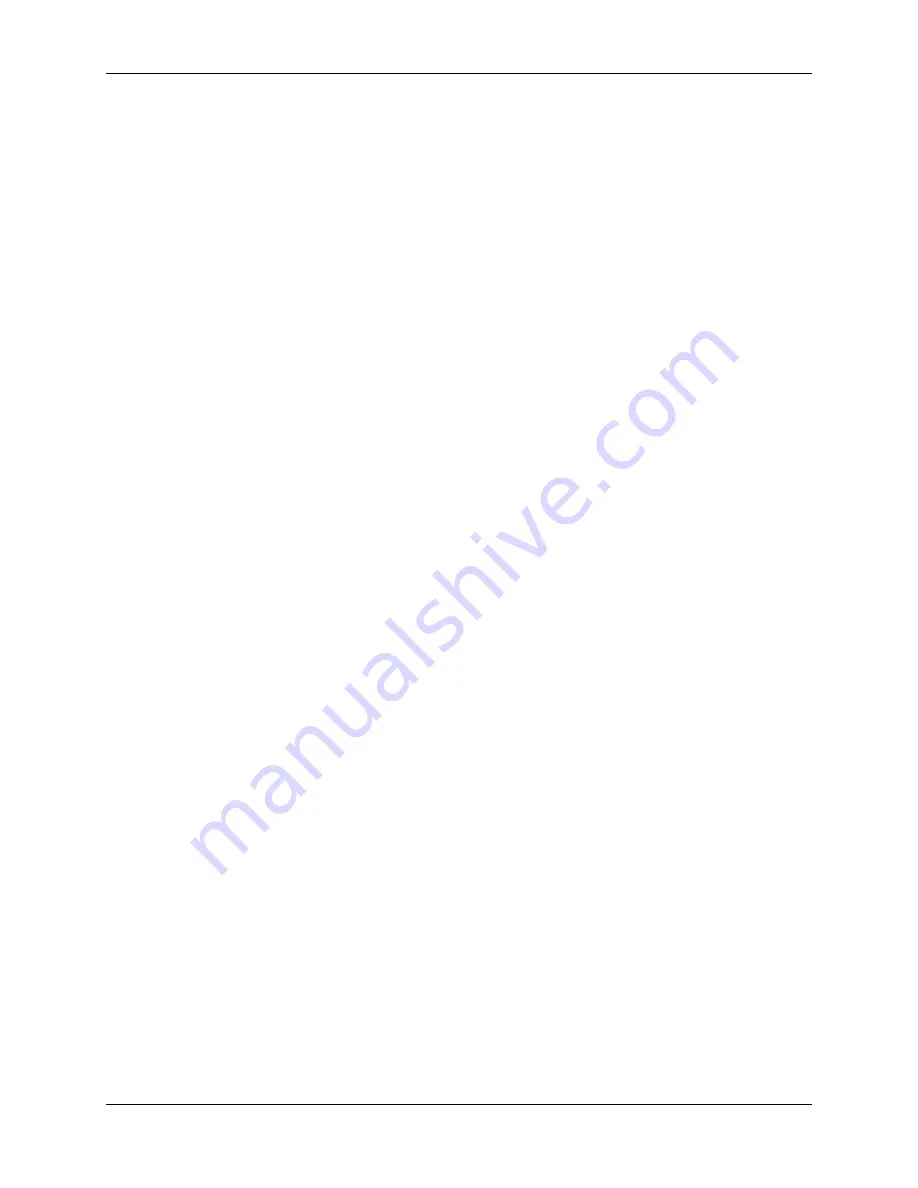
Installation
Spirit200a User’s Manual Rev J
This information is subject to the controls of the Export Administration Regulations [EAR]. This information shall not be provided to
non-U.S. persons or transferred by any means to any location outside the United States contrary to the requirements of the EAR.
3-2
Power Supply Installation
The Spirit power supply should be lifted by a forklift or pallet jack. In order
to prevent damaging the power supply, the forks should be of adequate
length to protrude on the far side of the power supply. The proper location
of the power supply will provide dependable service and reduce periodic
maintenance time. Choose a location that will provide unrestricted air
movement into and out of the power supply. Maintain
at least 24 inches
of space on
all
sides of the unit. The location should subject the power
supply to the least amount of dust, dirt, moisture, and corrosive vapors.
The surface on which the power supply is located should have a grade of
no greater than 10º to eliminate the risk of toppling over. The power
supply must be cleaned as often as necessary to prevent the
accumulation of metallic dust inside the unit. See Section 2 for power
supply dimensions.
Remote High Frequency Console Installation
The remote high frequency (RHF) console should be mounted in a
convenient location that is away from other electronic control devices.
The high voltage, high frequency signal generated inside the unit can
interfere with the operation of certain control systems. The RHF console
is usually mounted on the gantry of the cutting machine or on the cutting
table. See Section 2 for RHF console mounting dimensions.
5-Gang Manifold Installation
The 5-gang manifold assembly must be mounted within 6 feet (1.8 m) of
the torch. See Section 2 for 5-gang manifold mounting dimensions.
Torch Installation
The Spirit200a torch must be installed on the positioner of an arc voltage
control capable of maintaining the cutting arc voltage within 1 arc volt.
The arc voltage must be adjustable in 1 arc volt increments. The
positioner must be rigid to ensure cut quality and a torch collision sensor is
highly recommended. See Section 2 for torch mounting dimensions.