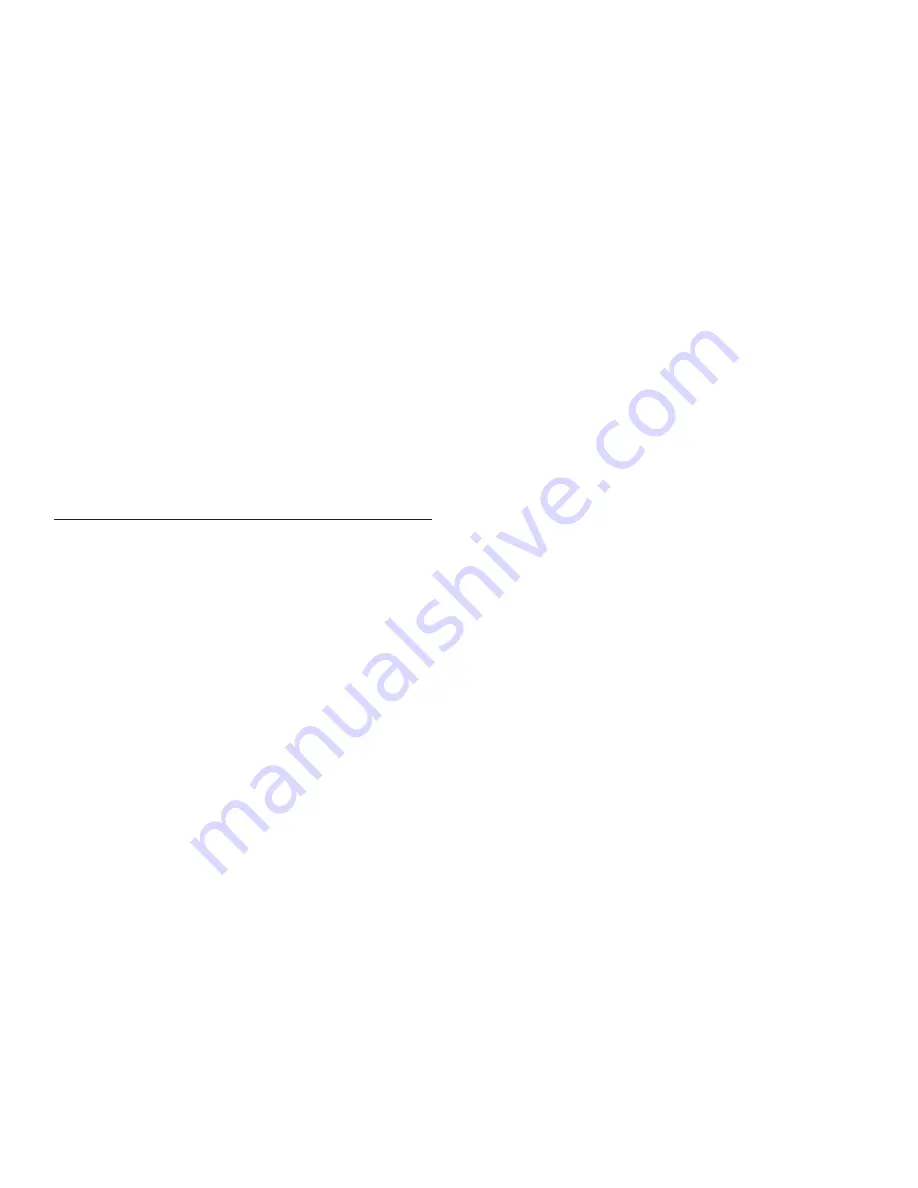
Propane EFI System
38
24 690 31 Rev. D
KohlerEngines.com
7. Reverse appropriate procedures to install new
injector(s) and reassemble engine. Use new O-rings
and retaining clips any time an injector is removed
(new replacement injectors include new O-rings and
retaining clips). Lubricate O-rings lightly with clean
engine oil. Use installation tool provided with O-rings
to install new upper O-ring. Place tool into fuel
injector inlet. Place one side of O-ring into O-ring
groove and roll O-ring over tool onto fuel injector.
Torque screw securing fuel injector caps and blower
housing mounting screws to 7.3 N·m (65 in. lb.), and
intake manifold and air cleaner mounting screws to
10.5 N·m (93 in. lb.). An ECU Reset will need to be
completed.
Injector problems due to dirt or clogging are generally
unlikely due to design of injectors and high fuel pressure.
Symptoms that could be caused by dirty/clogged
injectors include rough idle, hesitation/stumbling during
acceleration, or triggering of fault codes related to fuel
delivery. Injector clogging is usually caused by a buildup
of deposits on director plate, restricting fl ow of fuel,
resulting in a poor spray pattern. Some contributing
factors to injector clogging include higher than normal
operating temperatures, short operating intervals, and
dirty, incorrect, or poor quality fuel. Cleaning of clogged
injectors is not recommended; they should be replaced.
Ignition Coil
If a coil is determined to be faulty, replacement is
necessary. An ohmmeter may be used to test wiring and
coil windings.
NOTE: Do not ground primary coil with ignition ON as
they may overheat or spark.
NOTE: Always disconnect spark plug lead from spark
plug before performing following tests.
NOTE:
If ignition coil(s) are disabled and an ignition
fault is registered, system will automatically
disable corresponding fuel injector drive
signal.
Fault must be corrected to ignition coil
and ECU power (switch) must be turned OFF for
10 seconds for injector signal to return. This is a
safety measure to prevent bore washing and oil
dilution.
Testing
Using an ohmmeter set on Rx1 scale, check resistance
in circuits as follows:
1. To check cylinder coil 1 (starter side), disconnect
Black connector from ECU and test between Black
pins 1 and 15. To check cylinder coil 2 (oil fi lter side),
disconnect Grey connector from ECU and test
between Grey pins 10 and 17. Wiring and coil
primary circuits are OK if readings are 0.5-0.8
2. If reading(s) are not within specifi ed range, check
and clean connections and retest.
3. If reading(s) are still not within specifi ed range, test
coils separately from main harness as follows:
a. Remove screw retaining coil to housing and
disconnect primary leads connector.
b. Connect an ohmmeter set on Rx1 scale to
primary terminals of coil. Primary resistance
should be 0.5-0.8 Ω.
c. Connect an ohmmeter set on Rx10K scale
between spark plug boot terminal and B+ primary
terminal. Secondary resistance should be 6400-
7800 Ω.
d. If secondary resistance is not within specifi ed
range, coil is faulty and needs to be replaced.