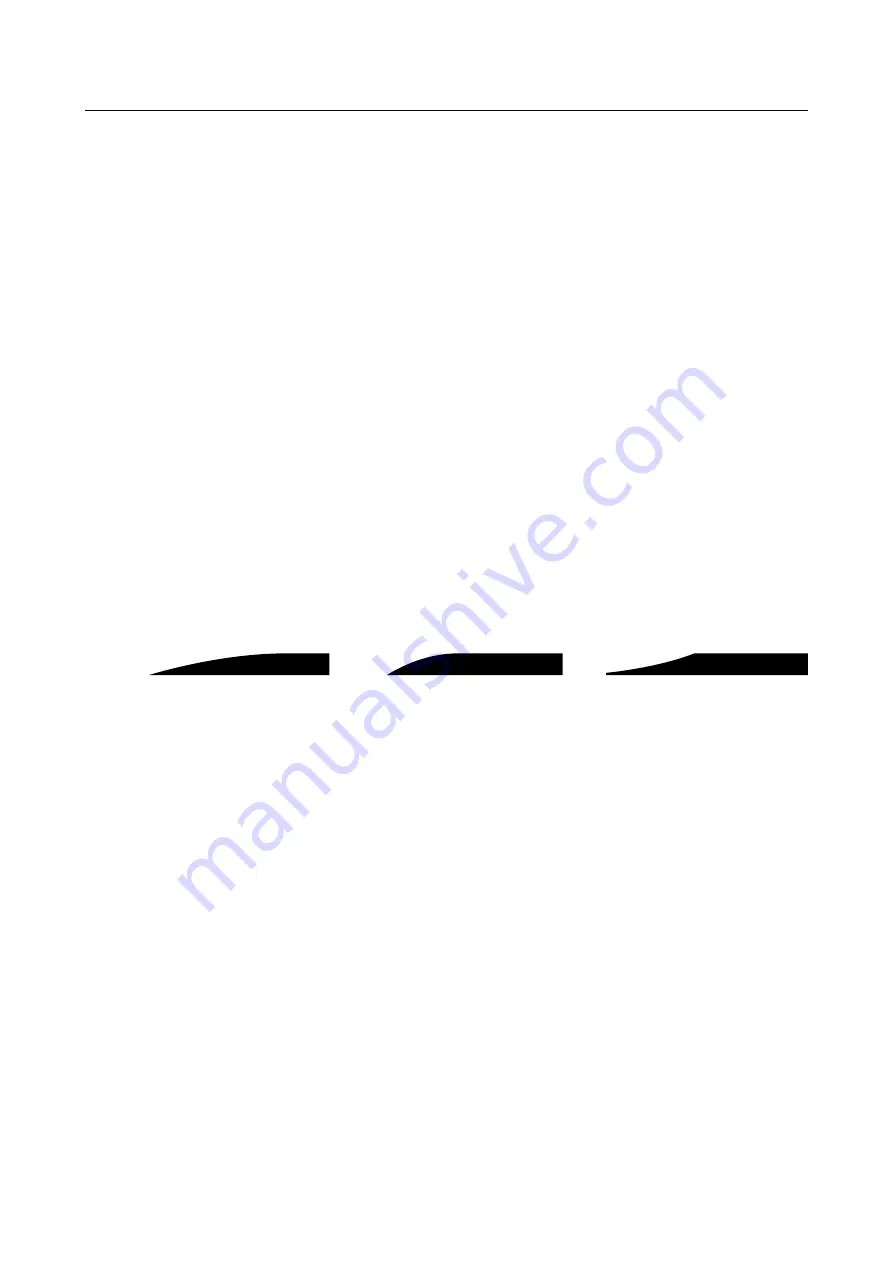
20
7.1 General principles of grinding technology
If a blade has become blunt, material must be removed from its surface to restore it to its original
sharpness.
For that, the knife in question is ground to produce its cutting edge. If, in the process, a burr
appears on the blade, then the grinding process was successful and can be concluded. Now,
before the final sharpness is achieved, the burr must be removed in a further step. This is done
with a flap brush.
As it is not only the sharp cutting edges but also the long service lives that define a blade, the
cutting angle is another important indicator of a blade's performance. The smaller the cutting
edge angle, the higher the theoretical service life. In practice, however, the cutting edge breaks
off and is therefore no longer sharp when the cutting edge angle is too small.
The cutting edge angles must therefore lie between 15° and 35°. If the cutting edge angles
are less than 15°, the blade becomes so unstable that it breaks at the slightest resistance. If the
cutting edge angle is greater than 35°, the blade is extremely stable, but service life will not be as
long.
One more criterion for judging the properties of a cutting edge is the cutting edge profile.
There are three different ground profiles:
Tapered grinding Convex grinding Concave grinding
Convex ground profiles can mostly be found on cutter blades and hand knives. Tapered and
concave ground profiles are predominantly found on circular knives and blades.
In general: Adhering to the profiles and the cutting edge angles specified by the manufacturer is
required
7. Operation