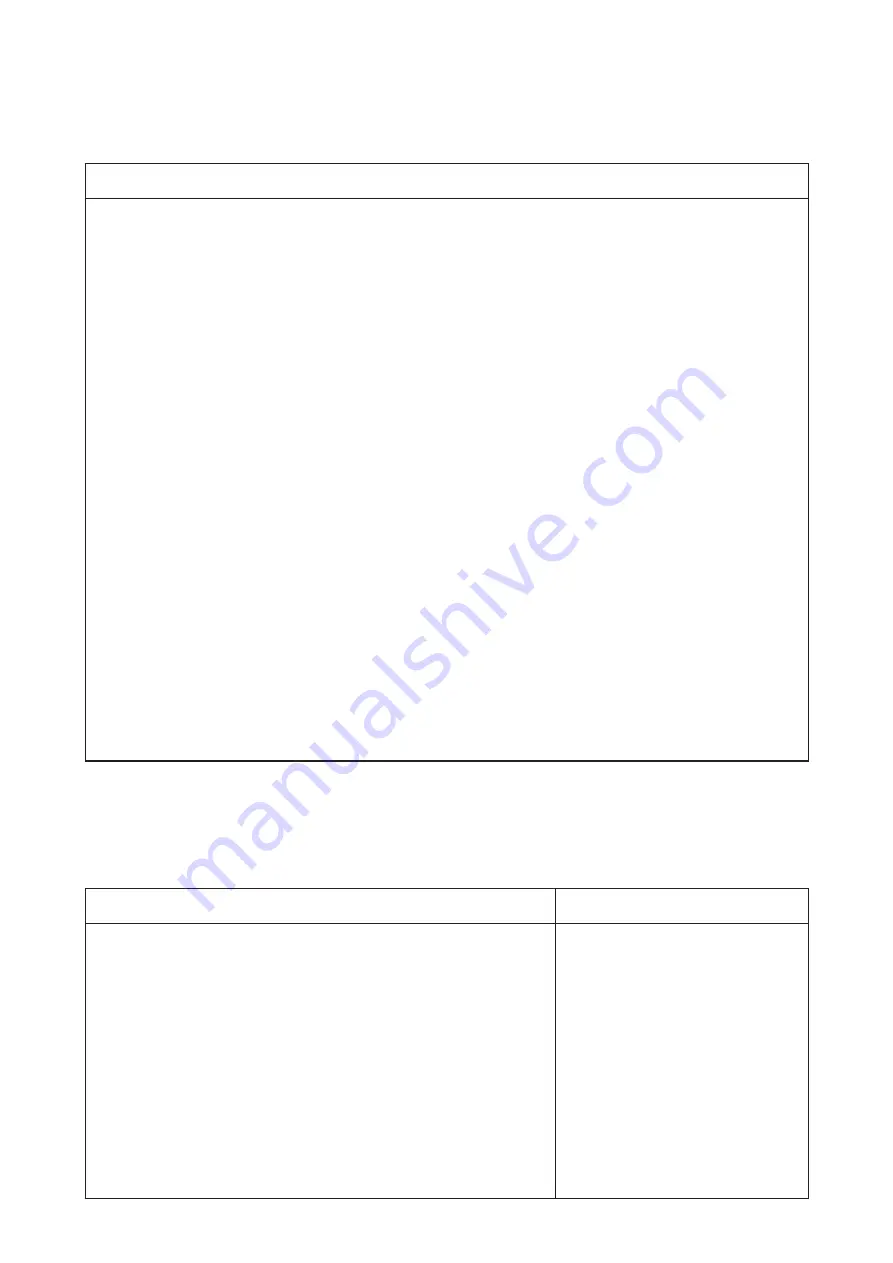
– 19 –
Procedures of assembling
1. Pass the two lubrication pipes
❻
and the oil drain pipe
❼
through the frame, and mount the shuttle
.
2. Hold the lubrication pipe
❻
with the lubrication pipe holder plate
and fix it with the setscrew
❶
.
At that time, make sure not to let the lubrication pipe
❻
come in contact with the thread trimmer connec-
tor rod.
3. Pass the lubrication pipe
❻
through the cord clamp
and fix it with the setscrew
❶
.
At that time, the needle thread clamp sensor cord
should be passed beneath the lubrication pipe
❻
and the oil drain pipe
❼
.
If the needle thread clamp sensor cord
is located above them, this can be a cause of abrasion or
cable breakage in the crosswise feed main
.
4. Using the harness band
❷
and the lubrication pipe holder
, stretch and fix the lubrication pipe
❻
along the wall side of the frame.
At that time, make sure not to permit the lubrication pipe
❻
to touch the needle thread clamp connector
link.
5. Bundle the needle thread clamp sensor cord
, the lubrication pipe
❻
, and the oil drain pipe
❼
with
the harness band
❸
.
6. Pass the two lubrication pipes
❻
through the cord clamp
and fix them with the setscrew
❶
.
7. Insert the two lubrication pipes
❻
(part B) in the oil tank
❺
. Fix the oil tank
❺
to the frame with the
setscrew
❹
.
8. Fix the oil drain pipe
❼
to the rear side by means of the cord clamp.
9. Fix the shuttle
and mount the driver
❾
. (Refer to "3.-(10) Hook adjustment".)
* Harness bands
❷
and
❸
: Part No. EA9500B0100
Adjustment procedures
Results of Improper adjustment
Bring needle bar
❶
to the lowest position of its stroke. Loosen nee-
dle bar connection screw
❷
and adjust so that upper marker line
❹
engraved on the needle bar aligns with the bottom end of needle
bar bushing lower
❸
.
(Caution) After the adjustment, make sure that there is no un
-
even torque.
* When stitch skipping occurs in accordance with the sewing con-
ditions, adjust the height of the needle bar so as to lower it by 0.5
to 1 mm from the needle bar engraved line
❹
.
Содержание LK-1900B series
Страница 128: ... 114 4 Parts to which grease is applied 1 Work clamp foot lifter area 2 Wiper area Grease JUKI Grease A Grease ...
Страница 129: ... 115 3 Thread tension area 4 Thread trimmer area Grease Grease JUKI Grease A ...
Страница 130: ... 116 5 Feed area Grease Grease D ...
Страница 131: ... 117 6 Needle bar and main shaft area 7 Lower shaft area JUKI Grease A JUKI Grease A ...
Страница 132: ... 118 8 Needle thread clamp mechanism area For LK 1900BB 1903BB Grease ...
Страница 133: ... 119 9 LK 1901B relations Grease ...
Страница 134: ... 120 10 LK 1903B relations Grease ...
Страница 135: ... 121 11 LK 1900BB 1903BB relations JUKI Grease A ...
Страница 164: ... 150 4 Power supply circuit diagram Single phase SDC board MAIN board Light blue Orange Brown Yellow Red Black ...