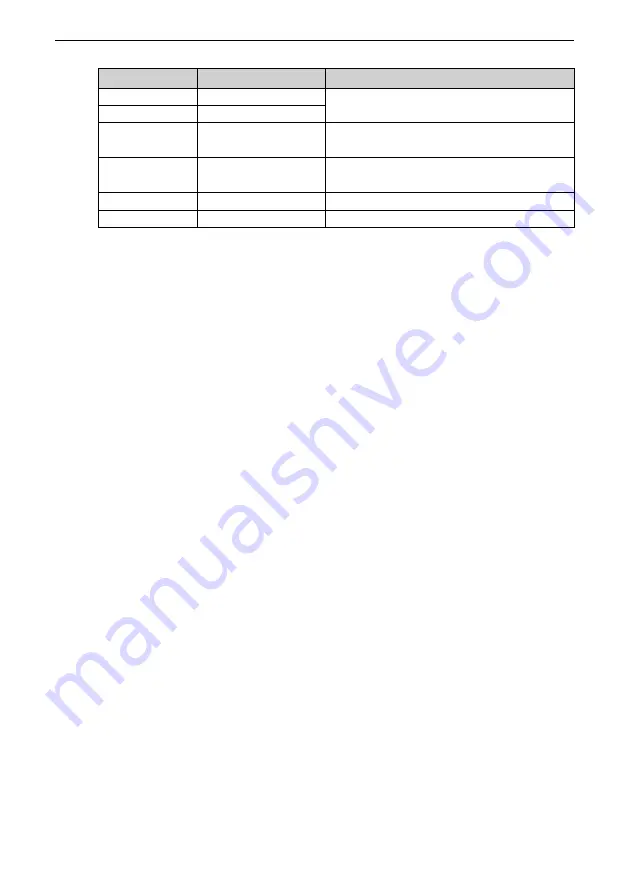
‑
82
‑
Pin No.
Assignment
Description
4
RS485+
RS485 communication port
5
RS485‑
6
RS232‑TXD
RS232 transmitting end, connected to the
receiving end of the host controller
7
RS232‑RXD
RS232 receiving end, connected to the
transmitting end of the host controller
8
GND
Ground
Enclosure
PE
Shield
3.5
Connecting the Power supply (RST)
3.5.1 Wiring Precautions
●
Do not connect the input power supply cables to the output terminals U, V, and W.
Failure to comply will damage the servo drive.
●
When cables are bundled in a duct, the cooling effect will be deteriorated. In this
case, take the permissible current reduction ratio into account.
●
When the temperature inside the cabinet exceeds the temperature limit of the
cable, it is recommended to replace with Teflon cables featuring a higher
temperature limit. As the surface of regular cables may be easily hardened and
cracked under a low temperature, take thermal insulation measures for cables laid
in a low‑temperature environment.
●
The bending radius of a cable must be 10 times more than its outer diameter to
prevent the internal conductor from breaking due to long‑time bending.
●
Do not bundle power cables and signal cables together or route them through the
same duct. Power cables and signal cables must be separated by at least 30 cm to
prevent interference.
●
High voltage may be still present in the servo drive after the power supply is
switched off. Do not touch the power supply terminals within 15 minutes after
power‑off.
●
Do not switch on/off the power supply frequently. If the power supply is switched
on or off frequently within 1s, Er.740/Er.136/Er.430 may occur (see Chapter
"Troubleshooting" in SV660P Series Servo Drive Commissioning Guide for details).
In this case, power on the servo drive again after waiting for the specified ON/OFF
interval. If frequent ON/OFF control is needed, keep an ON/OFF interval of at least
1 min.
The servo drive carries a capacitor in the power supply part, and this capacitor will
be charged with a high current for 0.2s upon power‑on. Turning on/off the power
supply frequently degrades the performance of main circuit components inside
the servo drive.
Содержание SV660P Series
Страница 1: ...SV660P Series Servo Drive Hardware Guide Data code 19011391 A00...
Страница 55: ...Installation 54 Figure 2 21 Installing the ferrite clamp...
Страница 66: ...Wiring 65 3 3 2 Wiring Diagram for Torque Control Mode Figure 3 5 Wiring in the torque control mode...
Страница 111: ...Wiring 110 Open collector mode For use of the internal 24 V power supply of the servo drive...
Страница 113: ...Wiring 112 Scheme 2 Using the external resistor...
Страница 135: ...Wiring 134 Selecting the regenerative resistor Figure 3 48 Flowchart for selecting the regenerative resistor...
Страница 144: ...Maintenance 143...