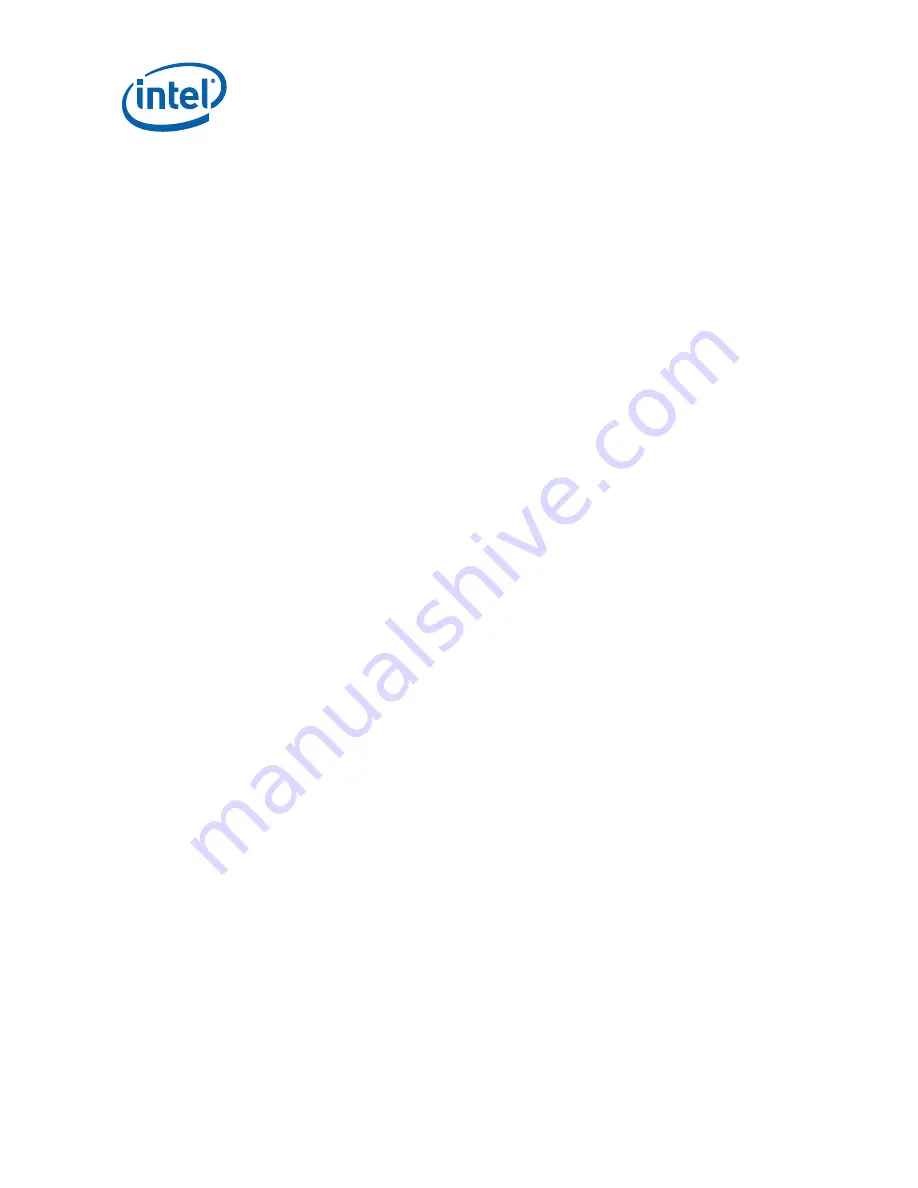
Thermal Management Logic and Thermal Monitor Feature
34
Thermal and Mechanical Design Guidelines
4.2.1
PROCHOT# Signal
The primary function of the PROCHOT# signal is to provide an external indication that
the processor has reached the TCC activation temperature. While PROCHOT# is
asserted, the TCC will be activated. Assertion of the PROCHOT# signal is independent
of any register settings within the processor. It is asserted any time the processor die
temperature reaches the trip point.
PROCHOT# can be configured using BIOS as an output or bi-directional signal. As an
output, PROCHOT# will go active when the processor temperature of either core
reaches the TCC activation temperature. As an input, assertion of PROCHOT# will
activate the TCC for both cores. The TCC will remain active until the system de-
asserts PROCHOT#
The temperature at which the PROCHOT# signal goes active is individually calibrated
during manufacturing. Once configured, the processor temperature at which the
PROCHOT# signal is asserted is not re-configurable.
One application of the Bi-directional PROCHOT# is for the thermal protection of
voltage regulators (VR). System designers can implement a circuit to monitor the VR
temperature and activate the TCC when the temperature limit of the VR is reached. By
asserting PROCHOT# (pulled-low) which activates the TCC, the VR can cool down as a
result of reduced processor power consumption. Bi-directional PROCHOT# can allow
VR thermal designs to target maximum sustained current instead of maximum
current. Systems should still provide proper cooling for the VR, and rely on bi-
directional PROCHOT# signal only as a backup in case of system cooling failure.
Note:
A thermal solution designed to meet the thermal profile specifications should rarely
experience activation of the TCC as indicated by the PROCHOT# signal going active.
4.2.2
Thermal Control Circuit
The Thermal Control Circuit portion of the Thermal Monitor must be enabled for the
processor to operate within specifications. The Thermal Monitor’s TCC, when active,
will attempt to lower the processor temperature by reducing the processor power
consumption. There are two methods by which TCC can reduce processor power
dissipation. These methods are referred to as Thermal Monitor 1 (TM1) and Thermal
Monitor 2 (TM2).
4.2.2.1
Thermal Monitor
In the original implementation of thermal monitor this is done by changing the duty
cycle of the internal processor clocks, resulting in a lower effective frequency. When
active, the TCC turns the processor clocks off and then back on with a predetermined
duty cycle. The duty cycle is processor specific, and is fixed for a particular processor.
The maximum time period the clocks are disabled is ~3
s. This time period is
frequency dependent and higher frequency processors will disable the internal clocks
for a shorter time period. Figure
4-1 illustrates the relationship between the internal
processor clocks and PROCHOT#.
Performance counter registers, status bits in model specific registers (MSRs), and the
PROCHOT# output pin are available to monitor the Thermal Monitor behavior.
Содержание BX80570E8200 - Core 2 Duo 2.66 GHz Processor
Страница 10: ...10 Thermal and Mechanical Design Guidelines...
Страница 26: ...Processor Thermal Mechanical Information 26 Thermal and Mechanical Design Guidelines...
Страница 82: ...Heatsink Clip Load Metrology 82 Thermal and Mechanical Design Guidelines...
Страница 84: ...Thermal Interface Management 84 Thermal and Mechanical Design Guidelines...
Страница 108: ...Balanced Technology Extended BTX System Thermal Considerations 108 Thermal and Mechanical Design Guidelines...
Страница 110: ...Fan Performance for Reference Design 110 Thermal and Mechanical Design Guidelines...
Страница 122: ...Mechanical Drawings 122 Thermal and Mechanical Design Guidelines Figure 7 50 Reference Fastener Sheet 1...
Страница 123: ...Mechanical Drawings Thermal and Mechanical Design Guidelines 123 Figure 7 51 Reference Fastener Sheet 2...
Страница 124: ...Mechanical Drawings 124 Thermal and Mechanical Design Guidelines Figure 7 52 Reference Fastener Sheet 3...
Страница 125: ...Mechanical Drawings Thermal and Mechanical Design Guidelines 125 Figure 7 53 Reference Fastener Sheet 4...