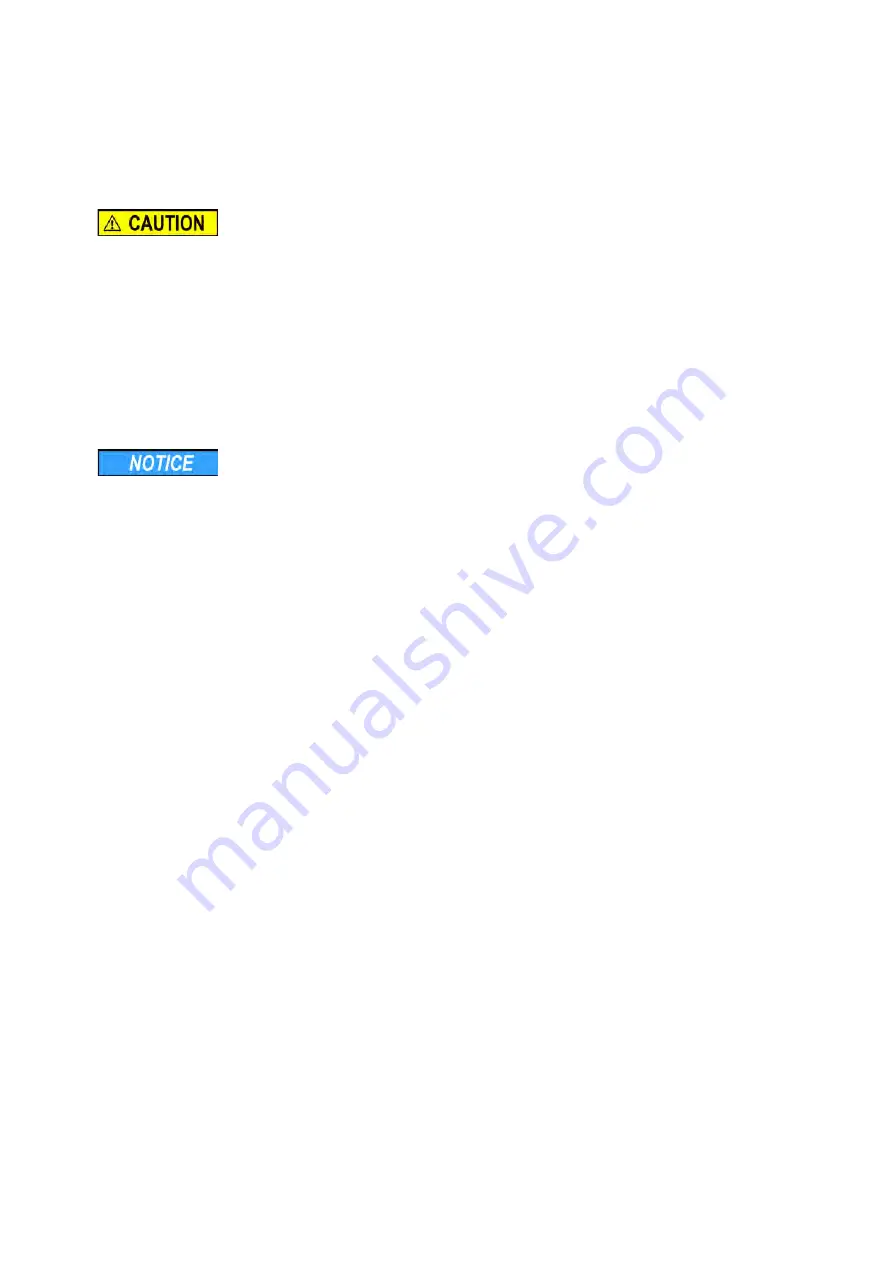
P 2.1L user manual V6840, version 3.6
Installation
7
Transport
Carefully prepare the device for transport or storage. If you want to return
your device to KNAUER for repairs, enclose the Service Request Form
which can be downloaded from our website.
Device Data
For a secure transport, note the weight and dimensions of the device (see
Technical Data).
Bruising danger
Damage to the device by carrying or lifting it on protruding housing parts.
The device may fall and thus cause injuries.
Lift the device only centrally on the side of the housing.
Lifiting
Clasp the device at its side panels and lift it out of the packaging. Do not
hold onto front cover or leak tray.
Location
Requirements
The location for the device must meet the following requirements:
Device defect
The device overheats at exposure to sunlight and insufficient air circula-
tion. Device failures are very likely.
Set up the device in such a way that it is protected against exposure to
direct sunlight.
Leave some space for air circulation: See space requirements.
Note:
The leak sensor may malfunction it the device is placed on an
inclined surface. Use a level to check that the device is in an horizontal
position.
Power Supply
The device is intended for use with AC power networks of 100 – 240 V.
Power cable
Only the supplied power cable is to be used to connect the device to the
mains supply. Replace defective power cables only with accessories from
KNAUER. Only use power cables with a permission for use from your
country.
Power plug
Make sure that the power plug on rear of the device is always accessible,
so that the device can be disconnected from the power supply.
Unpacking
Store all packing material. Retain included packing list carefully for repeat
orders.
Tool
Utility knife
position device or system on level surface
protect from heavy ventilation
Weight
19 kg
Dimensions (width
x height x depth)
361 × 201 × 523 mm
Power supply
100 – 240 V DC
Air humidity
< 90 %, non-condensing
Temperature
4 – 40 °C/39.2 – 104 °F
Содержание Azura P 2.1L
Страница 1: ...Pump P 2 1L User Manual V6840 HPLC...