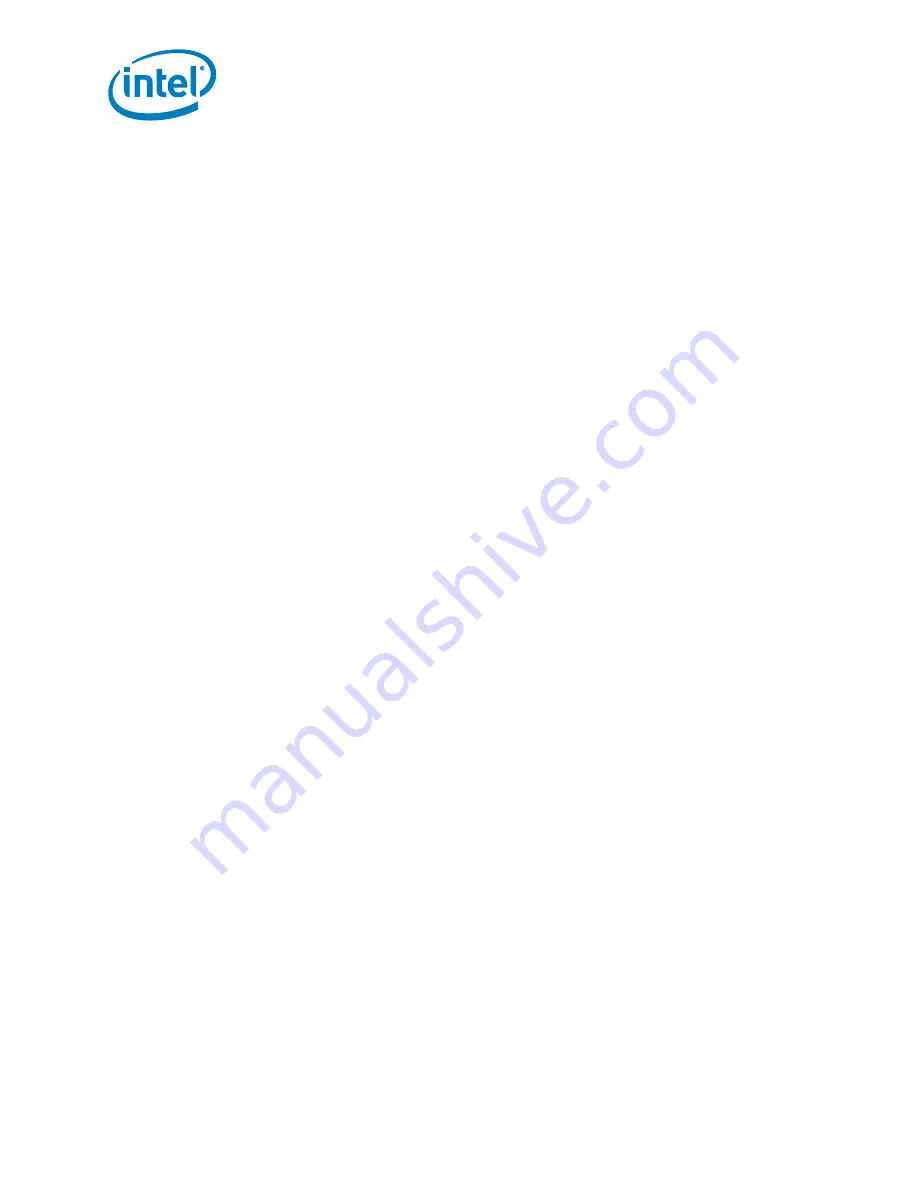
Sensor Based Thermal Specification Design Guidance
58
Thermal/Mechanical Specifications and Design Guidelines
7.3.2
Thermal Design and Modelling
Based on the boundary conditions the designer can now make the design selection of
the thermal solution components. The major components that can be mixed are the
fan, fin geometry, heat pipe or air duct design. There are cost and acoustic trade-offs
the customer can make.
7.3.3
Thermal Solution Validation
7.3.3.1
Test for Compliance with the TTV Thermal Profile
This step is the same as previously suggested for prior products. The thermal solution
is mounted on a test fixture with the TTV and tested at the following conditions:
• TTV is powered to the TDP condition
• Maximum airflow through heatsink
• T
AMBIENT
at the boundary condition from
The following data is collected: TTV power, TTV T
CASE
, and T
AMBIENT
. This is used to
calculate
Ψ
CA
which is defined as:
Ψ
CA
= (TTV T
CASE
– T
AMBIENT
) / Power
This testing is best conducted on a bench to eliminate as many variables as possible
when assessing the thermal solution performance. The boundary condition analysis as
described in
should help in making the bench test simpler to perform.
7.3.3.2
Thermal Solution Characterization for Fan Speed Control
The final step in thermal solution validation is to establish the thermal solution
performance,
Ψ
CA
and acoustics as a function of fan speed. This data is necessary to
allow the fan speed control algorithm developer to program the device. It also is
needed to asses the expected acoustic impact of the processor thermal solution in the
system.
The fan speed control device may modulate the thermal solution fan speed (RPM) by
one of two methods. The first and preferred is pulse width modulation (PWM) signal
compliant with the 4-Wire Pulse Width Modulation (PWM) Controlled Fans specification.
the alternative is varying the input voltage to the fan. As a result the characterization
data needs to also correlate the RPM to PWM or voltage to the thermal solution fan. The
fan speed algorithm developer needs to associate the output command from the fan
speed control device with the required thermal solution performance. Regardless of
which control method is used, the term RPM will be used to indicate required fan speed
in the rest of this document.
7.4
Fan Speed Control (FSC) design process
The next step is to incorporate the thermal solution characterization data into the
algorithms for the device controlling the fans.
As a reminder, the requirements are:
• When the DTS value is at or below T
CONTROL
, the fans can be slowed down — just
as with prior processors.
Содержание BX80605X3440 - Quad Core Xeon X3440
Страница 10: ...Introduction 12 Thermal Mechanical Specifications and Design Guidelines...
Страница 26: ...LGA1156 Socket 28 Thermal Mechanical Specifications and Design Guidelines...
Страница 78: ...Component Suppliers 78...
Страница 80: ...Mechanical Drawings 80 Figure B 1 Socket Heatsink ILM Keepout Zone Primary Side for 1U Top...
Страница 81: ...81 Mechanical Drawings Figure B 2 Socket Heatsink ILM Keepout Zone Secondary Side for 1U Bottom...
Страница 87: ...87 Mechanical Drawings Figure B 8 Heatsink Compression Spring...
Страница 88: ...Mechanical Drawings 88 Figure B 9 Heatsink Load Cup...
Страница 89: ...89 Mechanical Drawings Figure B 10 Heatsink Retaining Ring...
Страница 91: ...91 Mechanical Drawings Figure B 12 Heatsink Backplate...
Страница 92: ...Mechanical Drawings 92 Figure B 13 Heatsink Backplate Insulator...
Страница 102: ...Socket Mechanical Drawings 104 Thermal Mechanical Specifications and Design Guidelines...
Страница 106: ...Package Mechanical Drawings 108 Thermal Mechanical Specifications and Design Guidelines...