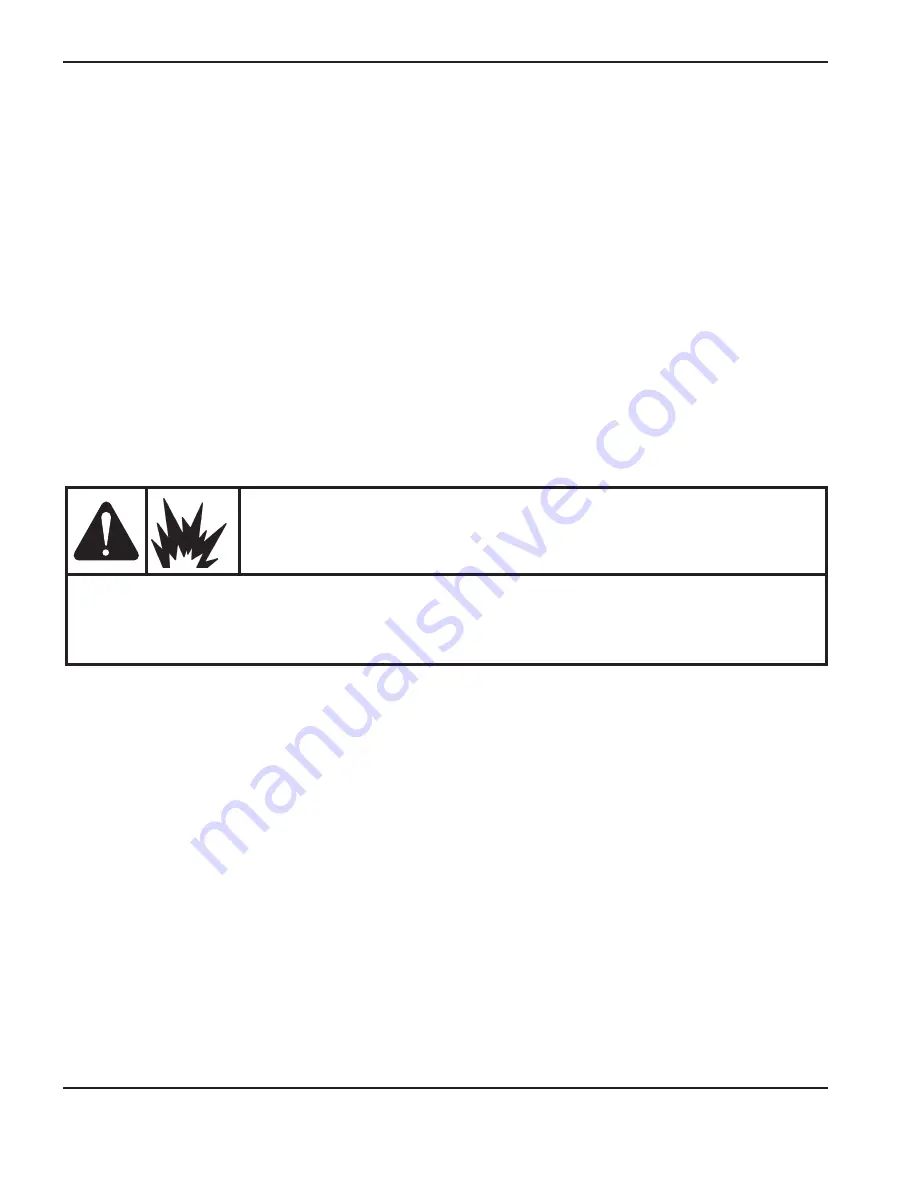
OperatiOn
4-28
HPR130XD Auto Gas –
806330 Revision 2
Underwater cut charts
overview
Hypertherm has developed underwater cut charts for 80 A, 130 A, 200 A, 260 A, and 400 A mild steel processes.
