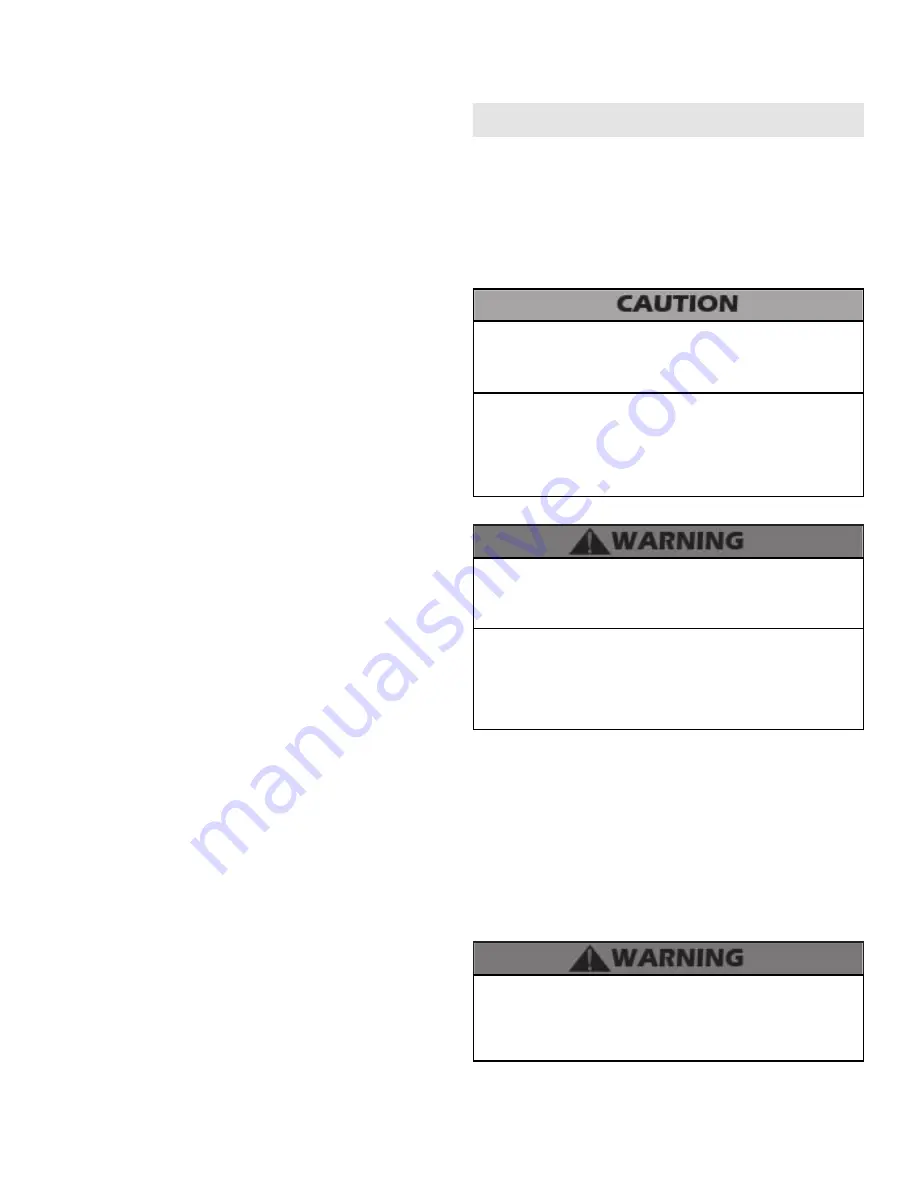
lp-445-r4 Rev. 006 Rel. 027 Date 7.21.20
7
Gas Valve
Senses suction from the blower, allowing gas to flow only if powered
and combustion air is flowing.
Integrated Venturi (500 Models) or Swirl Plate (700/850 Models)
Controls air and gas flow into the burner.
Burner
The high grade stainless steel burner uses premixed air and gas to
provide a wide range of firing rates.
Spark Ignition
The burner is ignited by applying high voltage through the system
spark electrode. The spark from the electrode ignites mixed gas off
of the burner.
Supply Water Temperature Sensor
This sensor monitors the boiler outlet water temperature (System
Supply). The control adjusts boiler firing rate so the supply
temperature will match the boiler set point.
Return Water Temperature Sensor
This sensor monitors boiler return water temperature (System
Return).
Temperature and Pressure Gauge
Allows the user to monitor system temperature and pressure.
Electrical field connections with terminal strips
The electrical cover allows easy access to the clearly marked line
voltage and low voltage terminal strips to facilitate wiring the boiler.
Condensate Collection System
This boiler is a high efficiency appliance and will produce condensate.
