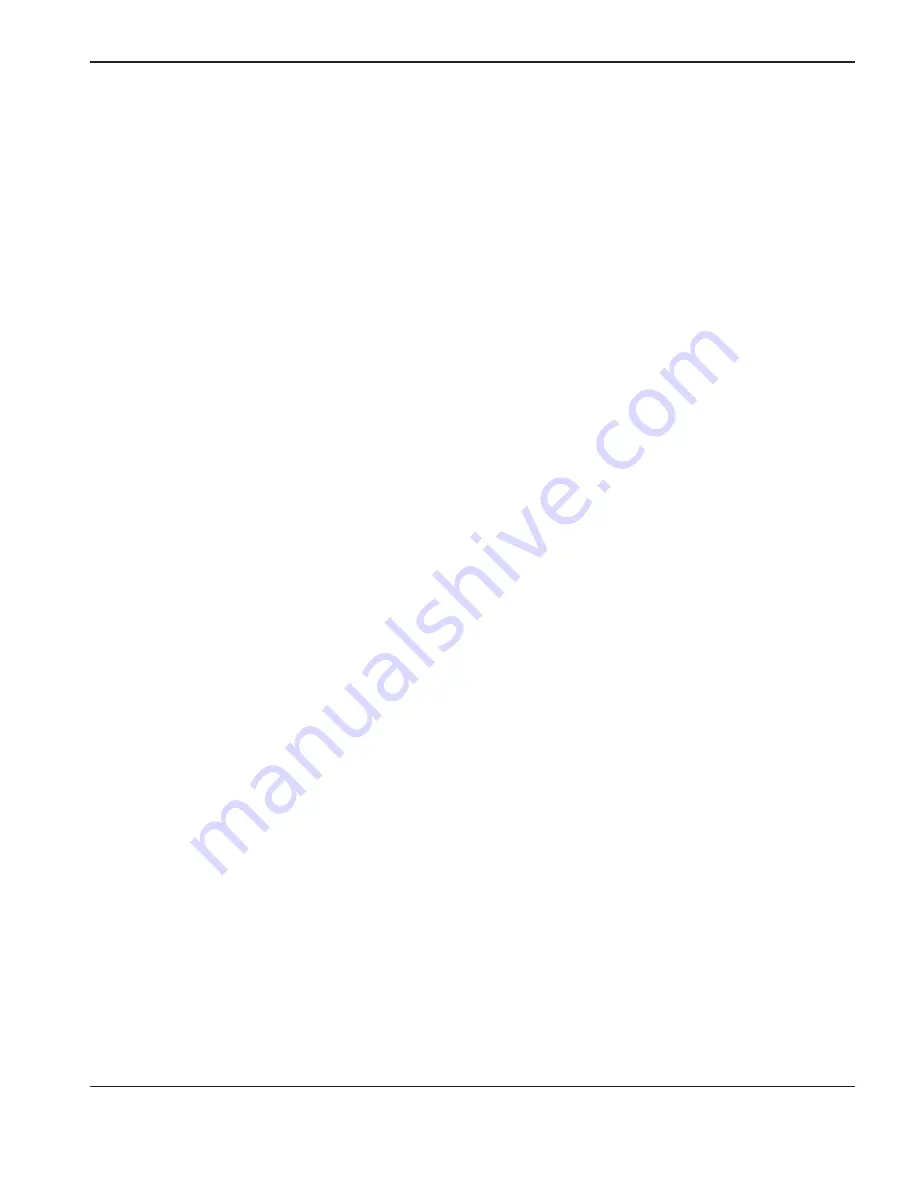
Parts
powermax
65/85
Operator Manual
6-13
Machine torch consumables
Part number
Description
Shielded
220817
Shield 45/65/85 A
220854
Retaining cap 45/65/85/105 A
220953
Ohmic retaining cap 45/65/85/105 A
220941
45 A Nozzle
220819
65 A Nozzle
220816
85 A Nozzle
220842
Electrode 45/65/85/105 A
220857
Swirl ring 65/85 A
Unshielded
220955
Deflector 65/85/105 A
220854
Retaining cap 45/65/85/105 A
220941
45 A Nozzle
220819
65 A Nozzle
220816
85 A Nozzle
220842
Electrode 45/65/85/105 A
220857
Swirl ring 65/85 A
Gouging
220798
Gouging shield 65/85/105 A
220854
Retaining cap 45/65/85/105 A
220797
Gouging nozzle 65/85 A
220842
Electrode 45/65/85/105 A
220857
Swirl ring 65/85 A
FineCut
1
220955
Deflector 65/85/105 A
220948
FineCut shield
220854
Retaining cap 45/65/85/105 A
220953
Ohmic retaining cap 45/65/85/105 A
220930
FineCut Nozzle
220842
Electrode 45/65/85/105 A
220857
Swirl ring 65/85 A
1
The deflector (220955) is used only with the standard retaining cap (220854). The shield (220948) is used only with
the ohmic retaining cap (220953).
Содержание powermax65
Страница 1: ...Plasma arc cutting systems Operator Manual 806650 Revision 2 ...
Страница 10: ...vi powermax65 85 Operator Manual ...
Страница 14: ...Table of Contents x powermax65 85 Operator Manual ...
Страница 30: ...Specifications 1 16 powermax65 85 Operator Manual ...
Страница 150: ...Parts 6 16 powermax65 85 Operator Manual ...