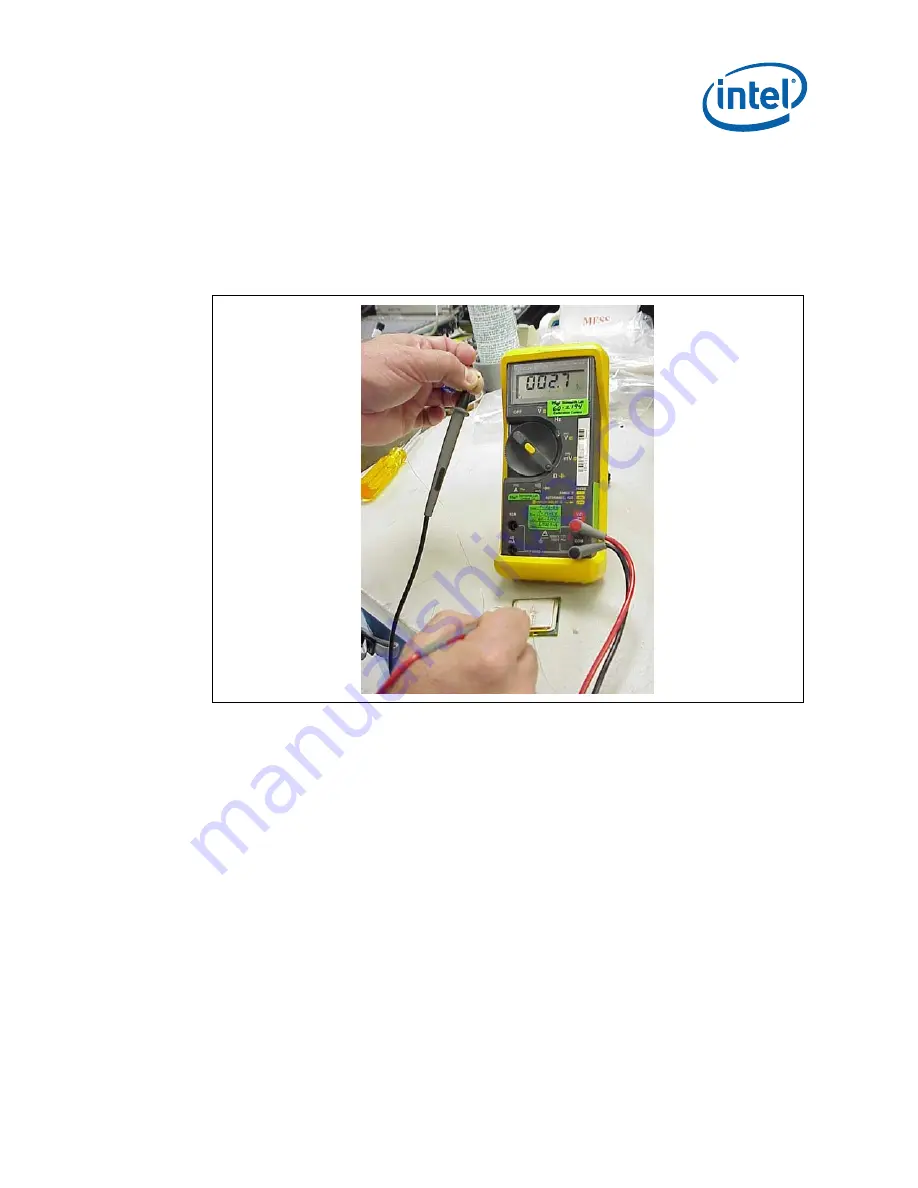
Case Temperature Reference Metrology
Thermal and Mechanical Design Guidelines
95
12.
Place a 3
rd
piece of tape at the end of the step in the groove as shown in
7-22. This tape will create a solder dam to prevent solder from flowing into
the larger IHS groove section during the melting process.
13.
Measure resistance from thermocouple end wires (hold both wires to a DMM
probe) to the IHS surface. This should be the same value as measured during the
thermocouple conditioning Section
Figure
7-23. Measuring Resistance between Thermocouple and IHS
14.
Using a fine point device, place a small amount of flux on the thermocouple bead.
Be careful not to move the thermocouple bead during this step (Figure
Ensure the flux remains in the bead area only.
Содержание BX80570E8200 - Core 2 Duo 2.66 GHz Processor
Страница 10: ...10 Thermal and Mechanical Design Guidelines...
Страница 26: ...Processor Thermal Mechanical Information 26 Thermal and Mechanical Design Guidelines...
Страница 82: ...Heatsink Clip Load Metrology 82 Thermal and Mechanical Design Guidelines...
Страница 84: ...Thermal Interface Management 84 Thermal and Mechanical Design Guidelines...
Страница 108: ...Balanced Technology Extended BTX System Thermal Considerations 108 Thermal and Mechanical Design Guidelines...
Страница 110: ...Fan Performance for Reference Design 110 Thermal and Mechanical Design Guidelines...
Страница 122: ...Mechanical Drawings 122 Thermal and Mechanical Design Guidelines Figure 7 50 Reference Fastener Sheet 1...
Страница 123: ...Mechanical Drawings Thermal and Mechanical Design Guidelines 123 Figure 7 51 Reference Fastener Sheet 2...
Страница 124: ...Mechanical Drawings 124 Thermal and Mechanical Design Guidelines Figure 7 52 Reference Fastener Sheet 3...
Страница 125: ...Mechanical Drawings Thermal and Mechanical Design Guidelines 125 Figure 7 53 Reference Fastener Sheet 4...