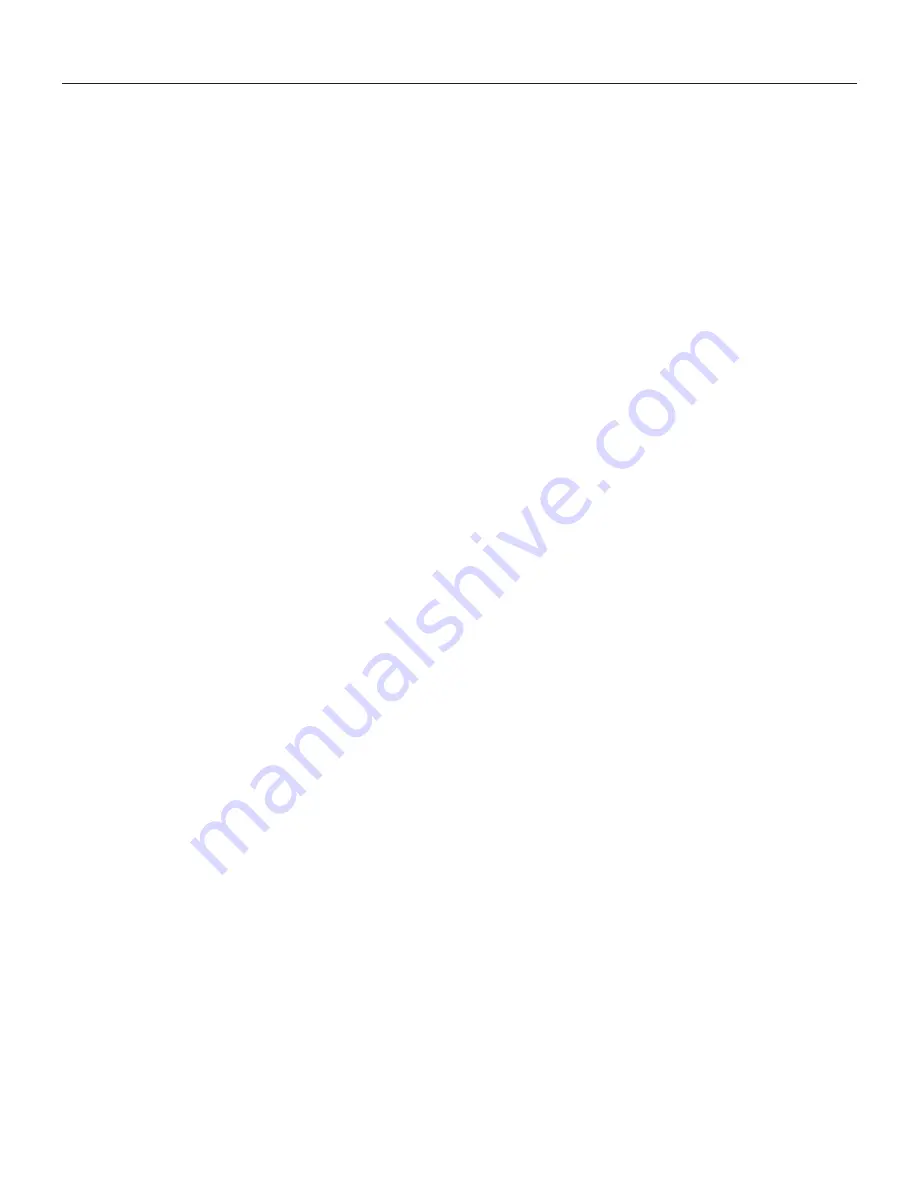
6
INTRODUCTION
1.1 Appliance Certification
Laboratory:
OMNI-Test Laboratories in Portland, Oregon
Standards:
• ANSI Z21.88-2014/CSA 2.33-2014,
Vented Gas Fireplace
Heaters
• CGA 2.17-M91 (R2009),
Gas-Fired Appliances for Use at High
Altitudes
• CSA P.4.1-2009,
Testing Method for Measuring Annual
Fireplace Efficiency
This installation must conform with local codes, or in the absence
of local codes, with the
National Fuel Gas Code, ANSI Z223.1/
NFPA 54, or the
Natural Gas and Propane Installation Code, CSA
B149.1.
