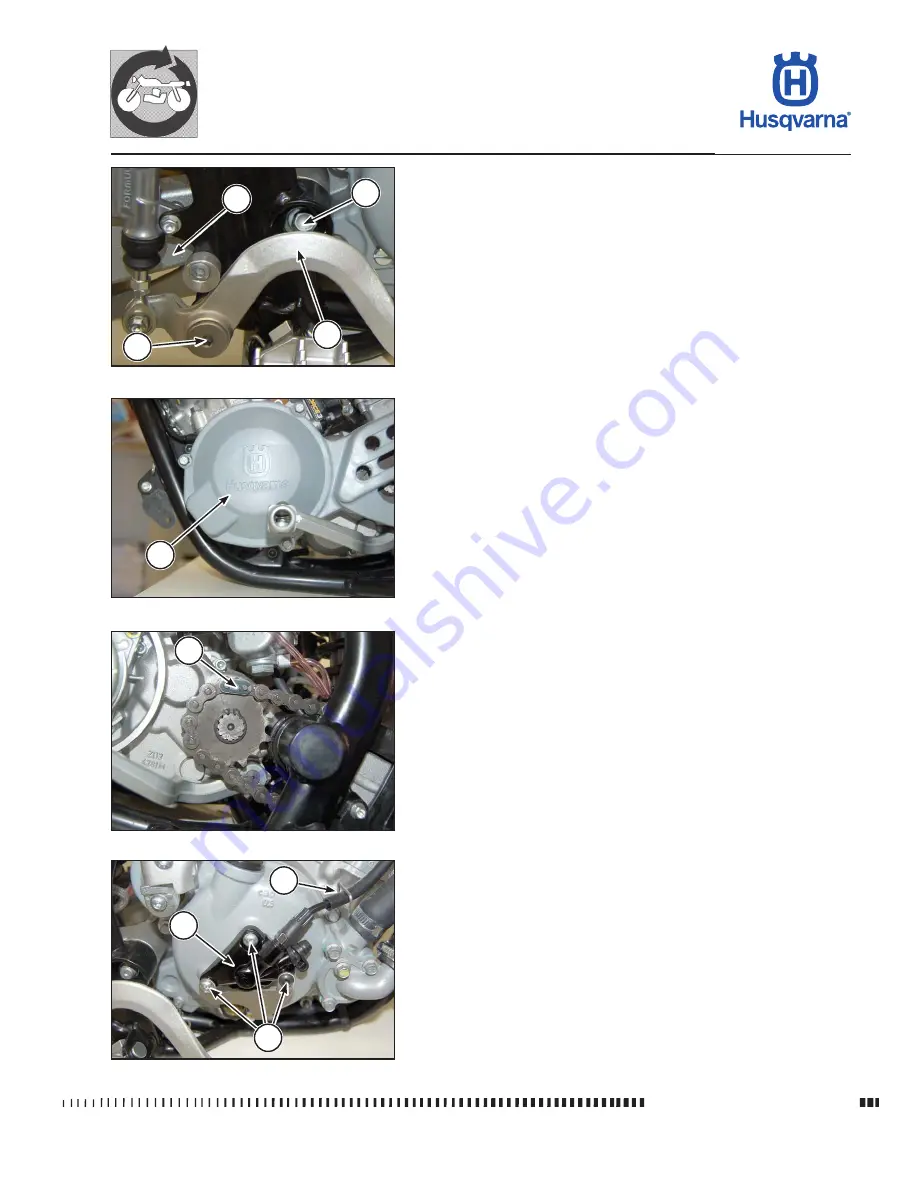
E.13
CR 65 2012
3
4
B
A
1
2
1
2
3
GENERAL PROCEDURES
Workshop Manual Ed. 09-2011
- After releasing the brake pedal (B) loosen the chassis retaining screw (4),
using a 17 mm socket wrench on the left, and a 14 mm one on the right to
remove the nut (2) of the swinging arm pivot (3) and the swinging arm (A)
itself.
Secondary drive chain removal
- Remove the case cover (1) to access the drive chain.
- Use needle-nose pliers to remove the master link (2) and open the drive
chain.
Clutch actuator removal
- Remove the whole actuator (1) removing the three screws (2) that fasten it
to the clutch cover, and release the pipe from the ring (3) that retains it to the
engine.
Содержание CR 65 2012
Страница 1: ...CR 65 2012 Workshop Manual Ed 09 2011 ...
Страница 6: ......
Страница 7: ...b 1 CR 65 2012 b Workshop Manual Ed 09 2011 IMPORTANT NOTICES Section ...
Страница 9: ...A 1 CR 65 2012 A Workshop Manual Ed 09 2011 GENERAL INFORMATION Section ...
Страница 14: ......
Страница 15: ...B 1 CR 65 2012 B Workshop Manual Ed 09 2011 MAINTENANCE Section ...
Страница 19: ...C 1 CR 65 2012 C Workshop Manual Ed 09 2011 TROUBLESHOOTING Section ...
Страница 24: ......
Страница 25: ...D 1 CR 65 2012 D Workshop Manual Ed 09 2011 SETTINGS AND ADJUSTMENTS Section ...
Страница 27: ...D 3 CR 65 2012 Workshop Manual Ed 09 2011 SETTINGS AND ADJUSTMENTS CR 65 ...
Страница 48: ......
Страница 49: ...E 1 CR 65 2012 E GENERAL PROCEDURES Workshop Manual Ed 09 2011 Section ...
Страница 63: ...F 1 CR 65 2012 ENGINE DISASSEMBLY Workshop Manual Ed 09 2011 Section F ...
Страница 73: ...G 1 CR 65 2012 ENGINE OVERHAUL Workshop Manual Ed 09 2011 Section G ...
Страница 86: ......
Страница 87: ...H 1 CR 65 2012 ENGINE REASSEMBLY Workshop Manual Ed 09 2011 Section H ...
Страница 98: ......
Страница 99: ...I 1 CR 65 2012 I FRONT SUSPENSION Workshop Manual Ed 09 2011 Section ...
Страница 105: ...J 1 CR 65 2012 J REAR SUSPENSION Workshop Manual Ed 09 2011 Section ...
Страница 113: ...L 1 CR 65 2012 L BRAKES Workshop Manual Ed 09 2011 Section ...
Страница 122: ......
Страница 123: ...M 1 CR 65 2012 M ELECTRICAL SYSTEM Workshop Manual Ed 09 2011 Section ...
Страница 131: ...N 1 CR 65 2012 N ENGINE COOLING Workshop Manual Ed 09 2011 Section ...
Страница 136: ......
Страница 137: ...P 1 CR 65 2012 Workshop Manual Ed 09 2011 HYDRAULICALLY CONTROLLED CLUTCH Section P ...
Страница 142: ......
Страница 143: ...S 1 CR 65 2012 Workshop Manual Ed 09 2011 FUEL SUPPLY Section S ...
Страница 154: ......
Страница 155: ...W 1 CR 65 2012 W SPECIAL TOOLS Workshop Manual Ed 09 2011 Section ...
Страница 163: ...Y 1 CR 65 2012 Y CHASSIS AND WHEELS Workshop Manual Ed 09 2011 Section ...