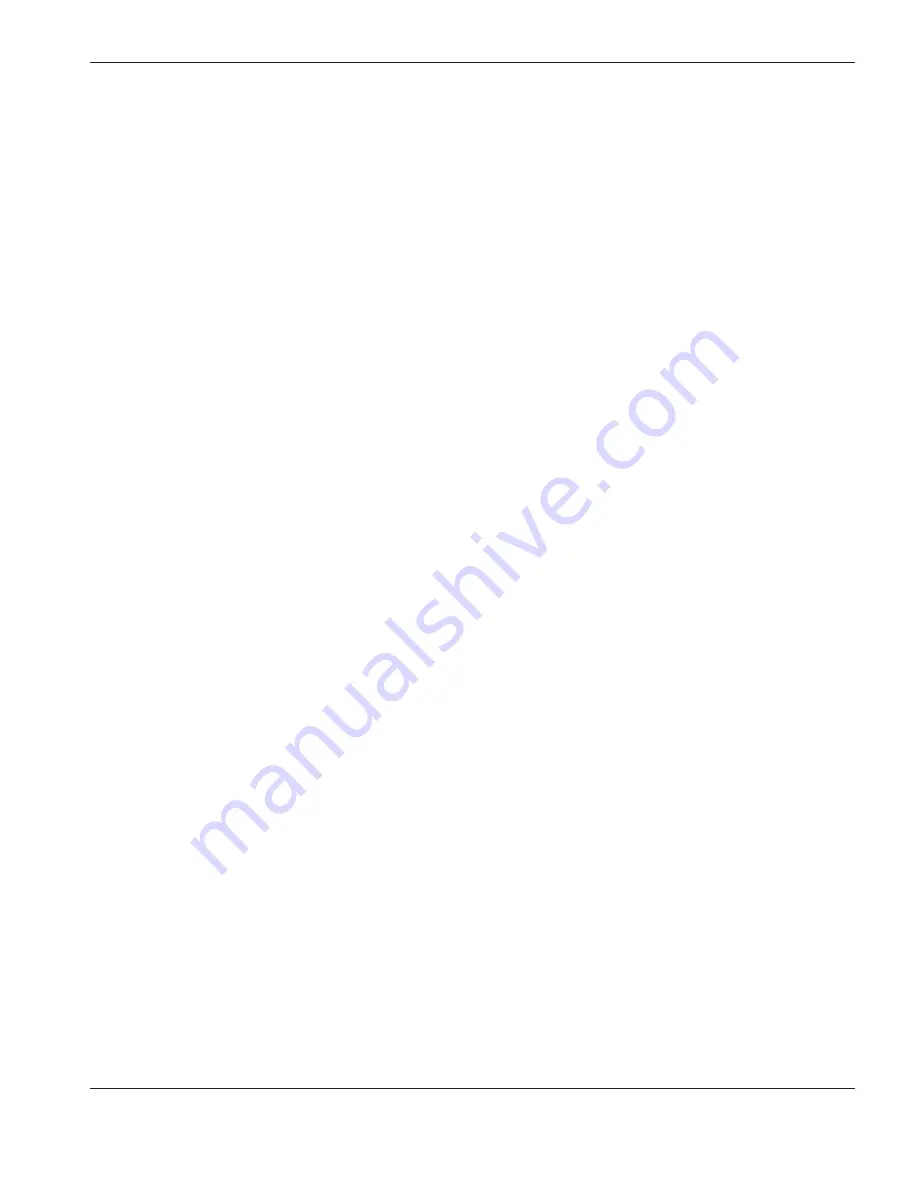
InstallatIon
HPR130XD Auto Gas –
806330
3-7
cable from the far motor to the gantry bus bar. The gantry bus bar should have a separate, heavy EMI ground
cable 21.2 mm
2
(4 AWG; 047031) to the table bus bar. The EMI ground cables for the torch lifter and the
RHF console must each run separately to the table ground bus.
3. A ground rod that meets all applicable local and national electrical codes must be installed within 6 m (20 ft)
of the cutting table. This is a PE ground and should be connected to the cutting table ground bus bar using
13.3 mm
2
(6 AWG) green and yellow grounding cable (047121) or equivalent.
4. For the most effective shielding, use the Hypertherm CNC interface cables for I/O signals, serial
communication signals, between plasma systems in multi-drop connections, and for interconnections between
all parts of the Hypertherm system.
