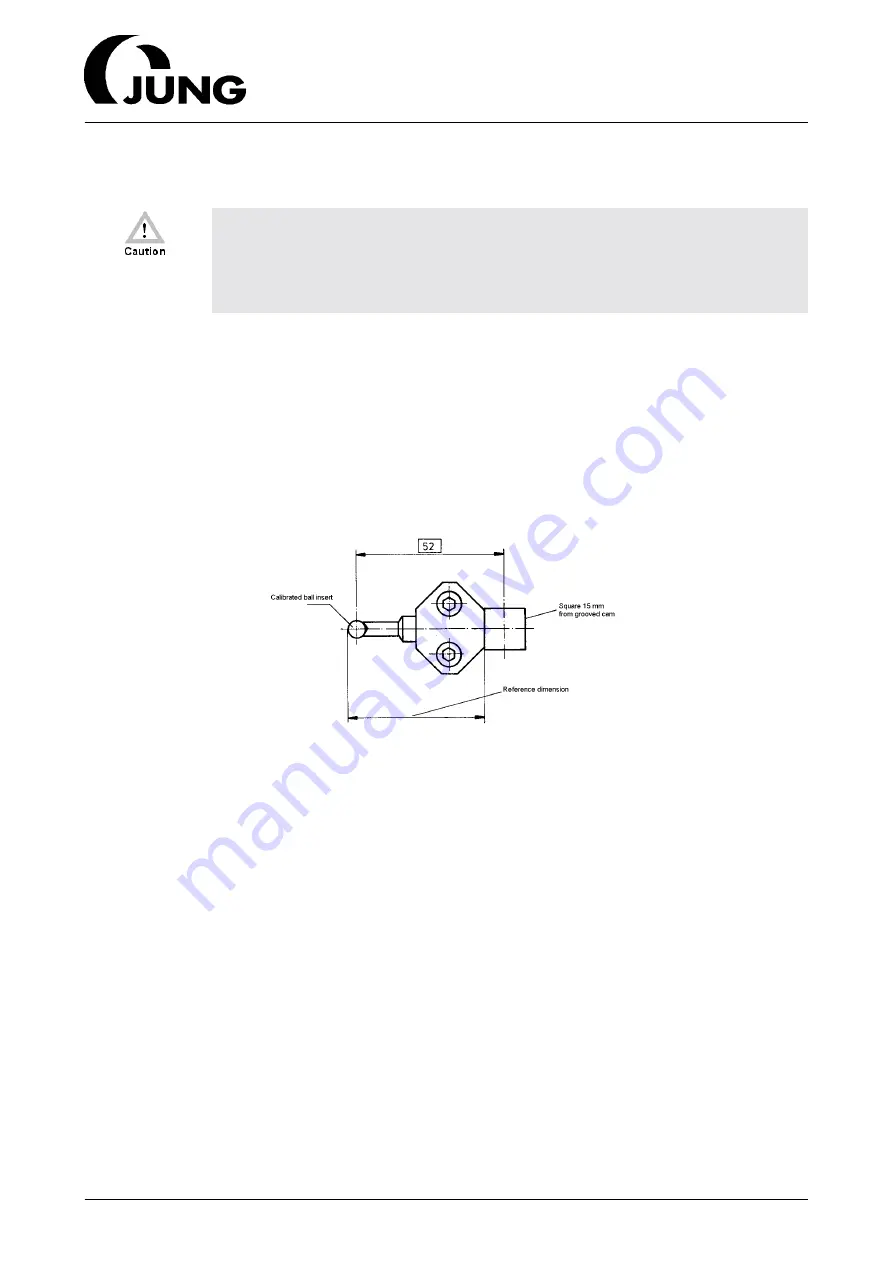
J630D
206
26.7.02
6. Dressers
6.8.2
Installation and commissioning
6.8.3
Calculating the basic dimension on the PA 31K
•
Position the turret head close to the limit positions in the U+ and W+ axes.
•
Insert the dividing head into the turret head with the single-diamond holder
mounted on it, then tighten it.
– The calibrated ball insert enclosed with the dresser has already been com-
pletely adjusted in the factory.
•
Press the "Adj. diam. NC start" softkey; the diamond swivels about the radius
midpoint in the E-axis.
•
Check this motion for deviations using a dial gauge.
•
If the gauge indicates a deviation, you must correct it by means of the single-
diamond holder.
– If it is not possible to adjust the single-diamond holder so that it is exactly
concentric, the calibrated ball insert is misaligned. You must first preset it to
the reference dimension (47.5 -0.1 - -0.2) and then adjust the length exactly.
•
Now swivel the dividing head 2 x 90° by pressing the "Diamond ch. NC start"
softkey twice.
•
Then tighten the fastening screws more firmly and repeat the measurement.
The machine is only allowed to be installed, commissioned and
connected to the mechanical components of the PA 31K by the Jung
Customer Service department. K.Jung GmbH cannot under any
circumstances accept liability for damage resulting from failure to
comply and no warranty claims will be allowed.
Содержание J630D
Страница 6: ......
Страница 7: ...Operating Instructions J630D...
Страница 8: ......
Страница 12: ......
Страница 14: ......
Страница 18: ......
Страница 20: ......
Страница 30: ......
Страница 34: ......
Страница 35: ...J630D 2 Technical data transportation commissioning 26 7 02 29 2 3 Floor space drawing...
Страница 36: ......
Страница 37: ...J630D 2 Technical data transportation commissioning 26 7 02 31 2 4 Transport dimensions machine only...
Страница 38: ......
Страница 46: ......
Страница 48: ......
Страница 56: ......
Страница 60: ......
Страница 62: ......
Страница 64: ......
Страница 66: ......
Страница 80: ......
Страница 90: ......
Страница 92: ......
Страница 94: ......
Страница 100: ......
Страница 106: ......
Страница 114: ......
Страница 130: ......
Страница 134: ......
Страница 136: ......
Страница 142: ......
Страница 144: ......
Страница 148: ......
Страница 154: ......
Страница 158: ......
Страница 160: ......
Страница 172: ......
Страница 188: ......
Страница 190: ......
Страница 198: ......
Страница 200: ......
Страница 208: ......
Страница 210: ......
Страница 218: ......
Страница 222: ......
Страница 226: ......
Страница 236: ......
Страница 244: ......
Страница 246: ......
Страница 248: ......
Страница 258: ......
Страница 262: ......
Страница 276: ......
Страница 278: ......
Страница 286: ...J630D 280 26 7 02 9 Maintenance servicing disposal 9 3 5 Lubrication instruction plate...
Страница 290: ......
Страница 291: ...J630D 9 Maintenance servicing disposal 26 7 02 285 9 4 Hydraulic plan...
Страница 295: ...J630D 9 Maintenance servicing disposal 26 7 02 289 9 5 Pneumatic plan...
Страница 296: ......
Страница 300: ......
Страница 302: ......
Страница 304: ......
Страница 310: ......
Страница 312: ......
Страница 314: ......
Страница 316: ......