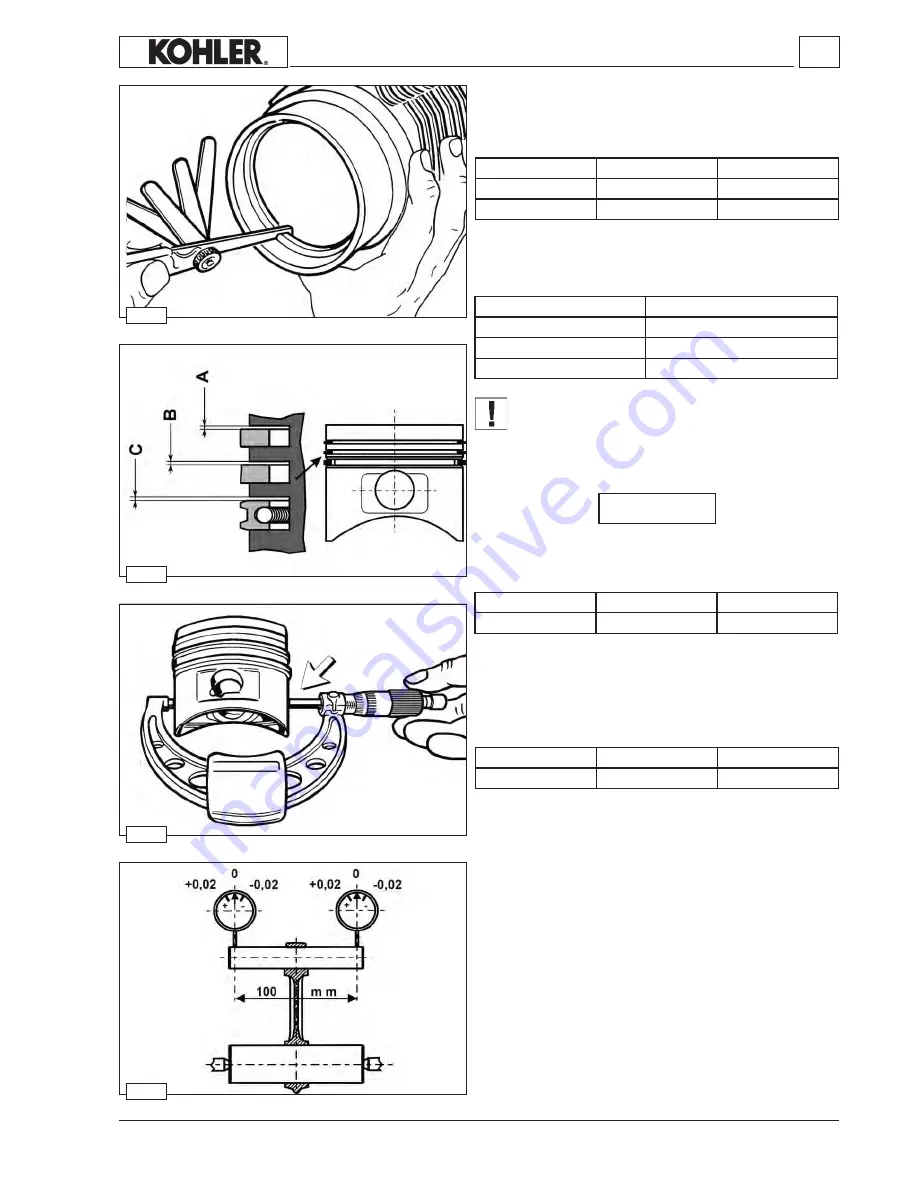
- 21 -
- 21 -
19
18
17
16
10
0,30 ÷ 0,50
0,80
0,25 ÷ 0,50
0,80
A = 0,22
B = 0,19
C = 0,16
21,997 ÷ 22,002
0,003 ÷ 0,013
0,040
21,997 ÷ 22,002
0,023 ÷ 0,038
0,070
Checks and overhaul
Piston rings - Piston - Pin
To gauge the wear on the piston rings, put them into the cylinder
from the bottom side and measure the distance between the free
ends (fig. 16), which must be:
Make sure that the piston rings slide smoothly in the slots and
use a thickness gauge to check the play between the slot and
ring (fig. 17). Replace the piston and rings if the play exceeds:
Piston ring
Fitting mm
Max. wear mm
Compression
Oil scrapper
WARNING: it is advisable to replace the piston rings
whenever the piston is demounted.
Checking the piston diameter: the diameter of the piston
must be measured at a distance from the base (fig. 18) of
approximately 11 mm.
Ø 86,915 ÷ 86,835
Check the play between cylinder and piston. Replace the parts if
play exceeds 0.150 mm.
Play between pin and piston mm:
Piston ring
Max. wear mm
1st Compression
2nd Compression
3rd Oil scrapper
Pin Ø mm
Assy.clearance mm
Max. wear mm
Pin Ø mm
Assy.clearance mm
Max. wear mm
Connecting rod
Coupling between the small end hole of the connecting rod and
pin is made without a bearing.
Play between connecting rod small end and pin mm:
Check connecting rod axes parallelism in the following way:
1.
Insert the pin into the small end hole of the connecting rod
and a calibrated plug into the big end (with the bearing
mounted).
2.
Rest the plug on two prisms arranged on a surface plate or
between two centers (fig. 19).
3.
Use a centesimal comparator to check that the difference
between the readings made at the ends of the pin does
not exceed
0.02 mm
. square up the connecting rod if the
deformation is greater (
max. 0.05 mm
).
Workshop Manual KD500 _ cod. ED0053029390 -
1° ed
_rev.
00
Содержание KD 500
Страница 1: ...KD 500 WORKSHOP MANUAL...
Страница 6: ...6 Index Workshop Manual KD500 _ cod ED0053029390 1 ed_rev 00...