5. All hardware used in the ground system must be brass or copper. While you can use steel studs welded to
the cutting table for mounting the ground bus, no other aluminum or steel hardware can be used in the ground
system.
6. AC power, PE, and service grounds must be connected to all equipment according to local and national
codes.
7. For a system with a remote high frequency console (RHF), the positive, negative, and pilot arc leads should
be bundled together for as long a distance as possible. The torch lead, work lead, and the pilot arc (nozzle)
leads may be run parallel to other wires or cables only if they are separated by at least 150 mm (6 inches).
If possible, run power and signal cables in separate cable tracks.
8. For a system with an RHF console, the ignition console should be mounted as closely as possible to the torch,
and must have a separate ground cable that connects directly to the cutting table ground bus bar.
9. Each Hypertherm component, as well as any other CNC or motor drive cabinet or enclosure, must have a
separate ground cable to the common (star) ground on the table. This includes the ignition console, whether
it is bolted to the plasma system or to the cutting table.
10. The metal braided shield on the torch lead must be connected fi rmly to the ignition console and to the torch.
It must be electrically insulated from any metal and from any contact with the fl oor or building. The torch lead
can be run in a plastic cable tray or track, or covered with a plastic or leather sheath.
11. The torch holder and the torch breakaway mechanism – the part mounted to the lifter, not the part mounted
to the torch – must be connected to the stationary part of the lifter with copper braid at least 12.7 mm
(0.5 inches) wide. A separate cable must run from the lifter to the gantry ground bus bar. The valve assembly
should also have a separate ground connection to the gantry ground bus bar.
12. If the gantry runs on rails that are not welded to the table, then each rail must be connected with a ground
cable from the end of the rail to the table. The rail ground cables connect directly to the table and do not need
to connect to the table ground bus bar.
13. If you are installing a voltage divider board, mount it as closely as possible to where the arc voltage is
sampled. One recommended location is inside the plasma system enclosure. If a Hypertherm voltage divider
board is used, the output signal is isolated from all other circuits. The processed signal should be run in
twisted shielded cable (Belden 1800F or equivalent). Use a cable with a braided shield, not a foil shield.
Connect the shield to the chassis of the plasma system and leave it unconnected at the other end.
14. All other signals (analog, digital, serial, and encoder) should run in twisted pairs inside a shielded cable.
Connectors on these cables should have a metal housing. The shield, not the drain, should be connected to
the metal housing of the connector at each end of the cable. Never run the shield or the drain through the
connector on any of the pins.
Содержание HyPerformance HPR130XD
Страница 1: ...HyPerformance Plasma HPR130XD Auto gas Instruction manual 806330 Revision 3 ...
Страница 16: ...Table of Contents viii HPR130XD Auto Gas 806330 ...
Страница 26: ...Specifications 2 2 HPR130XD Auto Gas 806330 ...
Страница 38: ...Specifications 2 14 HPR130XD Auto Gas 806330 ...
Страница 48: ...Installation 3 10 HPR130XD Auto Gas 806330 ...
Страница 51: ...Installation HPR130XD Auto Gas 806330 3 13 LHF mounting Horizontal RHF mounting Vertical RHF mounting ...
Страница 59: ...Installation HPR130XD Auto Gas 806330 3 21 1X1 J103 J300 Female Male 5 6 5 6 3X1 3X2 3X3 3X4 ...
Страница 61: ...Installation HPR130XD Auto Gas 806330 3 23 7 Caution Never use PTFE tape on any joint preparation ...
Страница 94: ...Installation 3 56 HPR130XD Auto Gas 806330 ...
Страница 101: ...Operation HPR130XD Auto Gas 806330 Revision 2 4 7 Diagnostics screen ...
Страница 102: ...Operation 4 8 HPR130XD Auto Gas 806330 Revision 2 Test screen ...
Страница 103: ...Operation HPR130XD Auto Gas 806330 Revision 2 4 9 Cut chart screen ...
Страница 152: ...Operation 4 58 HPR130XD Auto Gas 806330 Revision 2 ...
Страница 236: ...7 4 HPR130XD Auto Gas 806330 Discrete output functionality ...
Страница 294: ...Appendix B CNC Interface Protocol b 28 HPR130XD Auto Gas 806330 Revision 1 ...
Страница 302: ...4 HPR130XD Auto Gas 806330 ...