These underwater cut charts are designed to produce optimal results for cutting mild steel up to 75 mm (3 inches)
below the surface of the water.
benefits and trade-offs
Underwater cutting can significantly reduce the level of noise and smoke generated by normal plasma cutting, as well
as the glare of the plasma arc. Underwater operation provides the maximum possible noise suppression over the widest
possible range of current levels. For example, you can expect noise levels to stay below 70 decibels for many processes
when cutting up to 75 mm (3 inches) below the surface of the water. Operators can expect exact noise levels to vary
depending on the table design and the cutting application being used.
However, underwater cutting can limit the visual and auditory signals that experienced operators may use while cutting
to ensure they are getting a high quality cut and the cutting process is proceeding as it should. Underwater cutting can
also affect the cut edge quality, resulting in a rougher surface finish with increased dross levels.
wARNINg!
Explosion hazard – underwater cutting with fuel gases or aluminum
Do not cut under water with fuel gases containing hydrogen. Do not cut aluminum alloys underwater or
on a water table unless you can prevent the accumulation of hydrogen gas.
Doing so can result in an explosive condition that can detonate during plasma cutting operations.
All underwater processes (80–400 A) use consumables that are designed for standard (straight) cutting, when the
torch is perpendicular to the workpiece.
Requirements and restrictions
•
These processes are specifically designed for cutting mild steel up to 75 mm (3 inches) below the surface of
the water. Do not attempt to cut in water if the surface of the workpiece is deeper than 75 mm (3 inches).
•
The True Hole™ process is not compatible with underwater cutting. If you are using a water table with the True
Hole process, the water level should be at least 25 mm (1 inch) below the bottom surface of the workpiece.
•
Preflow must be on during initial height sense (IHS) for all underwater cutting.
•
Ohmic contact cannot be used for underwater cutting.
Operators should disable ohmic contact from the CNC. For example, if you are using a Hypertherm CNC and torch
height control (THC) system, you can disable ohmic contact sensing by switching the Nozzle Contact IHS setting to
OFF. The system then defaults to stall force sensing as a backup for torch height control.
Содержание HyPerformance HPR130XD
Страница 1: ...HyPerformance Plasma HPR130XD Auto gas Instruction manual 806330 Revision 3 ...
Страница 16: ...Table of Contents viii HPR130XD Auto Gas 806330 ...
Страница 26: ...Specifications 2 2 HPR130XD Auto Gas 806330 ...
Страница 38: ...Specifications 2 14 HPR130XD Auto Gas 806330 ...
Страница 48: ...Installation 3 10 HPR130XD Auto Gas 806330 ...
Страница 51: ...Installation HPR130XD Auto Gas 806330 3 13 LHF mounting Horizontal RHF mounting Vertical RHF mounting ...
Страница 59: ...Installation HPR130XD Auto Gas 806330 3 21 1X1 J103 J300 Female Male 5 6 5 6 3X1 3X2 3X3 3X4 ...
Страница 61: ...Installation HPR130XD Auto Gas 806330 3 23 7 Caution Never use PTFE tape on any joint preparation ...
Страница 94: ...Installation 3 56 HPR130XD Auto Gas 806330 ...
Страница 101: ...Operation HPR130XD Auto Gas 806330 Revision 2 4 7 Diagnostics screen ...
Страница 102: ...Operation 4 8 HPR130XD Auto Gas 806330 Revision 2 Test screen ...
Страница 103: ...Operation HPR130XD Auto Gas 806330 Revision 2 4 9 Cut chart screen ...
Страница 152: ...Operation 4 58 HPR130XD Auto Gas 806330 Revision 2 ...
Страница 236: ...7 4 HPR130XD Auto Gas 806330 Discrete output functionality ...
Страница 294: ...Appendix B CNC Interface Protocol b 28 HPR130XD Auto Gas 806330 Revision 1 ...
Страница 302: ...4 HPR130XD Auto Gas 806330 ...