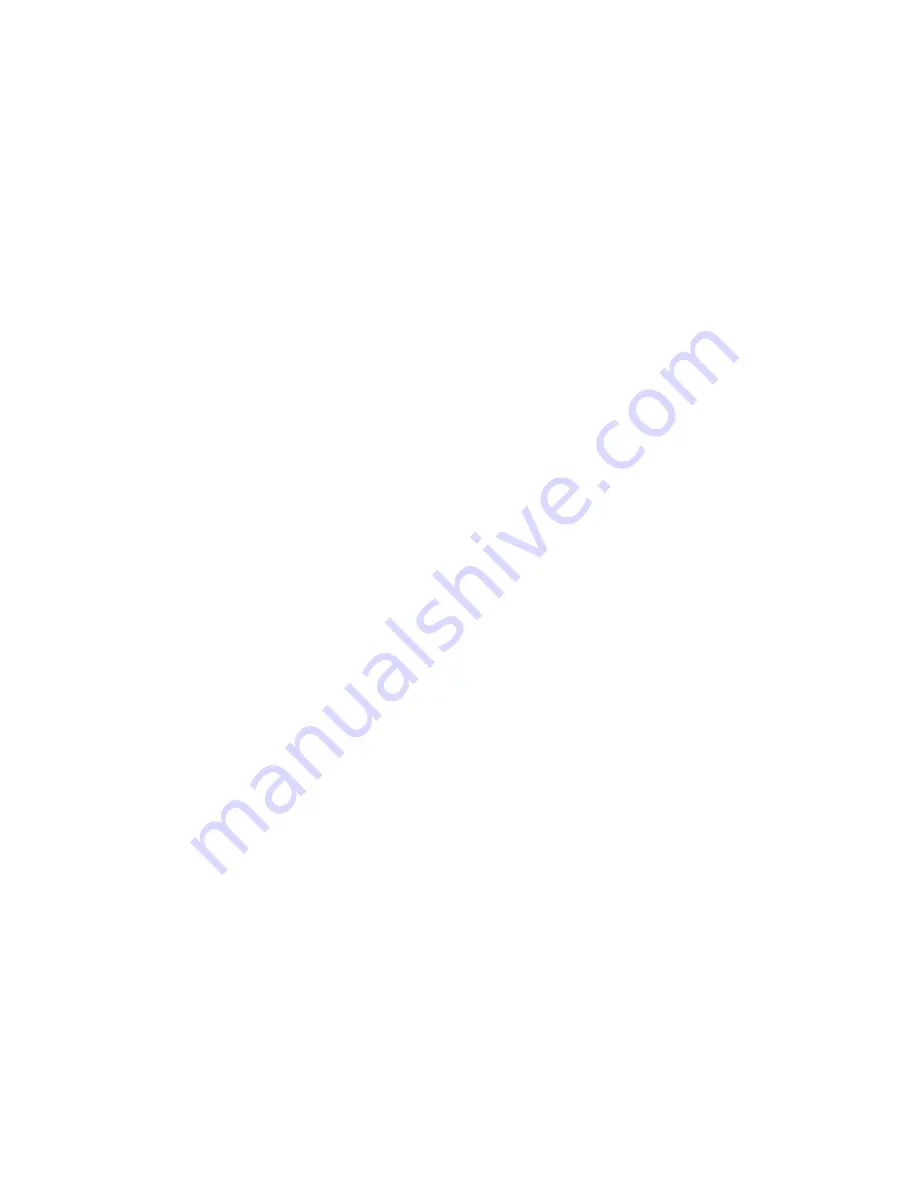
- 9 -
SECTION 3
!
OPERATION
3.1 START UP
Typically, the instruments come from the factory set up for a 10 to 1 flow rate span, with the trip level
set approximately at 10% of the full scale value. SECTION 6 details the instrument specifications.
Following installation all that is required is to switch on power and initiate flow in the measurable flow
rate range. The following figures and tables show how to configure the Model 400 alarm setpoint(s),
high/low alarming, and time response. Liquid meters that are not calibrated directly on the liquid to be
measured are so indicated in this manual (SECTION 6) and require an in-line field calibration.
When power is first turned on, the output reading or signal will indicate full scale. After ten to forty-five
seconds (depending on flow range adjustment) the reading will stabilize. The instrument time constant
is generally between 4 to 12 seconds. Higher average flow rates will result in an observed faster
response time for a given unit.
3.2 FIELD ADJUSTMENT INSTRUCTIONS
The flow switch/monitor may initially indicate a high flow rate even for zero flow when power is first
applied to the unit. Correct indication of flow or level will result after an initial period which can extend
to about forty seconds depending on where the level adjust is set. Apply power only after reading and
adhering to instructions in
SECTION 2
of this manual.
3.2.1
Adjustment of the ALARM1 flow switch setpoint (all Model 400 types)
A.
Establish a flow rate at the desired trip level. This should be done with flow in the line, not
at zero flow. Set the alarm switch, S1, to “
LO
” if alarming at a rate below this flow value is
desired; set it to “
HI
” if alarming at a rate above this flow value is desired. An example would
be to use 50% of your lowest normal flow rate as the set point and setting S1 to “
LO
.”
B.
If the LED is
green
, adjust “
Trip 1
" potentiometer clockwise* until the relay de-energizes
(LED turns
red
). This is the alarm condition.
C.
If the LED is
red
, adjust “
Trip 1
" potentiometer slowly counter clockwise* until the relay
energizes (LED turns
green
).
D.
If the relay cannot be made to drop out over the full range of the “
Trip 1
" potentiometer, see
Table III.
*Reverse direction of turns if S1 is set to “
HI
” position.
3.2.2
Adjustment of the ALARM2 flow trip setpoint (when S2 option is ordered)
The ALARM2 flow switch is energized at flows below the trip level and does not have an LED to
indicate alarm state. The relay contacts must be monitored to determine the relay state (refer to Table
II). If one relay is to be used for high flow alarm and one relay for low flow alarm, RELAY1 should be
used as the “lo” alarm and RELAY2 used as the “hi” alarm.