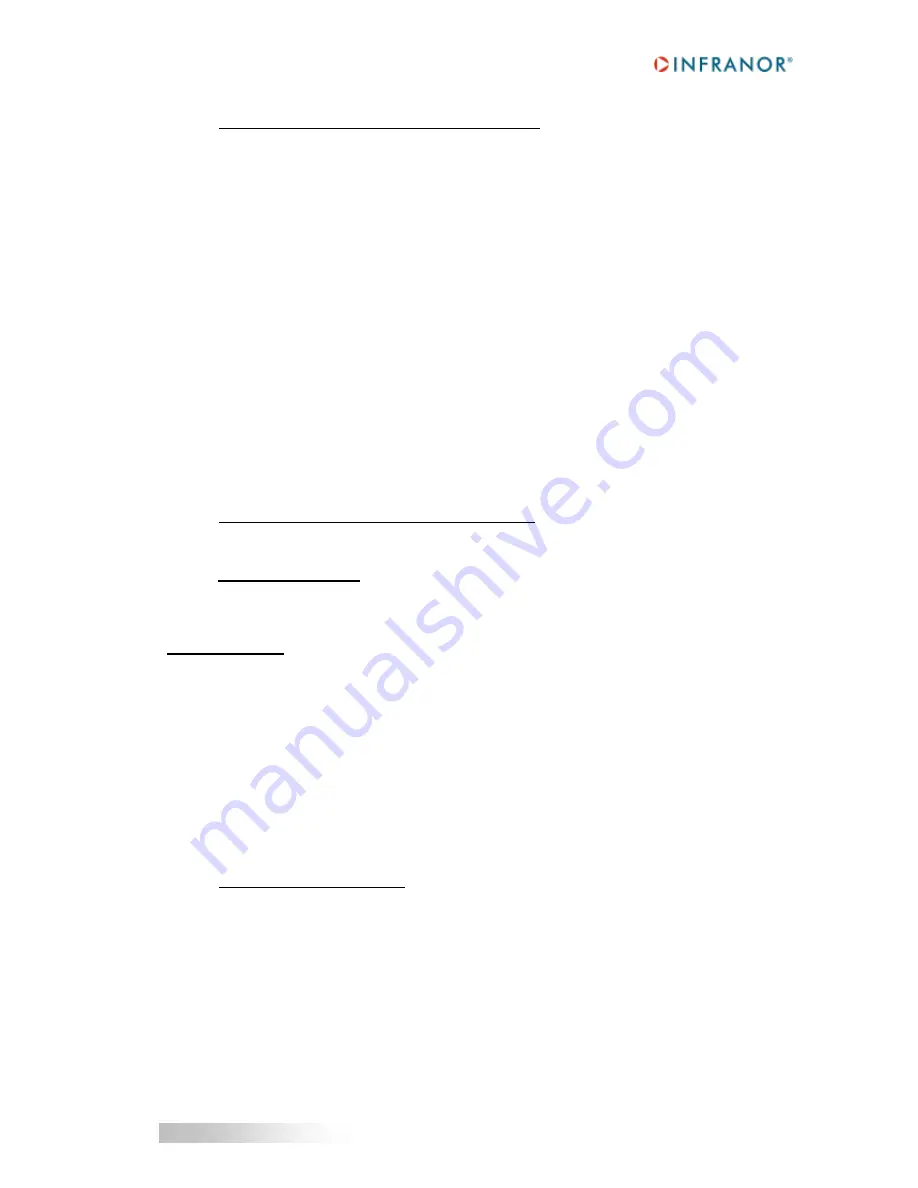
31
XtrapulsEasy
™-DB - Installation Guide
Chapter 5 - Appendix
C
-
UNUSUAL OPERATING ENVIRONMENT CONDITIONS
The use of the power converter, of its pertaining control system and of the servo in conditions which are
diverging from the usual ones defined by the IEC 60146-1-1 standard must be considered as abnormal.
These abnormal operating conditions must be specified by the purchaser.
Abnormal operating conditions as those listed below may require a special construction or special
protections. The conditions below must be notified if they are known or specified:
1. Exposure to corrosive gas.
2. Exposure to excessive moisture (relative moisture exceeding 85 %).
3. Exposure to excessive dust.
4. Exposure to abrasive dust.
5. Exposure to water steam or condensation.
6. Exposure to oil steam.
7. Exposure to explosive dust or gas mixtures.
8. Exposure to salt air.
9. Exposure to abnormal vibrations, shocks, jerking.
10. Exposure to inclemency or water dripping.
11. Exposure to unusual storing or freight conditions.
12. Exposure to sudden or rough temperature variations.
13. Abnormal exiguity of the available room.
14. Abnormal high nuclear radiations.
15. Altitude higher than 1000 m.
16. Long storage periods.
17. Outdoor equipment.
D
-
INSTALLATION, COMMISSIONING AND OPERATION
Normal and abnormal operating conditions apply the same way to installation, commissioning and use.
E
-
EQUIPMENT STORAGE
At receipt, the equipment must be immediately stored under adequate shelter. The transport
packaging is not suited to outdoor or non-protected storing.
Climatic conditions
Equipments must be stored in the environment conditions specified by the IEC 60721-3-1
standard. This includes:
1 -
Room temperature: class
1K4
-25°C to +55°C
2 -
Relative moisture: class 1K3
5% to 95%
Modules and panels must be protected against condensation. Rough temperature and moisture variations should
be avoided, as far as possible. If the temperature of the storing room is varying such as to subject the equipment
to condensation or to frost, the equipment must then be protected by a reliable heating system which will keep it at
a temperature slightly higher than the surrounding air temperature.
If the equipment has been subjected to a low temperature during a long time, it should not be unpacked before
having reached the surrounding air temperature, in order to avoid condensation. Such moisture in some parts of
the equipment may involve a faulty electric insulation.
F
-
PARTICULAR STORING RISKS
The following risks must be carefully considered:
1. Water: The equipment must be protected against rain, snow, rime, etc.
2. Altitude: The equipment should not be stored at an altitude higher than 3000m.
3. Corrosive agents: The equipment must be protected against salty sea spray, emanations of dangerous
gasses or corrosive liquids, etc…
4. Duration: the specifications of the above mentioned items are only valid for a total transport and
storage period of up to six months. Longer periods may require a special treatment (smaller
surrounding air temperature range such as in class 1K3).