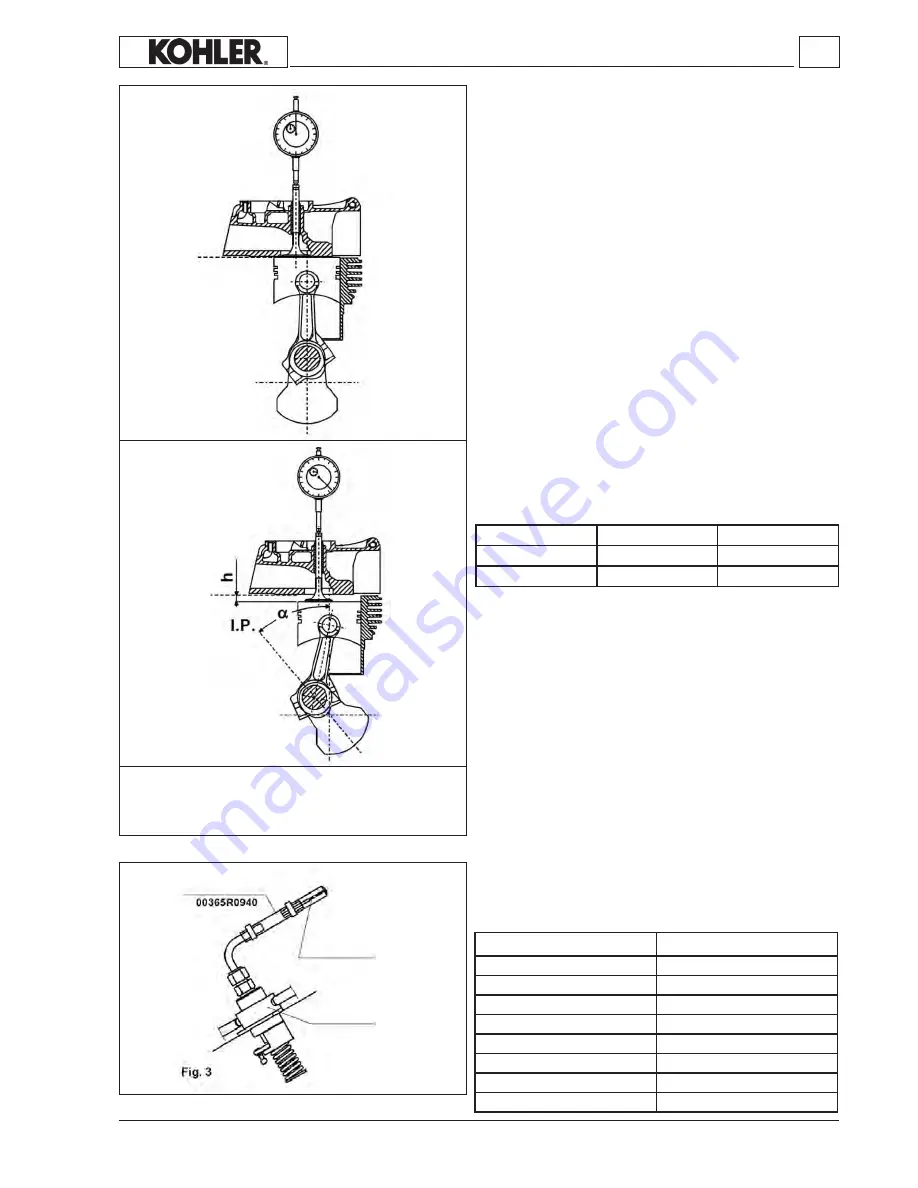
- 43 -
- 43 -
17
PMS
PMS
Fig. 1
Fig. 2
3000
2,735 mm
18°
3600
4,427 mm
23°
2,443 mm
17°
2,735 mm
18°
3,043 mm
19°
3,336 mm
20°
3,704 mm
21°
4,058 mm
22°
4,427 mm
23°
4,811 mm
24°
SUGGESTIONS ON HOW TO TIME THE INJECTION PUMP
WHEN THE LEAD PUNCH MARKS ON THE FLYWHEEL ARE
DIFFICULT TO REACH.
(Consult chapter "Injection lead" on page 37 for a description of
the conventional adjustment)
Proceed in the following way:
1.
Remove the cover from the rocker arms.
2.
Demount the recoil and turn the drive shaft to the valve
regulation position.
(This operation is carried out by means of the fylwheel nut,
using a N° 32 socket wrench).
3.
Demount the intake or exhaust rocker arm, the valve spring
and caps.
4.
Rest the valve top on the crown of the T.D.C. balanced piston
(fig.1).
WARNING: The valve slips from its guide if the piston is
lowered by turning the drive shaft more than 1/4 of a pipe
wrench turn.
5.
Position a comparator mounted on a magnetic pedestal or
dummy injector and reset it on the valve stem (fig.1).
6.
Slowly turn the drive shaft in an anti-clockwise direction and
check the comparator to make sure that the piston drops
about 5 mm in relation to TDC (dimension "h" - fig. 2).
7.
Slowly turn the drive shaft in a clockwise direction and check
the comparator to make sure that the piston rises by the
values indicated in the following table, in relation to TDC
(dimension "
h
" - fig. 2):
8.
Remove the injection tube and mount the capillary tube code
00365R0940
on the injection pump delivery fitting (fig. 3).
9.
Turn the accelerator lever to the MAX position and the stop
lever to about half travel.
10.
Turn the drive shaft anti-clockwise by no more than 1/4 of the
pipe wrench turn.
11.
Pressurize the circuit by turning the drive shaft several times in
an alternate clockwise/anti-clockwise way until fuel splashes
out of the calibrated hole of the capillary tube.
12.
Turn the drive shaft and check the comparator to make
sure that the piston drops about 10 mm in relation to TD.
(dimension (quota "
h
" - fig. 2).
13.
Shake the capillary tube until an air bubble forms inside it (fig.
3).
14.
Turn the drive shaft in a clockwise direction very slowly and
check the position of the air bubble in the capillary tube. A
small movement of this bubble will indicate the exact lead
position. This value must correspond to the one previously
read on the comparator (see point 7). If this is not the case,
add or remove seals to or from the injection pump according
to the corrections indicated in the following table:
Capillary tube
TDC
= top dead center
h
= extent of piston lowering in relation to TDC.
α
= angle corresponding to piston lowering in relation to T.D.C.
I.P.
= start of delivery
Air bubble
Injection pump
SERVICE
rpm
h
α
rpm
Lead IP
Workshop Manual KD500 _ cod. ED0053029390 -
1° ed
_rev.
00
Содержание KD 500
Страница 1: ...KD 500 WORKSHOP MANUAL...
Страница 6: ...6 Index Workshop Manual KD500 _ cod ED0053029390 1 ed_rev 00...