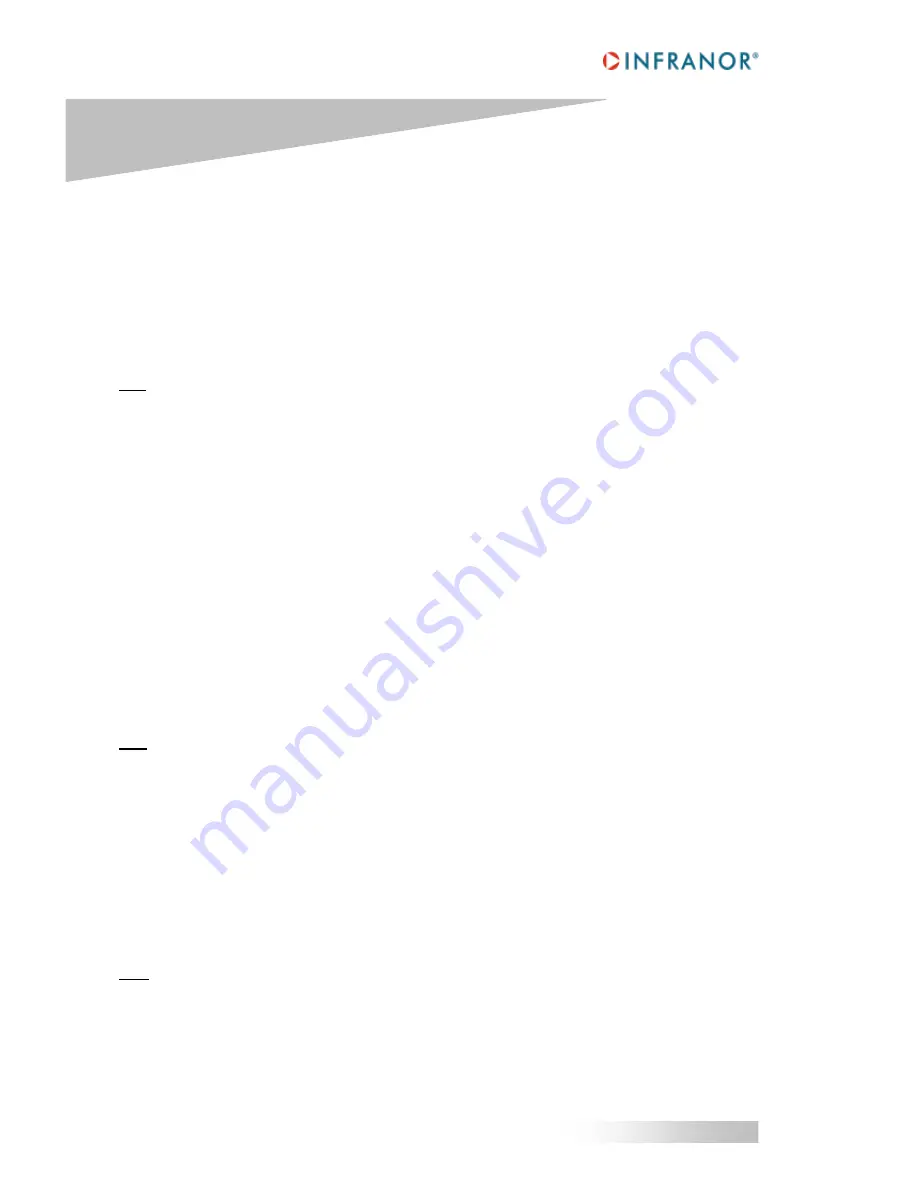
18
Chapter 4 - Connections
XtrapulsEasy
™-DB - Installation Guide
Chapter 4 - Design recommendations
4.1 - MOTHERBOARD DESIGN
4.1.1 - Copper section
The copper section for motor phases U V W and power source must be
at least 0.3mm²
on external layers.
However, in order to optimize the thermal behaviour (temperature rise less than 10°C), we recommend to
maximize the current ability of the design by:
-
Using at least 4-layer PCBs and at least 35µm finished copper thickness,
-
Using maximum trace width according to the connector pitch = 7mm.
Note: External layers allow a current 3 times higher than internal layers, thanks to natural convection.
On a multi-layer PCB, power trace patterns should be stacked to avoid coupling problems.
4.1.2 - Power and signal separation
Best practice is to keep a physical separation between power and low voltage signals on all stacked layers at the
same time:
-
It allows thermal separation,
-
It allows electrical separation.
To avoid coupling between low level signals and power traces, the following rules must be observed:
Never route together the power phases and the feedback signals.
Keep a GND trace between the power phases (or power source) and logic signals.
Differential signals (ex: CANOpen, Resolver) must be routed in respect of differential state of the art rules.
4.1.3 - External capacitors and decoupling
4.1.3.1 - 24V supply
A 220µF 35V aluminum capacitor placed on the host PCB near each drive is recommended for a 24V
decoupling.
Note:
The 24 V and power supply protection on source side must be ensured by the user.
4.1.3.2 - DC Bus Capacitors
At least, a 470µF /100V capacitor must be placed at the nearest of each drive.
If the DC bus power supply is provided by a battery, the energy reflected by the motor during deceleration phases
will recharge it.
Check the battery can support the max current reflected.
If the DC bus power supply is provided by a no current-reversible power supply (e.g. switch-mode power supply),
additional capacitors will be necessary.
Proceed by increasing the total amount of the DC bus capacitor bank until the overvoltage fault does not appear
anymore during deceleration phases.
Note: Emergency stops are generally the most regenerative phase since all axes decelerate simultaneously. A
protection diode may be necessary to avoid overvoltage on non-reversible supply.