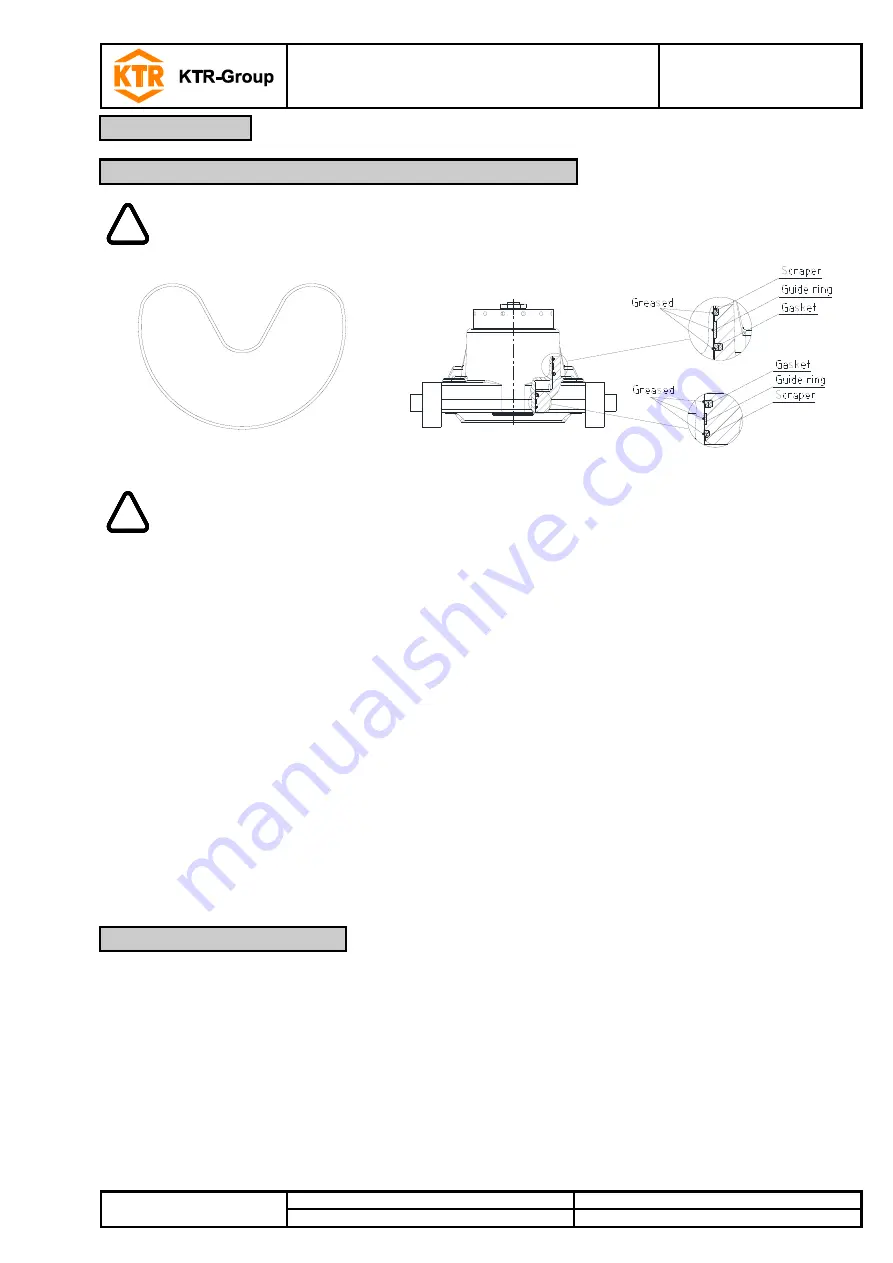
KTR-STOP
®
M-xxx B-xx-xx
Operating/Assembly instructions
KTR-N
Sheet:
Edition:
445102 EN
20 of 22
3
Please observe protection
note ISO 16016.
Drawn:
2020-03-25 Shg/Wie
Replacing:
KTR-N dated 2019-08-26
Verified:
2020-03-25 Shg
Replaced by:
!
Oils and greases containing molybdenum disulphite or zinc sulphite additives must not be
used.
Illustration 15: Assembly of gasket and scraper
Illustration 16
!
Inspect the surfaces of the brake piston and the hole of the housing to make sure that they
are neither scratched nor damaged, since the surfaces are either ground or polished. Such
kind of damages may cause earlier wear on the gaskets and scrapers and generate leaka-
ges.
•
Insert the brake piston (component 1.2) into the housing and press it against a stop.
•
Shift the set of disk springs (component 1.6) into the brake piston (component 1.2). Make sure that the disks
are located on top.
Grease the disk springs properly with Molykote MoS
2
.
Please make sure that the set of disk springs is mounted in the same arrangement as it was
supplied.
If a new set of disk springs is used, the condition of supply needs to be observed in detail.
•
Screw the setting nut (component 1.7) into the housing and set it to the right dimension (see illustration 12).
•
Put the opening pressure (see table 2) onto the hydraulic system.
•
Hand-tighten the screw with the disk (assembly lock, see illustration 11) into the setting nut (component 1.7).
•
Release the pressure from the hydraulic system.
•
Insert a new O-ring (component 1.9) between the housing and the setting nut.
•
Repeat chapters 4.2 to 4.8.
KTR-STOP
®
M-xxx B-xx-xx
is a low-maintenance brake. We recommend to perform a visual inspection and an
operational testing on the brake
at least once a year
. Here you should put special emphasis on leakages, corro-
sion, wear of brake pads and the condition of the screw connections.
If you realize any irregularities, please perform repairs accordingly.
5
Maintenance
5.2 Maintenance of the brake / replacement of single parts
5.3 Maintenance and service