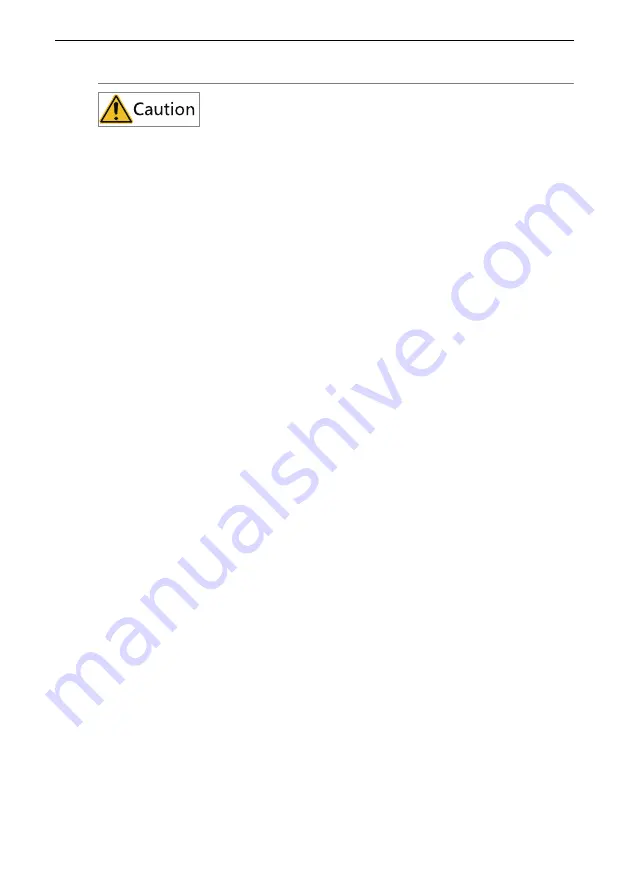
‑
56
‑
●
The specification and installation of external cables must comply with applicable
local regulations.
●
Observe the following requirements when the servo drive is used on a vertical axis.
—
—
Set the safety device properly to prevent the workpiece from falling upon
warning or overtravel.
—
—
Ensure the positive/negative polarity of the 24 V power supply is correct.
Otherwise, the axis may fall and cause personal injury or equipment damage.
●
Observe the following requirements during wiring of the power supply and main
circuit:
—
—
When the main circuit terminal is a connector, remove the connector from the
servo drive before wiring.
—
—
Insert one cable into one cable terminal of the connector. Do not insert
multiple cables into one cable terminal.
—
—
When inserting cables, take enough care to prevent the cable conductor burrs
from being short circuited to the neighboring cable.
—
—
Insulate the connecting part of the power supply terminals to prevent electric
shock.
—
—
Do not connect a 220 V servo drive to a 380 V power supply directly.
—
—
Install safety devices such as a circuit breaker to prevent short circuit in
external circuits. Failure to comply may result in a fire.
—
—
Cut off the main circuit power supply and switch off the S‑ON signal after an
alarm signal is detected.
●
Connect the servo drive to the motor directly. Do not use an electromagnetic
contactor during wiring. Failure to comply may result in equipment fault.
●
Do not put heavy objects onto cables or pull cables with excessive force. Failure to
comply may result in cable damage, leading to an electric shock.
●
When connecting DO terminals to relays, ensure the polarity of the flywheel diode
is correct. Wrong polarity will result in equipment damage or signal output failure.
●
Keep a distance of at least 30 cm between main circuit cables and I/O signal
cables/encoder cables. Failure to comply may result in equipment malfunction.
●
Use twisted pairs or multi‑conductor shielded twisted pairs as the I/O signal cable
or encoder cable. Failure to comply may result in equipment malfunction.
●
The maximum wiring lengths of the I/O signal cable and the encoder cable are 3 m
and 20 m respectively.
●
Use a power supply filter to reduce the electromagnetic interference on electronic
devices surrounding the servo drive.
●
Take proper shielding measures in the following locations to prevent equipment
damage:
—
—
Locations with interference caused by static electricity
Содержание SV660P Series
Страница 1: ...SV660P Series Servo Drive Hardware Guide Data code 19011391 A00...
Страница 55: ...Installation 54 Figure 2 21 Installing the ferrite clamp...
Страница 66: ...Wiring 65 3 3 2 Wiring Diagram for Torque Control Mode Figure 3 5 Wiring in the torque control mode...
Страница 111: ...Wiring 110 Open collector mode For use of the internal 24 V power supply of the servo drive...
Страница 113: ...Wiring 112 Scheme 2 Using the external resistor...
Страница 135: ...Wiring 134 Selecting the regenerative resistor Figure 3 48 Flowchart for selecting the regenerative resistor...
Страница 144: ...Maintenance 143...