The condensate collection system has a float switch which monitors
condensate level and prevents condensate from backing up into
the combustion system. Inside the collection system is a built in trap
which seals the combustion system from the connected drain. This
condensate should be neutralized to avoid damage to the drainage
system or piping.
Flow Protection
The optional flow switch is designed to protect the boiler during low
flow conditions. The boiler control also monitors flow through the
heat exchanger by monitoring the return and supply sensors and
will shut down the burner before overheating occurs.
Outdoor Sensor
The control adjusts unit set point based on the outdoor temperature
measured by this sensor to provide greater efficiency.
System Sensor (Optional)
This sensor is designed to be used in a cascade system. The
system pipe sensor measures the temperature of return water and
communicates with the control system to modulate the firing rate of
the connected boilers.
NOTE:
When using a system sensor, pipe insulation must be
wrapped around it to improve temperature measurement accuracy
and increase overall system efficiency.
0-10 Volt Input
Allows the installer to connect a BMS (Building Management
System) to control the boiler.
Indirect Tank Sensor (optional)
Monitors storage tank temperature.
C. Optional Equipment
Optional equipment available from HTP (and Part #):
• System Sensor (7250P-324)
• Indirect Tank Sensor (7250P-325)
• 4” Stainless Steel Vent Termination Kit (V2000)
• 6” Stainless Steel Vent Termination Kit (V3000)
• High and Low Gas Pressure Switch Kit with Manual Reset
(7350P-600)
• UL 353 Compliant Low Water Cut-Off Interface Kit with
Manual Reset (7350P-601)
• Alarm System (to monitor any failure) (7350P-602)
• PC Connection Kit (7250P-320)
• Condensate Neutralizer (7350P-611)
• Caster Kit (7350p-604)
• Stacking Kit (7350P-603)
• Flow Switch Kit (7350P-605)
COLD WEATHER HANDLING
- If the boiler has been stored in a very
cold location (BELOW 0
o
F) before installation, handle with care until
the components come to room temperature. Failure to do so could
result in damage to the boiler.
Carefully consider installation when determining boiler location.
Please read the entire manual before attempting installation. Failure
to properly take factors such as boiler venting, piping, condensate
removal, and wiring into account before installation could result in
wasted time, money, and possible property damage and personal
injury.
This boiler is certified for indoor use only. DO NOT INSTALL
OUTDOORS. Outdoor installations ARE NOT covered by warranty.
Failure to install the boiler indoors could result in property damage,
severe personal injury, or death.
A. Locating the Boiler
Incorrect ambient conditions can lead to damage to the heating
system and put safe operation at risk. Ensure that the installation
location adheres to the information included in this manual. Failure
to do so could result in property damage, serious personal injury, or
death. Failure of boiler or components due to incorrect operating
conditions IS NOT covered by product warranty.
Part 3 - Prepare the Boiler
Remove all sides of the shipping crate to allow the boiler to be moved
into its installation location. Pick the boiler up by the lifting rings to
avoid damage to the boiler enclosure. Use either solid 3/4” diameter
black iron pipe or lifting straps to lift the boiler off its shipping crate.
The boiler is heavy. At least two individuals are needed to properly
handle the boiler. The boiler is also equipped with leveling feet that
can be used to level the boiler properly on an uneven location surface.
If surface flooring is rough, take care when moving the boiler into
position, as catching the leveling feet could damage the boiler.
1. Installation Area (Mechanical Room) Operating Conditions
• Ensure ambient temperatures are higher than 32
o
F / 0
o
C and
lower than 104
o
F / 40
o
C
• Prevent the air from becoming contaminated by the products,
places, and conditions listed in this manual
• Avoid continuously high levels of humidity
• Never close existing ventilation openings
• Ensure a minimum 1” clearance around hot water and exhaust
vent pipes
• NOTE:
To prevent condensing in the fan, it is recommended to
avoid prolonged exposure to temperatures below 45
o
F
This boiler has a condensate disposal system that may freeze if
exposed to sustained temperatures below 32
o
F. Precautions should
be taken to protect the condensate trap and drain lines from
sustained freezing conditions. Failure to take precautions could
result in property damage, severe personal injury, or death.
2. Check for nearby connections to:
• System water piping
• Venting connections
• Gas supply piping
Содержание MODCON500 FS
Страница 34: ...lp 445 r4 Rev 006 Rel 027 Date 7 21 20 34 Figure 26 Cascade Master and Follower Wiring ...
Страница 61: ...lp 445 r4 Rev 006 Rel 027 Date 7 21 20 61 Figure 34 Water Side Replacement Parts All Models ...
Страница 62: ...lp 445 r4 Rev 006 Rel 027 Date 7 21 20 62 Figure 35 Cabinet Replacement Parts All Models See Table ...
Страница 65: ...lp 445 r4 Rev 006 Rel 027 Date 7 21 20 65 Maintenance Notes ...