1.2 Requirements for the
Commonwealth of Massachusetts
The following requirements reference various Massachusetts
and national codes not contained in this manual.
For all sidewall horizontally vented gas fueled equipment installed
in every dwelling, building or structure used in whole or in part for
residential purposes, including those owned or operated by the
Commonwealth and where the side wall exhaust vent termination
is less than (7) feet above finished grade in the area of the venting,
including but not limited to decks and porches, the following
requirements shall be satisfied:
1.2.1 Installation of Carbon
Monoxide Detectors
At time of installation of side wall horizontally vented gas fueled
equipment, the installing plumber or gas-fitter shall observe that
a hard wired carbon monoxide detector with an alarm and battery
back-up is installed on the floor level where the gas equipment is
to be installed. In addition, the installing plumber or gas-fitter shall
observe that a battery operated or hard wired carbon monoxide
detector is installed on each additional level of the dwelling,
building or structure served by the side wall horizontal vented
gas fueled equipment. It shall be the responsibility of the property
owner to secure the services of qualified licensed professionals for
the installation of hard wired carbon monoxide detectors.
In the event that the side wall horizontally vented gas fueled
equipment is installed in a crawl space or attic, the hard wired
carbon monoxide detector with alarm and battery back-up may
be installed on the next adjacent floor level. In the event that
the requirements of this subdivision can not be met at the time
of completion of installation, the owner shall have a period of
thirty (30) days to comply with the above requirements; provided,
however, that during said thirty (30) day period, a battery operated
carbon monoxide detector with an alarm shall be installed.
1.2.2 Approved Carbon Monoxide Detectors
Each carbon monoxide detector as required in accordance with
the above provisions shall comply with NFPA 720 and be ANSI/UL
2034 listed and IAS certified.
1.2.3 Signage
A metal or plastic identification plate shall be permanently mounted
to the exterior of the building at a minimum of eight (8) feet
above grade directly in line with the exhaust vent terminal for the
horizontally vented gas fueled heating appliance or equipment. The
sign shall read, in print no less the one-half inch (½) in size, “GAS
VENT DIRECTLY BELOW. KEEP CLEAR OF ALL OBSTRUCTIONS”.
1.2.4 Inspection
The state or local gas inspector of the side wall horizontally
vented gas fueled equipment shall not approve the installation
unless, upon inspection, the inspector observes carbon monoxide
detectors and signage installed in accordance with the provisions
of 248 CMR 5.08 (2) (a) 1 through 4.
1.2.5 Exemptions
The following equipment is exempt from 248 CMR 5.08 (2) (a) 1
through 4: The equipment listed in Chapter 10 entitled “Equipment
Not Required To Be Vented” in the most current edition of NFPA
54 as adopted by the Board; and Product Approved side wall
horizontally vented gas fueled equipment installed in a room or
structure separate from the dwelling, building or structure used in
whole or in part for residential purposes.
1.2.6 Manufacturer Requirements
1.2.6.1 Gas Equipment Venting System Provided
When the manufacturer of Product Approved side wall horizontally
vented gas equipment provides a venting system design or venting
system components with the equipment, the instructions provided
by the manufacturer for installation of the equipment and the
venting system shall include:
• Detailed instructions for the installation of the venting system
design or the venting system components; and
• A complete parts list for the venting system design or venting
system.
1.2.6.2 Gas Equipment Venting
System NOT Provided
When the manufacturer of Product Approved side wall horizontally
vented gas equipment does not provide the parts for venting the
flue gases, but identifies “special venting systems”, the following
requirements shall be satisfied by the manufacturer:
• The referenced “special venting systems” instructions shall
be included with the appliance or equipment installation
instructions and;
• The “special venting systems” shall be Product Approved by
the Board, and the instructions for that system shall include a
parts list and detailed installation instructions.
A copy of all installation instructions for all Product Approved
side wall horizontally vented gas fueled equipment, all venting
instructions, all parts lists for venting instructions, and/or all venting
design instructions shall remain with the appliance or equipment at
the completion of the installation.
1.0 INTRODUCTION