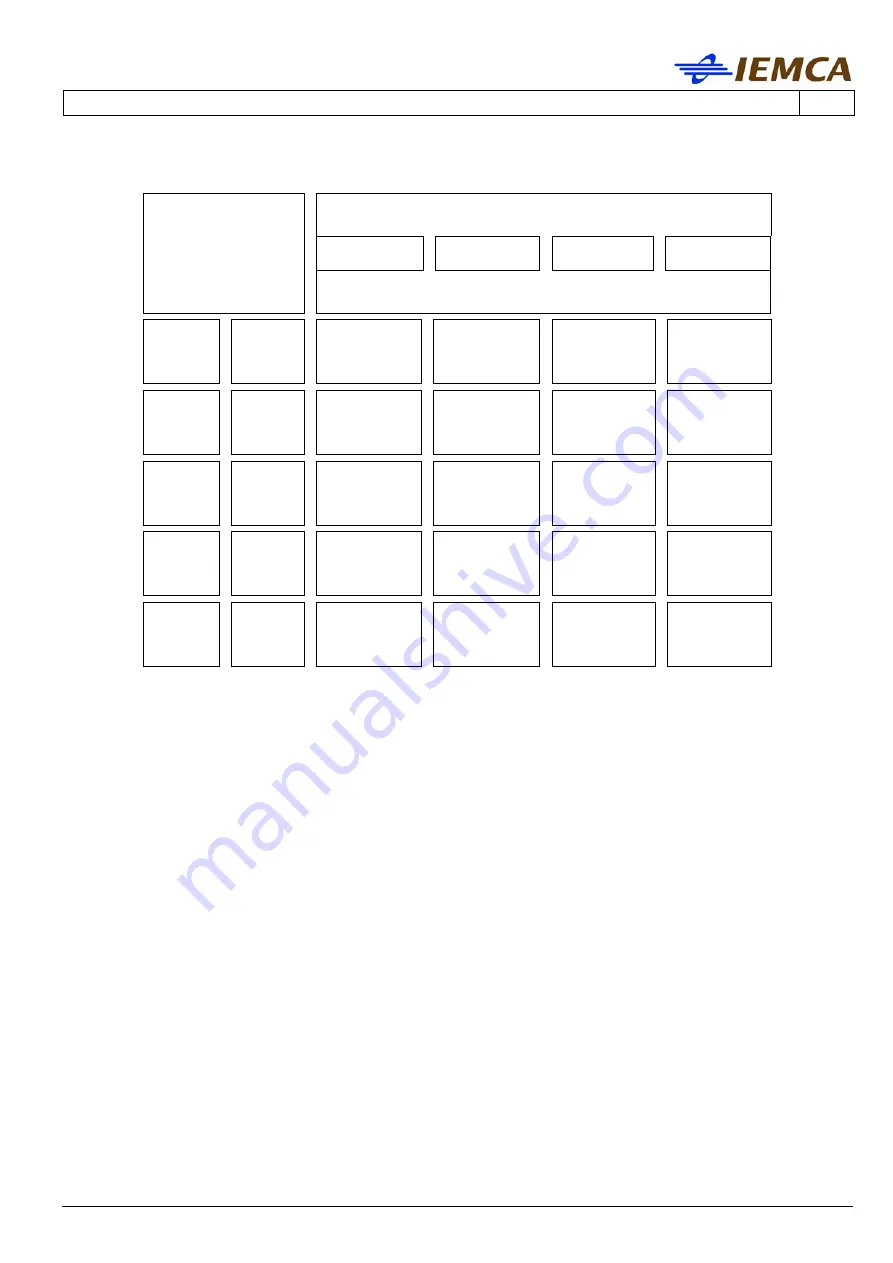
11 - COLLETS
Master 80 UP HyperFlexible
EN
11 - Pag. 9 / 9
Inch fraction
Inch fraction
1 2 3
4
Millimetres
11/16
45/64
23/32
47/64
0,687 5
0,703 125
0,718 75
0,734 375
17,462 5
17,859 4
18,256 2
18,653 1
42,862 5
43,259 4
43,656 2
44,053 1
68,262 5
68,659 4
69,056 2
69,453 1
93,662 5
94,059 4
94,456 2
94,853 1
3/4
49/64
25/32
51/64
0,75
0,765 625
0,781 25
0,796 875
19,050 0
19,446 9
19,843 8
20,240 6
44,450 0
44,846 9
45,243 8
45,640 6
69,850 0
70,246 9
70,643 8
71,040 6
95,250 0
95,646 9
96,043 8
96,440 6
13/16
53/64
27/32
55/64
0,812 5
0,828 125
0,843 75
0,859 375
20,637 5
21,034 4
21,431 2
21,828 1
46,037 5
46,434 4
46,831 2
47,228 1
71,437 5
71,834 4
72,231 2
72,628 1
96,837 5
97,234 4
97,631 2
98,028 1
7/8
57/64
29/32
59/64
0,875
0,890 625
0,906 25
0,921 875
22,225 0
22,621 9
23,018 8
23,415 6
47,625 0
48,021 9
48,418 8
48,815 6
73,025 0
73,421 9
73,818 8
74,215 6
98,425 0
98,821 9
99,218 8
99,615 6
15/16
61/64
31/32
63/64
0,937 5
0,953 125
0,968 75
0,984 375
23,812 5
24,209 4
24,606 2
25,003 1
49,212 5
49,609 4
50,006 2
50,403 1
74,612 5
75,009 4
75,406 2
75,803 1
100,012 5
100,409 4
100,806 2
101,203 1
b
Содержание Master 80 UP HyperFlexible
Страница 2: ......
Страница 4: ......
Страница 10: ......
Страница 16: ......
Страница 25: ...2 TECHNICAL INFORMATION Master 80 UP HyperFlexible EN 2 Pag 9 9 ...
Страница 36: ...EN 2 TECHNICAL INFORMATION Master 80 UP HyperFlexible 2 Pag 20 20 2 6 TECHNICAL DATA ...
Страница 44: ......
Страница 58: ......
Страница 66: ...EN 4 HANDLING AND INSTALLATION Master 80 UP HyperFlexible 4 Pag 8 8 tighten screws A and fit brackets B again ...
Страница 102: ......
Страница 106: ...EN 6 USE AND OPERATION Master 80 UP HyperFlexible 6 Pag 4 4 ...
Страница 127: ...7 BAR FEEDER MAINTENANCE Master 80 UP HyperFlexible EN 7 Pag 3 3 7 2 SCHEDULED MAINTENANCE Scheduled maintenance ...
Страница 132: ...EN 7 BAR FEEDER MAINTENANCE Master 80 UP HyperFlexible 7 Pag 8 8 7 3 LUBRICATION POINT DIAGRAM Oil ...
Страница 134: ...EN 8 TROUBLES CAUSES SOLUTIONS Master 80 UP HyperFlexible 8 Pag 2 2 ...
Страница 142: ......
Страница 174: ...EN 11 COLLETS Master 80 UP HyperFlexible 11 Pag 24 24 ...