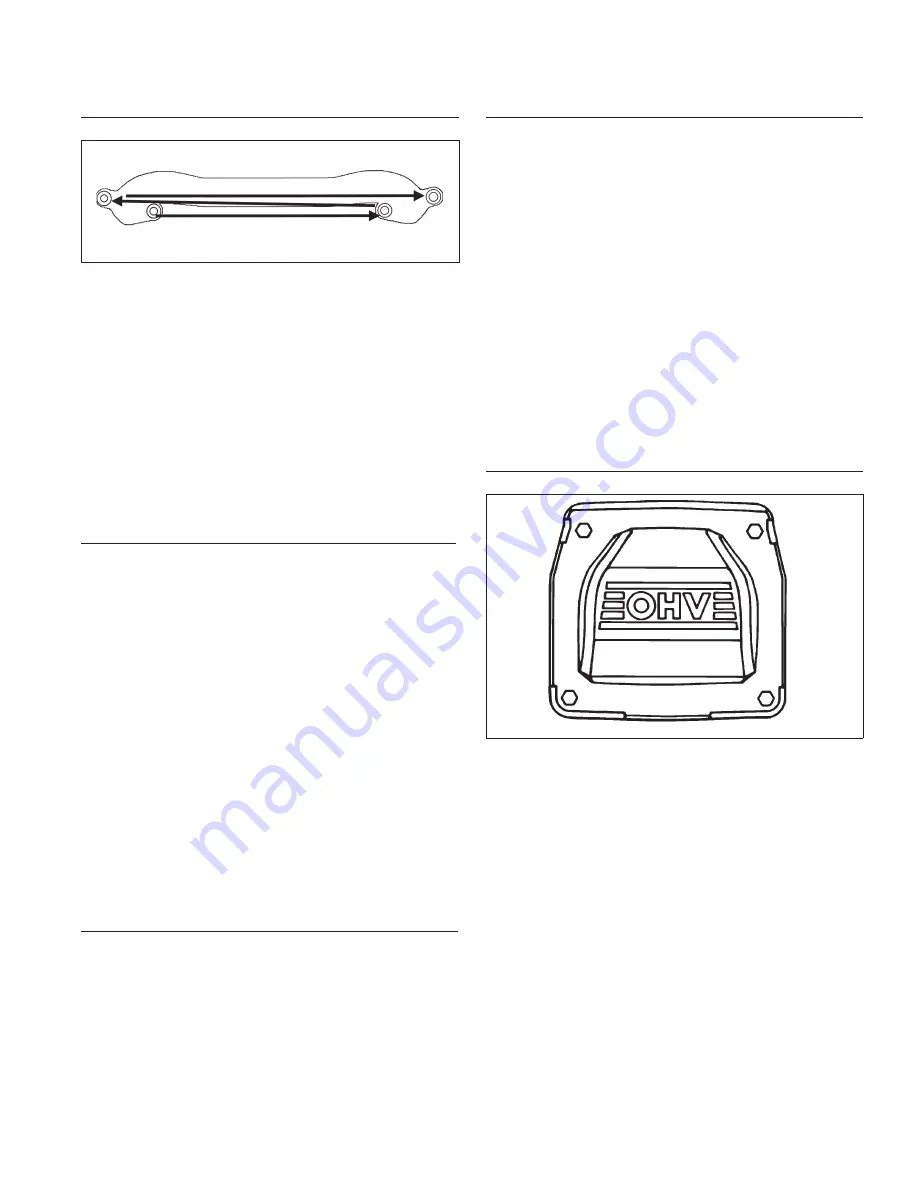
85
Reassembly
24 690 31 Rev. D
KohlerEngines.com
Install Intake Manifold
Torque Sequence
1
2
3
4
1. Install intake manifold (with high pressure fuel line
assembly) and new gaskets, with wiring harness
attached, to cylinder heads. Slide any wiring harness
clips onto appropriate bolts before installing. Make
sure gaskets are in proper orientation. Using
sequence shown, torque screws in 2 stages, fi rst to
7.8 N·m (69 in. lb.), then to 10.5 N·m (93 in. lb.).
2. Install ground terminal to crankcase post with a
silver screw. Torque to 4.0 N·m (35 in. lb.) into used
holes or 6.2 N·m (55 in. lb.) in new holes.
3. Install wire harness clip to other crankcase post.
Torque to 4.0 N·m (35 in. lb.) into used holes or 6.2
N·m (55 in. lb.) in new holes.
4. Place wire harness conduit in clip and snap clip
together.
Install Fuel Injectors
NOTE: Ensure all parts are clean, undamaged and free
of debris and make sure electrical connectors
have seal in place.
O-rings and retaining clips should be replaced
any time fuel injector is separated from its
normal mounting position.
1. Lightly lubricate fuel injector O-rings with clean
engine oil.
2. Push retaining clip onto fuel injector, aligning clip.
3. Press fuel injector into fuel injector cap until retaining
clip snaps into place.
4. Press fuel injector into bore in intake manifold and
rotate to original position.
5. Install fuel injector cap screw into intake manifold
and torque to 7.3 N·m (65. in. lb.).
6. Push electrical connector on fuel injector making
sure a good connection is made.
7. Repeat steps 1 through 6 for other fuel injector.
Install Manifold Absolute Pressure (MAP) Sensor or
Temperature/Manifold Absolute Pressure (TMAP)
Sensor
NOTE: Ensure all parts are clean, undamaged and free
of debris and make sure electrical connector has
seal in place.
1. Lightly oil MAP or TMAP sensor O-ring and push
sensor into bore in intake manifold.
2. Torque screw to 7.3 N·m (65 in. lb.).
3. Push electrical connector on MAP or TMAP sensor
making sure a good connection is made.
Install Crankshaft Position Sensor
NOTE: Ensure all parts are clean, undamaged and free
of debris and make sure electrical connectors
have seal in place.
NOTE: On engines with earlier design bracket, an air
gap must be set when installing. Later design
brackets require no adjustment.
1. Install crankshaft position sensor and bracket
assembly to crankcase posts.
2. On engines with earlier design bracket, snug screws
and check air gap of sensor with a feeler gauge. It
must be 0.20-0.70 mm (0.008-0.027 in.). Torque
bracket screws to crankcase to 4.0 N·m (35 in. lb.)
into used holes or 6.2 N·m (55 in. lb.) into new holes.
On engines with later design bracket, secure bracket
assembly to crankcase posts. Torque bracket screws
to crankcase to 4.0 N·m (35 in. lb.) into used holes
or 6.2 N·m (55 in. lb.) into new holes.
3. Push electrical connector on crankshaft position
sensor making sure a good connection is made.
Install Valve Covers
Torque Sequence
1
2
3
4
1. Make sure sealing surfaces are clean.
2. Make sure there are no nicks or burrs on sealing
surfaces.
3. Install a new O-ring in groove of each cover.
4. Position covers on cylinder heads. Locate cover with
oil separator hole on cylinder 1. Install screws in
each cover and fi nger tighten.
5. Torque valve cover fasteners to 6.2 N·m (55 in. lb.).