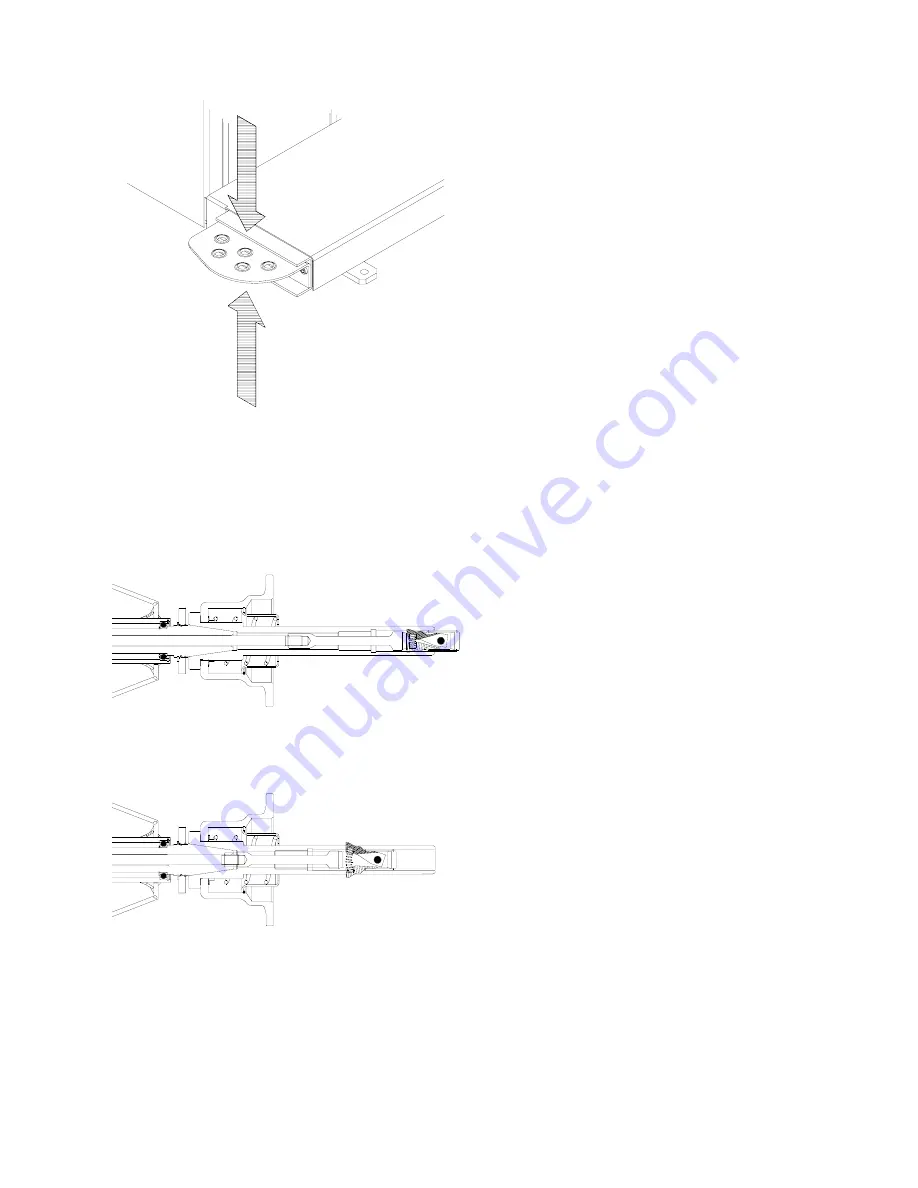
Page 15
Figure 13
Figure 14
Figure 15
5.0 POWER CLAMP
5.1 POWER CLAMP PEDAL
Shaft Lock
The main shaft is locked when the pedal is
depressed.
This holds the wheel in the correction position for correct
fitting of the correction weights. See Figure 13.
This lock is designed only to facilitate orientation of the
wheel and must not be used for braking the main shaft.
Power Clamp Operation.
Lift upward to engage the power clamp jaws when the
lock nut is placed on the shaft.
Lift upward again to release the clamp nut.
NOTE:
The first time the unit is operated after power-
up, make sure the power clamp engaging jaws are in
the outer most position and ready for use. An Error of
“E14”
may result if the unit cannot accurately determine
the clamping jaw position. Simple press “ESC” to
continue, lift the pedal again to cycle and the power
clamp will learn its new position. See Figures 14 and
15.
Push down for brake
Lift up for power clamp operation
Power Clamp with jaws all the way OUT
Power Clamp with jaws all the way IN
Содержание BFH 1000
Страница 2: ...Blank page ...
Страница 6: ......
Страница 14: ...Page 8 Figure 5a Complete Function Menu listing ...
Страница 44: ...NOTES ...
Страница 45: ...NOTES ...