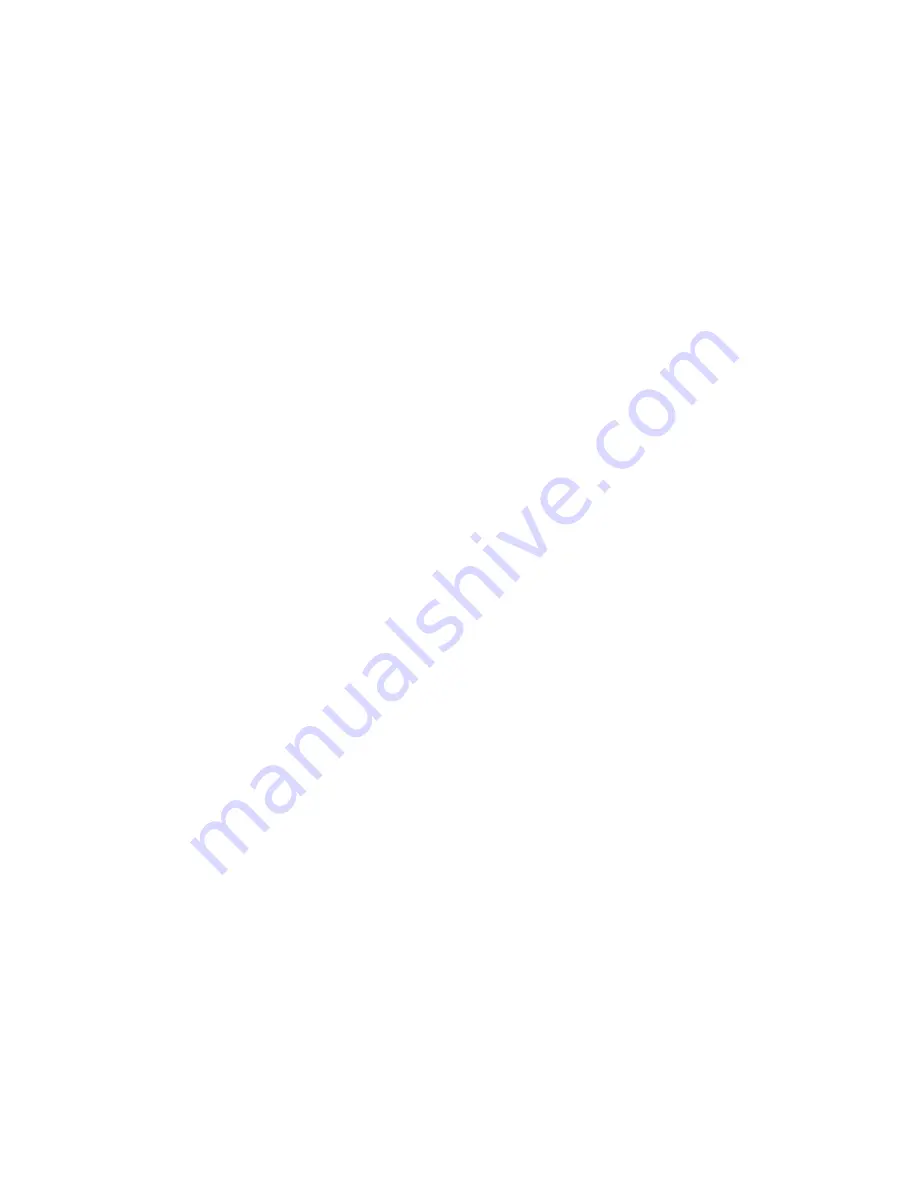
- 14 -
SECTION 4
!
MAINTENANCE
4.1 GENERAL MAINTENANCE
Certain precautions should be taken to insure proper performance of all models of flow instruments.
Since the measurement technique involves a signal resulting from heat transfer to the flowing medium,
care should be exercised to prevent build-up of varying layers on the walls of the transducer. Layers
such as bacterial growth, dried paints, gas bubbles and non-solubles can result in measurement below
actual flow rates. Periodic checks and cleaning should be performed to insure a clean pipe or probe
surface.
It should be part of normal maintenance procedure to check the system for proper functioning.
Experience and other observable conditions should be utilized to determine the frequency of inspection.
To test the flow switch action, the flow rate should be reduced below (for low flow switch) or raised
above (for high flow switch) the switching level. When the unit reaches alarm mode (de-energized relay,
LED is
red
), check and insure relay action and continuity of the shut down or warning circuits which it
operates.
The joints of all intrusive probes tips should be inspected for wear and corrosion.
4.2 FIELD CALIBRATION
If the unit was purchased with a 4-20mA output, and calibrated at the factory or by the customer, a field
recalibration can be performed as follows:
1.
Establish a known flow rate near 10-15% of the desired full scale value. Monitor the flow
output for stability.
2.
Locate the zero potentiometer (pot) labeled P3 using Figure 3. Identify the proper flow output
signal corresponding to the current flow rate (see Figure 6 or the supplied calibration curve,
as applicable). After the flow has stabilized. adjust P3 until the flow output agrees with the
desired output value.
3.
Establish a known flow rate near 95-100% of the desired full scale. Monitor the flow output
for stability.
4.
Locate the span pot labeled P4 using Figure 3. Identify the proper flow output signal
corresponding to the current flow rate (see Figure 6 or the supplied calibration curve, as
applicable). After the flow has stabilized, adjust P4 until the flow output agrees with the
desired output value.
5.
Since potentiometers P3 and P4 are slightly affected by the adjustment of the other, repeat
steps 1 through 4 until the desired accuracy level is achieved.