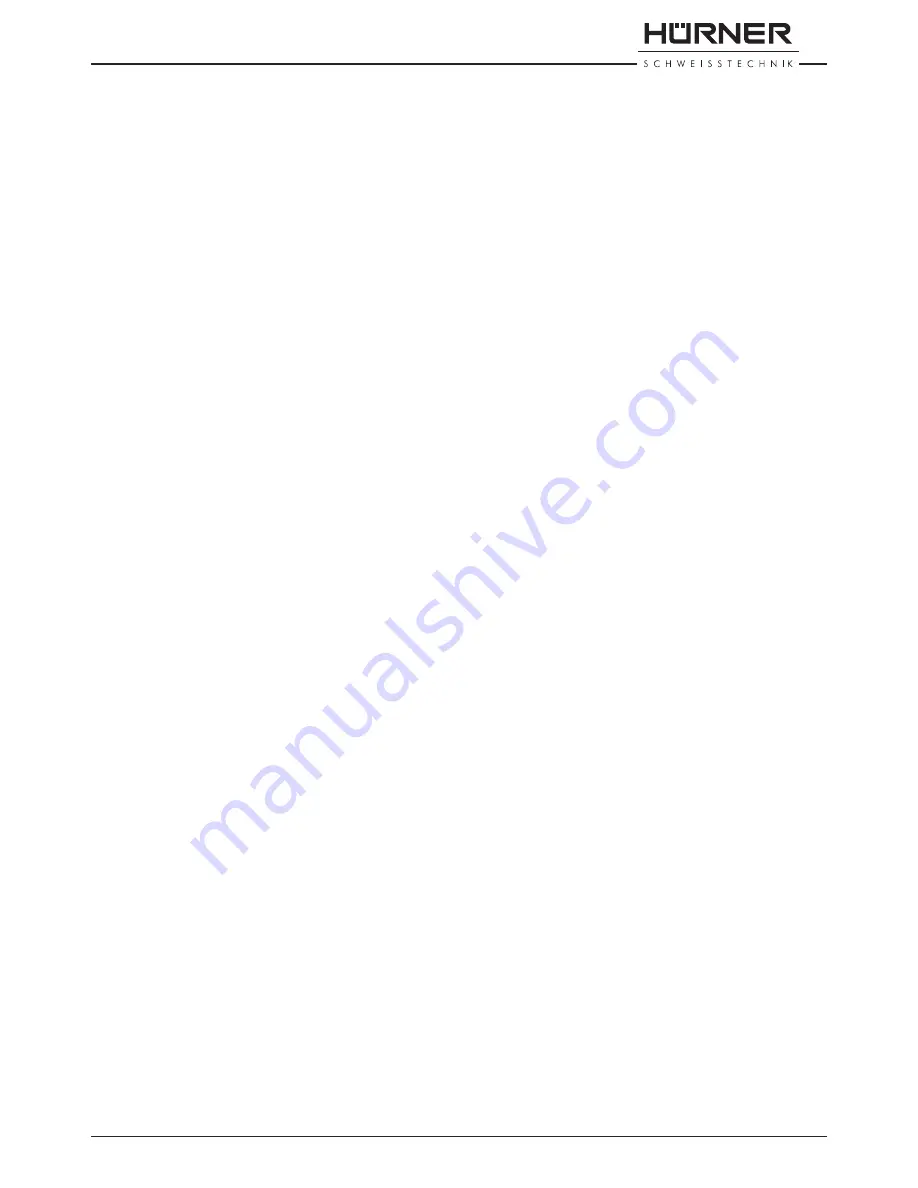
Version January 2009
EN
7
HST300 User’s Manual
H Ü R N E R S c h w e i s s t e c h n i k G m b H
Nieder-Ohmener Str.
35325 Mücke, Germany
During the welding process no further devices should be connected and
operated through the same generator.
2.10 Welding Report Integrity in Memory
When transferring welding reports to a printer, PC, or USB stick, always
be sure to wait until the display shows the “Printing finished” message
before you disconnect the printer, PC, or USB stick from the unit. If you
disconnect it too early, the welding unit may ask you whether you want to
delete the reports in memory, although they were not properly transferred
or printed. In this case, if you delete the contents of the report memory,
the welding reports would be irrevocably lost and would not have been
saved elsewhere.
3
Service and Repair
As the machine is used in applications that are sensitive to safety con-
siderations, it may be serviced and repaired only on our premises or by
partners who were specifically trained and authorized by us. Thus, con-
stantly high standards of operation quality and safety are maintained.
IMPORTANT!
Non-compliance with this provision will dispense the manufacturer from
any warranty and liability claims for the unit and any consequential
damage.
When serviced, the unit is automatically upgraded to the technical
specifications with which the product is currently shipped, and we grant
a three-months functional warranty on the serviced unit.
We recommend having the device serviced at least every twelve
months.
In Germany, keep in mind the inspection interval according to BGV A3!
3.1 Transport, Storage, Shipment
The HST300
Pricon
+ is shipped in a transport box. Store the HST300
Pri-
con
+ in the box, dry and protected from humidity.
When sending the welding unit, it should be placed into the transport
box at all times.
4
Principles of Operation
The HST300
Pricon
+ allows welding electrofusion fittings that feature a
bar code. Every fitting is provided with a tag with one or two bar codes
on it. The structure of this code is internationally standardized. The first
code, encoding the data on proper welding, complies with ISO TR 13950,
the second code, if present, encoding the component traceability data,
complies with ISO 12176-4.
The welding control program supports the extended data encoding speci-
fications under the ISO 12176-4 standard, e.g., pipe and fitting traceability
codes. To use them, switch the unit to ISO Mode (see section 10.1).
Further, the unit gives you the possibility to capture the so-called geo data
of a joint. With this feature, you can record the exact geographic location
of a joint using a satellite receiver, and save it to the welding report for
future reference, e.g., for planning future pipeline maintenance work.