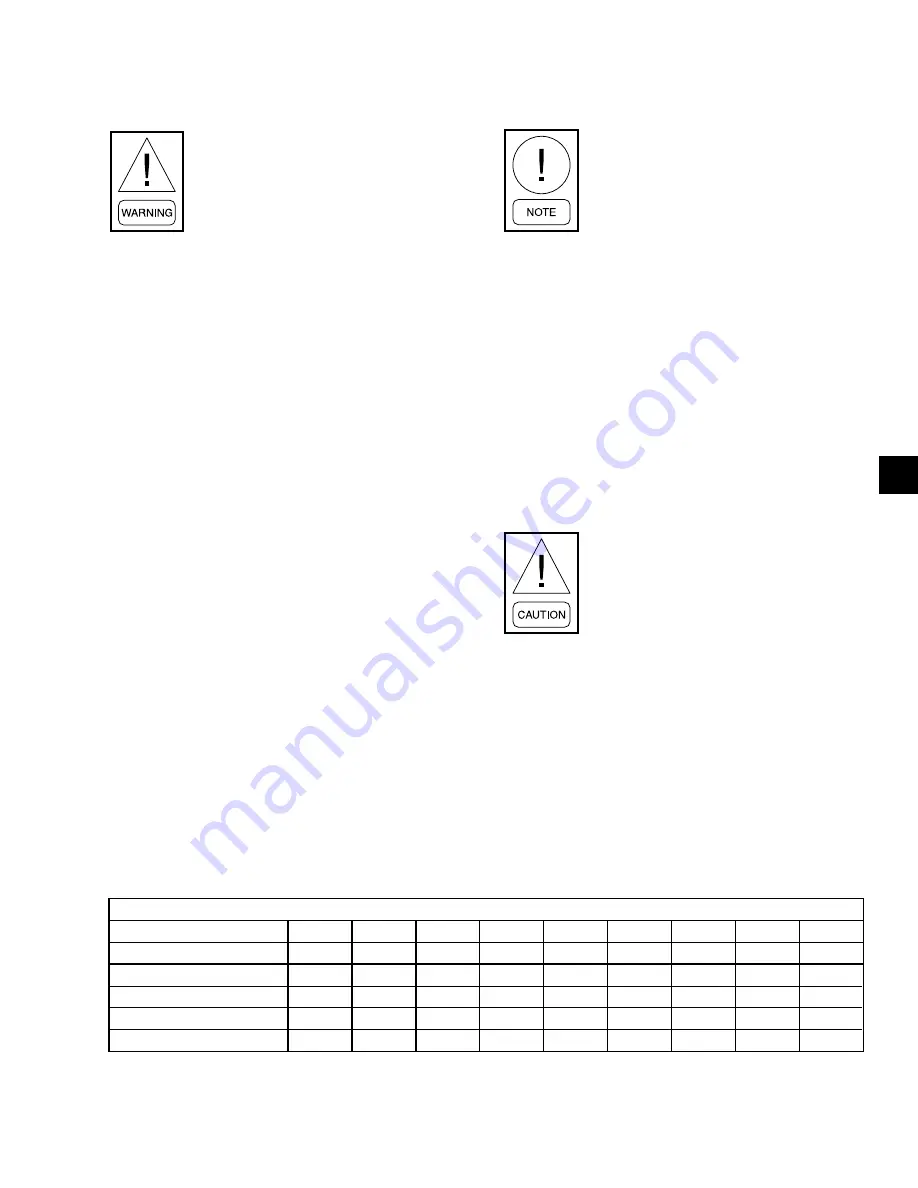
JOHNSON CONTROLS
91
SECTION 4 – MAINTENANCE
FORM 145.05-NOM7
ISSUE DATE: 10/31/2019
4
SECTION 4 – MAINTENANCE
GENERAL
A planned program of regularly scheduled maintenance
returns dividends by averting possible costly and unex-
pected periods of down time. It is the responsibility of
the owner to provide the necessary maintenance for the
air handling units and coils. If a system failure occurs
due to improper maintenance during the warranty pe-
riod, Johnson Controls is not be liable for costs incurred
to return the unit to satisfactory operation.
PERIODIC MAINTENANCE – MONTHLY
Filters
Check the cleanliness of the filters and replace or clean
as required.
Linkages
If the unit is equipped with an air side economizer ex-
amine the damper and the operator linkages to insure
that each is free and operating smoothly.
Compressors
Oil Level Check
The oil level can only be tested when the compressor
is running in stabilized conditions, to ensure that there
is no liquid refrigerant in the lower shell of the com-
pressor. When the compressor is running in stabilized
conditions, the oil level must be between 1/4 and 3/4 in
the oil sight glass. At shutdown, the oil level can fall to
the bottom limit of the oil sight glass.
Make sure power is removed from the unit
before performing the maintenance items
contained in this section.
Not all compressors come with an oil
sight glass. Most compressors use an oil
level port located a few inches up from
the bottom.
Oil Analysis
Use YORK Type "V" POE oil (clear) for units charged
with R-410A refrigerant. The type of refrigerant and
amount per system is listed in
and on the unit rating plate. A change in oil
color or odor may be an indication of contaminates
in the refrigerant system. If this occurs, an oil sample
should be taken and analyzed. If contaminates are pres-
ent, the system must be cleaned to prevent compressor
failure. This can be accomplished through the installa-
tion of oversized suction and liquid line driers. The dri-
ers may have to be changed several times to clean up
the system depending on the degree of contamination.
Fan Bearing Lubrication
Add grease slowly with shaft rotating until a slight bead
forms at the seals. If necessary, re-lubricate while bearing
is stationary. Refer to
for lubricat-
ing schedule. The lubrication schedule is the maximum
amount of time allowed between component mainte-
nance and lubrication. Depending on operation and site
conditions, shorten the schedule time between mainte-
nance and lubrication. Re-lubrication is generally ac-
companied by a temporary rise in operating tempera-
ture. Excess grease is purged from the seals.
Never use the scroll compressor to pump
the refrigerant system down into a vac-
uum. Internal arcing of the compressor
motor occurs, which results in failure of
compressor.
TABLE 14 -
FAN BEARING – LUBRICATION INTERVALS
RELUBRICATION SCHEDULE (MONTHS) BALL BEARING PILLOW BLOCKS
SPEED (RPM)
500
1000
1500
2000
2500
3000
3500
4000
4500
SHAFT DIA
1/2 in. thru 1-11/16 in.
6
6
5
3
3
2
2
2
1
1-15/16 in. thru 2-7/16 in.
6
5
4
2
2
1
1/2
1/4
1/4
2-11/16 in. thru 2-15/16 in.
5
4
3
2
1
1/2
1/2
3-7/16 in. thru 4 in.
4
3
2
1
1/2
1/2